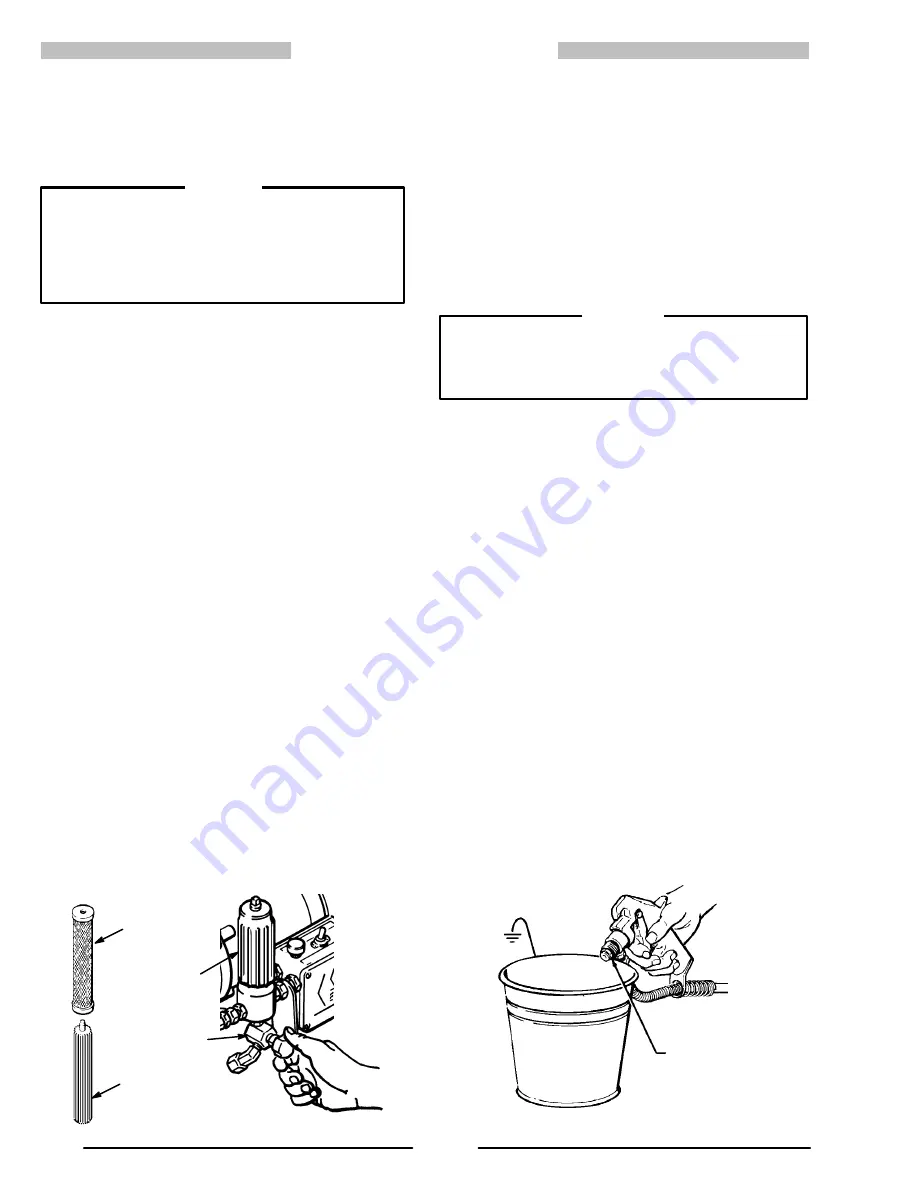
FLUSHING GUIDELINES
NOTE: The Pressure Relief Procedure Warning is on
page 14.
When To Flush
CAUTION
NEVER leave water in the sprayer if there is the
slightest change it could freeze. Flush out the water
with mineral spirits. If water freezes in the pressure
control tube, it prevents the sprayer from being
started, and causes serious damage to the pres-
sure control.
1.
New Sprayer. The sprayer was factory tested in light-
weight oil,which was left in to protect the pump parts.
Before using water-base paint, flush with mineral
spirits, followed by a soapy water flush, and then a
clean water flush.
Before using oil-base paint, flush with mineral spir-
its, only.
2.
Changing Colors. Flush with a compatible solvent
such as mineral spirits or water.
3.
Changing from water-base to oil-base paint.
Flush with warm, soapy water, then mineral spirits.
4.
Changing from oil-base to water-base paint.Flush
with mineral spirits, followed by warm, soapy water,
and then a clean water flush.
5.
Storage.
Water-base paint: Flush with water, and then miner-
al spirits. Leave the pump, hose and gun filled with
mineral spirits. Shut off the sprayer and open the
pressure drain valve to relieve pressure.
Oil-base paint: Flush with mineral spirits. Shut off
and unplug the sprayer, open the pressure drain valve
to relieve pressure.
6.
Startup after storage.
Before using water-base paint, flush out the miner-
al spirits with soapy water, and then with clean water.
When using oil-based paint, flush out the mineral
spirits with the paint to be sprayed.
How To Flush
1.
Relieve pressure.
2.
Remove the filter bowl and screen; see instruction
manual 307–273, supplied. Clean the screen sepa-
rately and install the bowl, without the screen, to flush
the bowl.
See Fig 7.
3.
Close the pressure drain valve.
4.
Pour one–half gallon (2 liters) of compatible solvent
into a grounded metal pail. Put the suction tube in the
pail.
5.
Remove the spray tip from the gun.
WARNING
To reduce the risk of static sparking and splashing
when flushing, always remove the spray tip from
the gun, and hold a metal part of the gun firmly to
the side of, and aimed into, a grounded metal pail
6.
Disengage the gun safety latch. Point the gun into a
metal waste container. With metal part of the gun firmly
touching the metal container, squeeze the gun trigger.
See Fig 8. This procedure reduces the risk of static
sparking and splashing. Start the sprayer, trigger the
gun, and slowly turn the pressure adjusting knob clock-
wise just until the pump starts. Keep the gun triggered
until clean solvent comes from the nozzle. Release the
trigger and engage the gun safety latch.
7.
Check all fluid connections for leaks. If any connec-
tions leak, first relieve pressure. Tighten the connec-
tions. Start the sprayer. Recheck the connections for
leaks.
8.
Remove the suction tube from the pail. Disengage the
gun safety latch. Trigger the gun to force solvent from
the hose. Do not run the pump dry for more than 30
seconds to avoid damaging the pump packings! Re-
lieve pressure.
9.
Leave the pressure drain valve open until you are
ready to use the sprayer again. Unscrew the filter
bowl and reinstall the clean screen. Reinstall the
bowl, hand tight only.
10. If you flushed with mineral spirits and are going to use
a water-base paint, flush with soapy water followed by
a clean water flush. Relieve pressure.
Fig 8
MAINTAIN FIRM
METAL-TO-METAL
CONTACT BETWEEN
GUN AND GROUNDED
METAL CONTAINER
GROUND
WIRE
FILTER
SUPPORT
Fig 7
SCREEN
FILTER
BOWL
PRESSURE
DRAIN VALVE