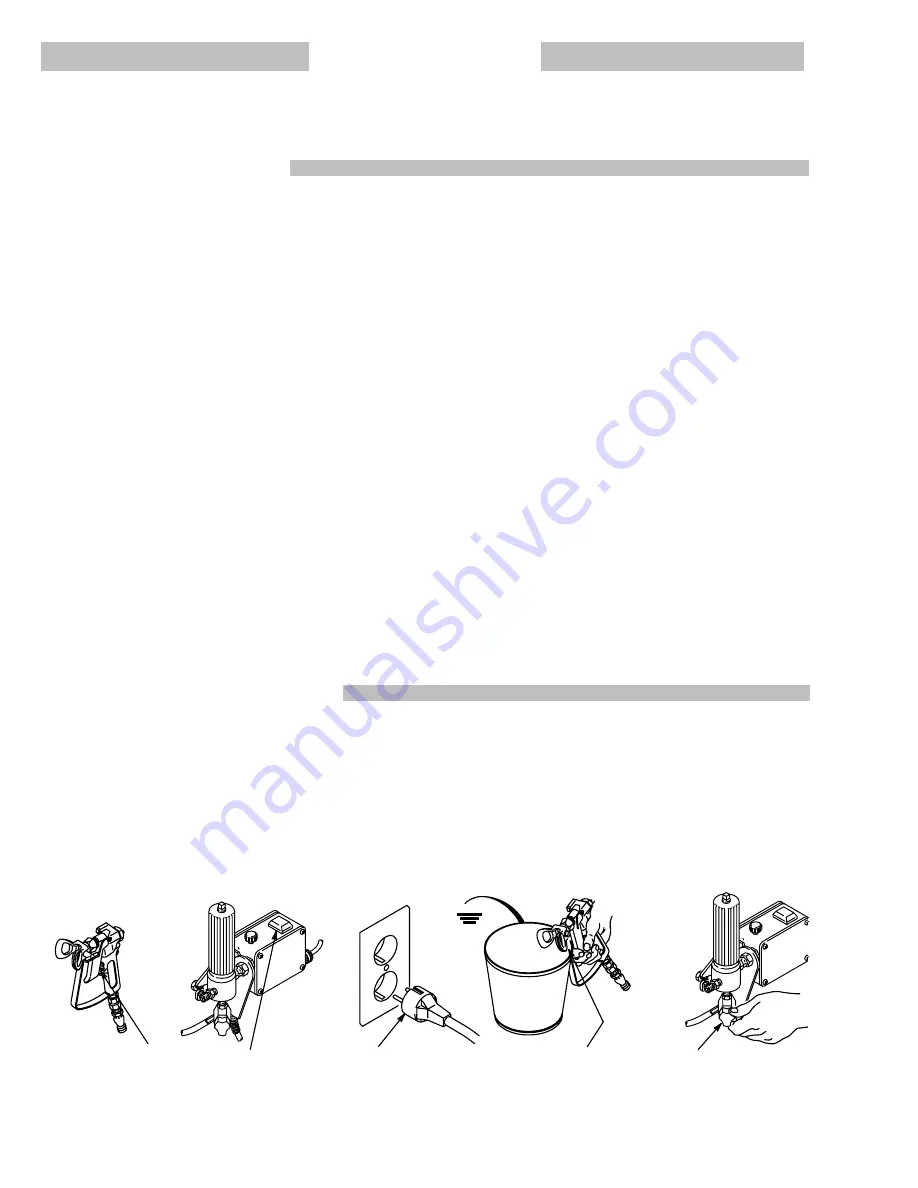
WARNINGS
HIGH PRESSURE SPRAY CAN CAUSE SERIOUS INJURY.
FOR PROFESSIONAL USE ONLY. OBSERVE ALL WARNINGS.
Read and understand all instruction manuals before operating the equipment.
FLUID INJECTION HAZARD
General Safety
This equipment generates very high fluid pressure. Spray from
the gun, leaks or ruptured components can inject fluid through
your skin and into your body, and cause extremely serious bodily
injury, including the need for amputation. Also, fluid injected or
splashed into the eyes or on the skin can cause serious damage.
NEVER point the spray gun at any one or at any part of the body.
NEVER put your hand or fingers over the spray tip. NEVER try
to “blow back” paint; this is NOT an air spray system.
ALWAYS have the tip guard in place on the spray gun when
spraying.
ALWAYS follow the
PRESSURE RELIEF PROCEDURE, below,
before cleaning or removing the spray tip or servicing any sys-
tem equipment.
NEVER try to stop or deflect leaks with your hand or body.
Be sure equipment safety devices are operating properly before
each use.
Medical Alert––Airless Spray Wounds
If any fluid appears to penetrate your skin, get
EMERGENCY
MEDICAL CARE AT ONCE. DO NOT TREA T AS A SIMPLE
CUT. Tell the doctor exactly what fluid was injected.
Note to Physician
: Injection in the skin is a traumatic injury. It
is important to treat the injury surgically as soon as possible.
Do not delay treatment to research toxicity . Toxicity is a
concern with some exotic coatings injected directly into the
blood stream. Consultation with a plastic surgeon or reconstru-
ctive hand surgeon may be advisable.
Spray Gun Safety Devices
Be sure all gun safety devices are operating properly before
each use. Do not remove or modify any part of the gun; this can
cause a malfunction and result in serious bodily injury.
Safety Latch
Whenever you stop spraying, even for a moment, always set the
gun safety latch in the closed or “safe” position, making the gun
inoperative. Failure to set the safety latch can result in accidental
triggering of the gun.
Diffuser
The gun diffuser breaks up spray and reduces the risk of fluid in-
jection when the tip is not installed. Check dif fuser operation
regularly. Follow the
PRESSURE RELIEF PROCEDURE , be-
low, then remove the spray tip. Aim the gun into a metal pail, hold-
ing the gun firmly to the pail. Using the lowest possible pressure,
trigger the gun. If the fluid emitted
is not diffused into an irregular
stream, replace the diffuser immediately.
Tip Guard
ALWAYS have the tip guard in place on the spray gun while
spraying. The tip guard alerts you to the fluid injection hazard
and helps reduce, but does not prevent, the risk of accidentally
placing your fingers or any part of your body close to the spray
tip.
Trigger Guard
Always have the trigger guard in place on the gun when spraying
to reduce the risk of accidentally triggering the gun if it is dropped
or bumped.
Spray Tip Safety
Use extreme caution when cleaning or changing spray tips. If the
spray tip clogs while spraying, engage the gun safety latch im-
mediately. ALWAYS follow the
PRESSURE RELIEF PROCE-
DURE, below, and then remove the spray tip to clean it.
NEVER wipe off build–up around the spray tip until the pressure
is fully relieved and the gun safety is engaged.
PRESSURE RELIEF PROCEDURE
To reduce the risk of serious bodily injury, including fluid injection,
splashing fluid or solvent in the eyes or on the skin, or injury from
moving parts or electric shock, always follow this procedure
whenever you shut off the sprayer, when checking or servicing
any part of the spray system, when installing, cleaning or chang-
ing spray tips, and whenever you stop spraying.
1. Engage the gun safety latch.
2. Turn the ON/OFF switch to OFF.
3. Unplug the power supply cord.
4. Disengage the gun safety latch. Hold a metal part of the gun
firmly to the side of a grounded metal pail, and trigger the gun
to relieve pressure.
5. Engage the gun safety latch.
6. Open the pressure drain valve, having a container ready to
catch the drainage, if a drain tube is not used. Leave the valve
open until you are ready to spray again.
If you suspect that the spray tip or hose is completely clogged,
or that pressure has not been fully relieved after following the
steps above, wrap a rag around the tip guard retaining nut or
hose end coupling and VERY SLOWLY loosen the part to relieve
pressure gradually, then loosen completely. Now clear the tip or
hose.
1,5
2
3
4
6
0112
Summary of Contents for 220-834
Page 18: ...18 NOTES...