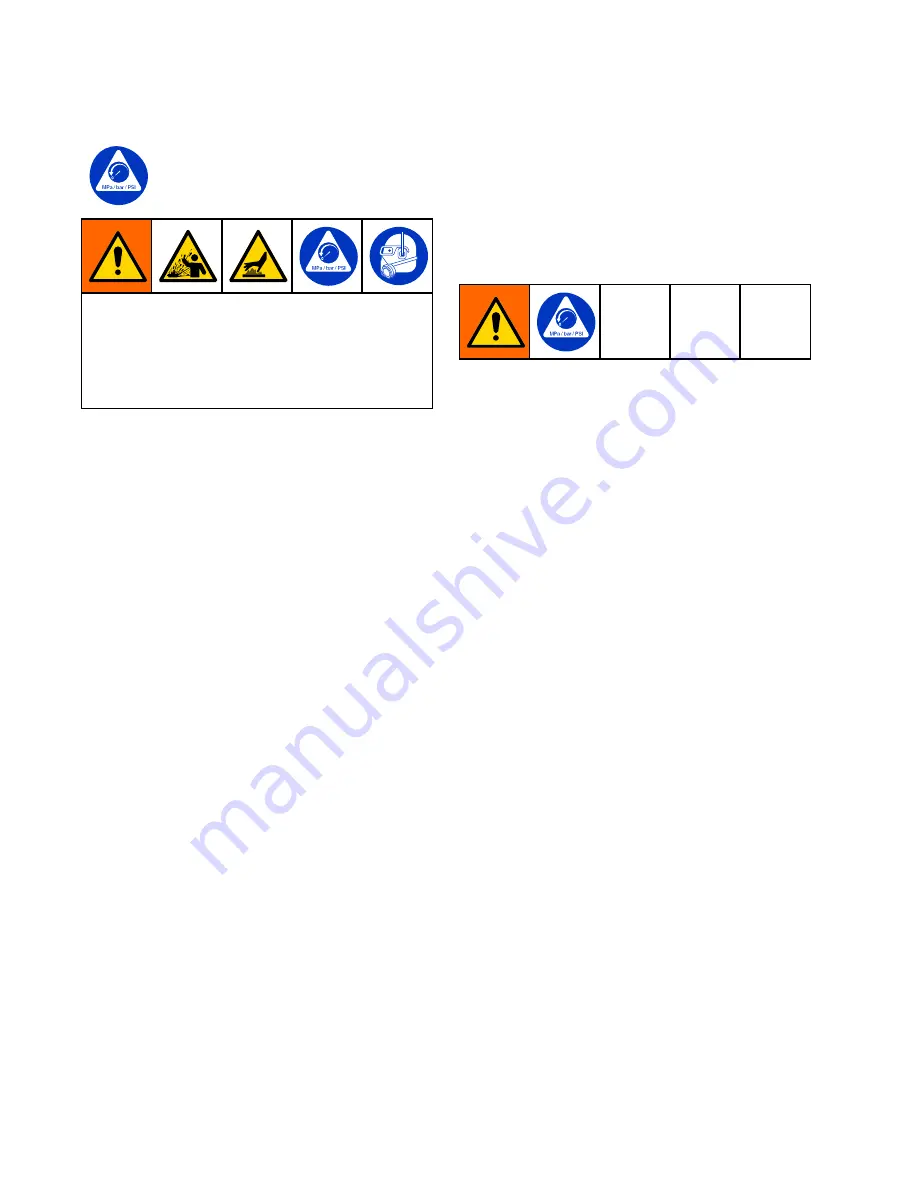
Pressure
Pressure
Pressure Relief
Relief
Relief Procedure
Procedure
Procedure
Follow the Pressure Relief Procedure
whenever you see this symbol.
This equipment stays pressurized until pressure
is relieved manually. To help prevent serious
injury from pressurized fluid, such as splashing
in the eyes or on skin, follow the Pressure Relief
Procedure when you stop pumping and before you
clean, check, or service the equipment.
1.
Shut off the air supply to the pump.
2.
Open the dispensing valve, if used.
3.
Open the fluid drain valve to relieve fluid
pressure. Have a container ready to catch the
drainage.
Pump
Pump
Pump Shutdown
Shutdown
Shutdown
At the end of the work shift and before you check,
adjust, clean, or repair the system, follow the
Pressure Relief Procedure, page 14
.
14
334793A