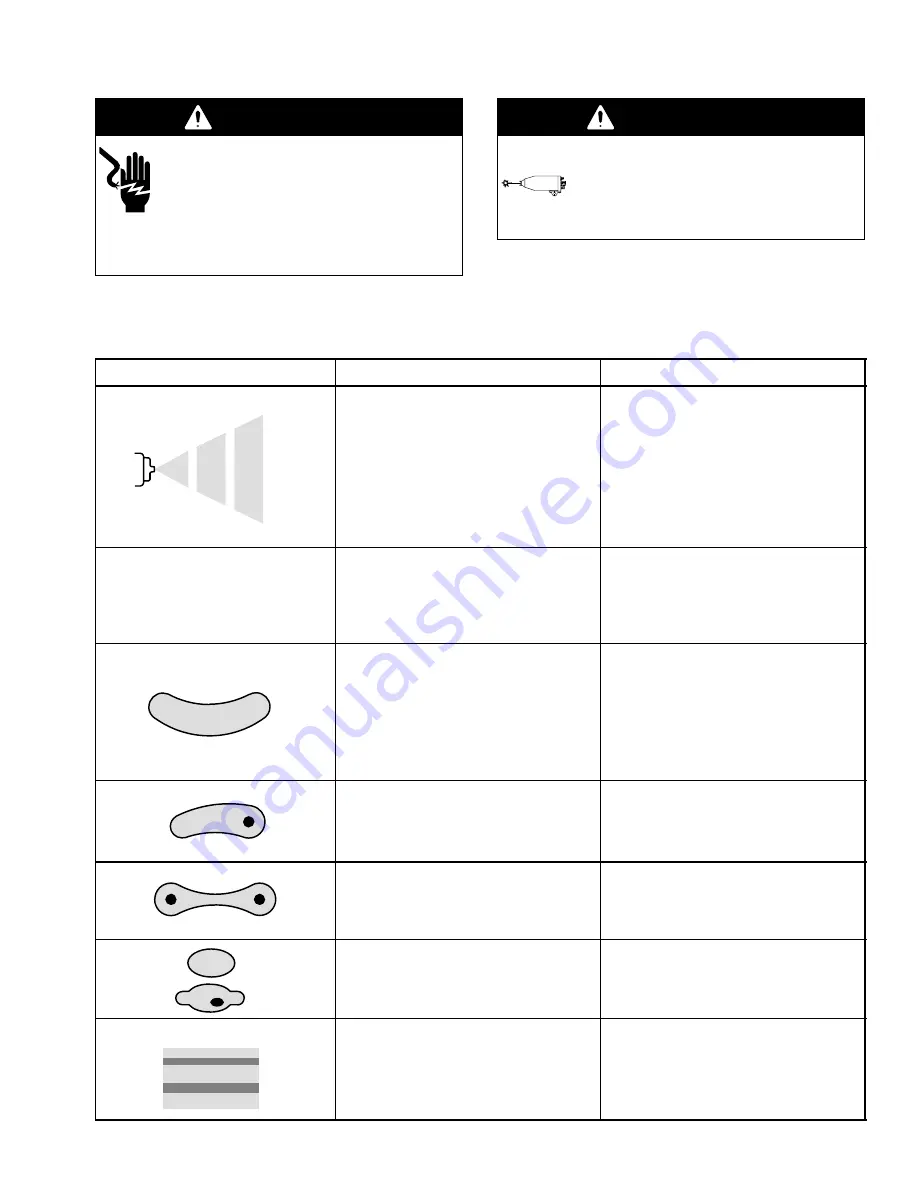
308442 23
Troubleshooting
WARNING
ELECTRIC SHOCK HAZARD
Installing and servicing this equipment
requires access to parts which may
cause an electric shock or other serious
injury if the work is not performed prop-
erly. Do not install or service this equipment unless
you are trained and qualified.
WARNING
PRESSURIZED EQUIPMENT
To reduce the risk of a serious injury,
follow the Pressure Relief Procedure
on page 16 before doing any mainte-
nance or service on the gun or system.
NOTE: Check all possible remedies in the Troubleshooting Charts before disassembling the gun.
Spray Pattern Troubleshooting
NOTE: Some spray pattern problems are caused by the improper balance between air and fluid.
PROBLEM
CAUSE
SOLUTION
Fluttering or spitting spray
The fluid supply is insufficient.
The fluid nozzle is loose, or the fluid noz-
zle taper seat is damaged.
There is dirt between the fluid nozzle,
taper seat, and gun body.
The coupler at the fluid inlet is loose or
cracked.
Adjust the fluid regulator, or fill the fluid
tank.
Tighten or replace the fluid nozzle; see
page 29.
Clean the parts; see page 21.
Tighten or repair the coupler.
Gun is spitting when triggered or
detriggered.
The air cap is damaged or dirty.
The actuator arm is out of position (it is too
close to the fluid needle).
The fluid seat is worn.
Clean or replace the air cap; see page 21.
Reposition the actuator arm; see page 32.
Replace the fluid nozzle and/or electrode
needle; see page 29 and 30.
There is fluid buildup on the air cap; par-
tially clogged horn holes; or full air pres-
sure from the clean horn hole forces the
fan pattern toward the clogged end.
The electrode is bent.
The fluid nozzle or air cap holes are dam-
aged.
Clean the air cap with a soft implement or
submerge it in water and wipe it clean;
see page 21.
Straighten the electrode.
Replace the damaged part; see page 29.
There is fluid buildup on the perimeter of
the fluid nozzle orifice, or a partially
clogged fluid nozzle orifice.
The electrode is bent.
Remove the obstruction; never use wire
or hard instruments; see page 21.
Straighten the electrode.
The fan air pressure is too high.
The fluid is too thin.
There is not enough fluid pressure.
Reduce the fan air pressure.
Increase the fluid viscosity.
Increase the fluid pressure.
The fan air pressure is too low.
The fluid is too thick.
There is too much fluid.
Increase the fan air pressure.
Reduce the fluid viscosity.
Reduce the fluid flow.
Streaks
The last coat of fluid is applied too wet.
There is too much air pressure.
The air pressure is insufficient.
The spray pattern is non-uniform.
Apply a drier finish using multiple strokes.
Decrease the air pressure.
Increase the air pressure.
Clean or replace the air cap; see page 21.