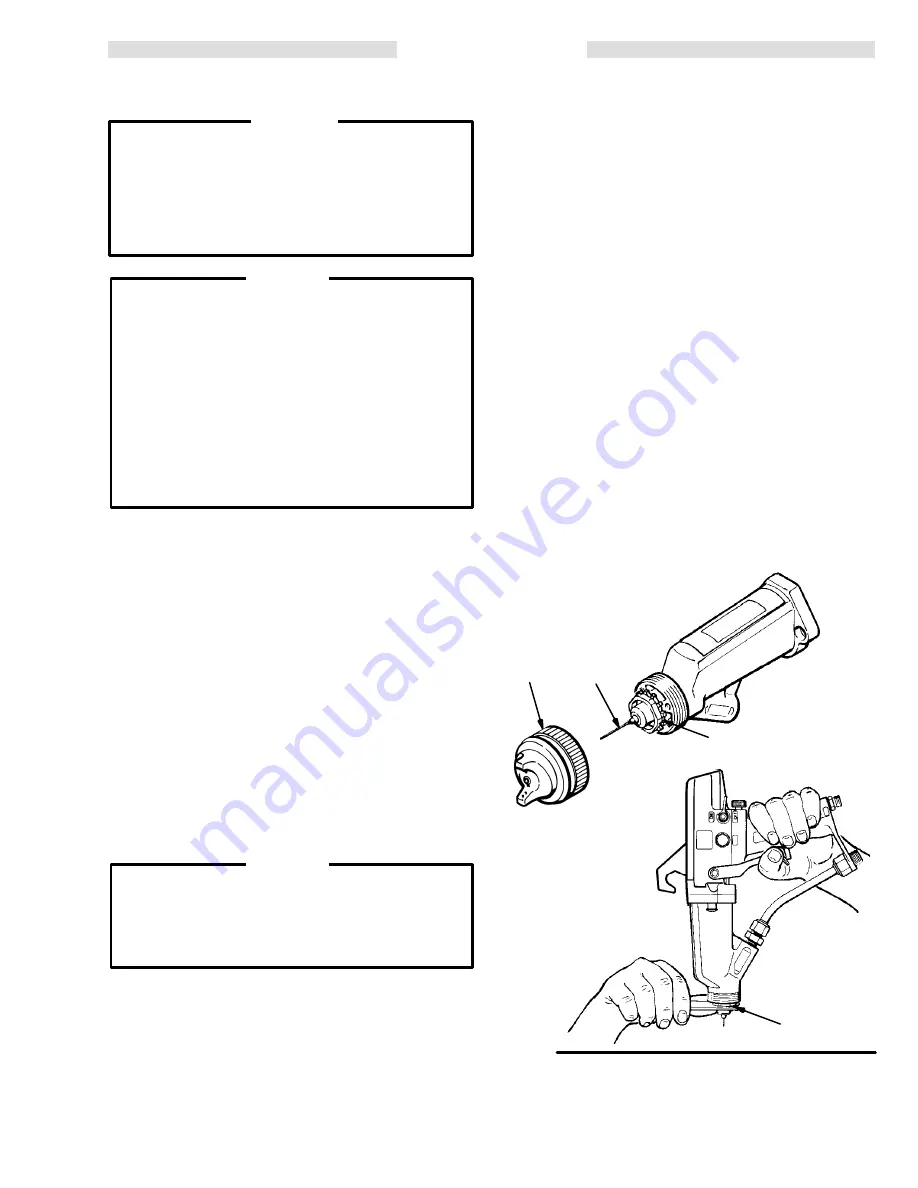
307-638ą11
MAINTENANCE
Daily Care and Cleaning
WARNING
To reduce the risk of serious bodily injury, including
splashing in the eyes or on the skin or electric
shock, always follow the Pressure Relief Proce-
dure Warning on page 9 when shutting off the sys-
tem, when you stop spraying and before checking,
servicing, installing, cleaning or changing any part
in the system.
CAUTION
Clean all parts with a non–conductive solvent,
compatible with the fluid being sprayed.
Conductive solvents can cause the gun to
malfunction.
Do not use any cleaning method which may al-
low solvent into the gun air passages. Solvent
left in the gun passages could result in a poor qual-
ity paint finish and may draw current and reduce
the electrostatic effect. Point the gun down while
cleaning to prevent dirty solvent from running back
into the air passages. NEVER IMMERSE THE
GUN IN SOLVENT.
1.
Clean the fluid and air line filters daily.
2.
Clean the outside of the gun daily with a soft cloth
dampened in a compatible solvent.
3.
Clean the air cap and fluid nozzle daily, minimum.
Some applications require more frequent cleaning.
Replace the fluid nozzle and air cap if they are dam-
aged. See Clean the Air Cap and Fluid Nozzle.
4.
Check the electrode wire. Straighten if bent, and re-
place if broken or damaged. See Electrode Needle
Replacement.
5.
Check all of the work hangers for build-up of material;
clean them, if necessary.
Clean the Air Cap and Fluid Nozzle
CAUTION
Do not use metal tools to clean the air cap holes as
this may scratch them, and make sure the elec-
trode wire is not damaged. Scratches in the air cap
holes or a damaged electrode wire can distort the
spray pattern.
Equipment needed:
Soft bristle brush (supplied).
Fluid nozzle wrench (supplied).
Solvent compatible with fluid being sprayed.
Procedure:
1.
Follow the Pressure Relief Procedure Warning on
page 9.
2.
Remove the air cap assembly (14). See Fig 6.
3.
Turn the locking pin (84) to the unlocked position.
4.
Squeeze the gun trigger and remove the fluid nozzle
with the fluid nozzle wrench (59g) supplied. Make
sure the front of the gun is held down. See Fig 6.
5.
Use the soft bristle brush (59a) supplied and solvent
to clean the air cap, fluid nozzle, and front part of the
gun.
6.
Squeeze the gun trigger and screw the fluid nozzle
back into gun. Tighten the nozzle securely with the
wrench (59g) supplied. Torque the fluid nozzle to
1.1–1.4 N
m (10–12 in–lb). See Fig 6. Turn the lock-
ing pin to the locked position.
7.
Carefully reinstall the air cap assembly. Avoid bend-
ing the electrode (12). Tighten the retaining nut so it
is snug, allowing the air cap to turn with resistance. If
too tight, the spray pattern will be distorted.
Fig 6
KEY
12
Electrode
13
Fluid Nozzle
14
Air Cap Assembly
59g
Wrench
12
13
14
Torque to
1.1–1.4 N
m
(10–12 in–lb)
59g
Summary of Contents for 218-026
Page 2: ......