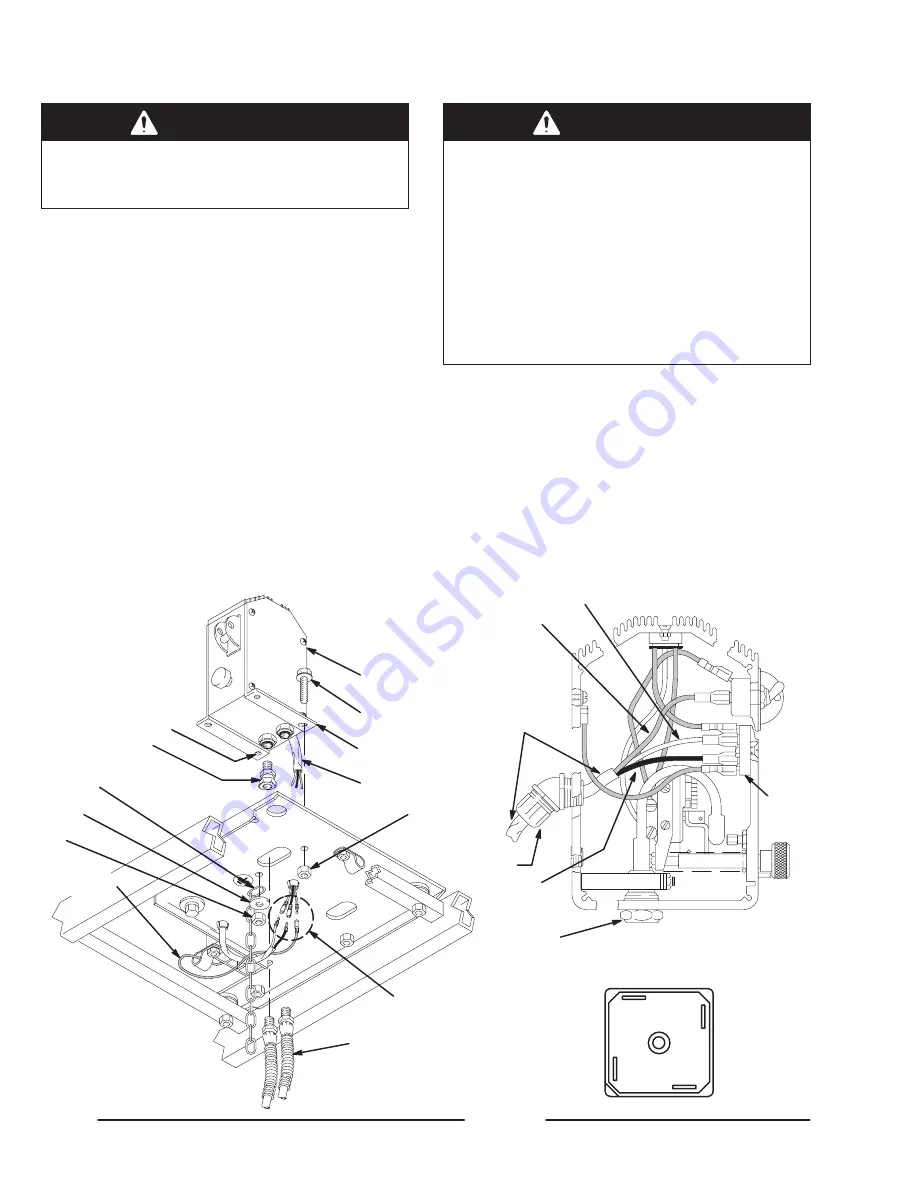
26
308-082
Pressure Control
WARNING
To reduce the risk of serious injury whenever you
are instructed to relieve pressure, always follow the
Pressure Relief Procedure on page 7.
1.
Disconnect both hoses (133) at the pressure control
swivel unions (108). Note the original location of
each hose to be sure you reassemble them correctly
at the end of this procedure. See Fig. 23.
2.
Working under the engine mounting plate of the cart,
disconnect the pressure control wires at A. Remove
the four nuts (40) and related hardware from the
capscrews (91 & 87).
3.
Remove the pressure control covers (89). See Fig.
23.
4.
Disconnect the red, black and white wires from the
rectifier (307) which are sheathed with the conductor
(309). Unscrew the connector (313) from the pres-
sure control, pulling the conductor and wires out with
it. See Fig. 24.
5.
Use a wrench to hold the hex of the adapters (C)
while removing the swivel unions (108). See Fig. 24.
WARNING
To reduce the risk of electric shock, be sure all
grounding features of the pressure control are
properly assembled:
Ground wire (308) connected in pressure con-
trol.
Serrated flange capscrews to mount the pres-
sure control to the cart.
Grounding chain (106) connected by the long
pressure control mounting capscrew (87).
6.
Reassemble the pressure control in the reverse or-
der. Use the long pressure control mounting screw
(87) in hole B. From below the mounting plate (25)
assemble the grounding chain (106), washer (105)
and nut (40) to the screw. See Fig. 23.
7.
Perform the Pressure Control Adjustment on
page 27 before regular operation of the sprayer.
BLACK
RED
WHITE
307
C
RECTIFIER (307) CONNECTIONS
GROUND
BLACK
RED
WHITE
309
313
108
106
105
40
133
40
89
91,87
109
309
B
A
TO FILTER
TO PUMP
TO ENGINE
-
+
~
~
0032
0033
0034
Fig. 23
Fig. 24
Summary of Contents for 231-132
Page 47: ...47 308 082 Notes ...