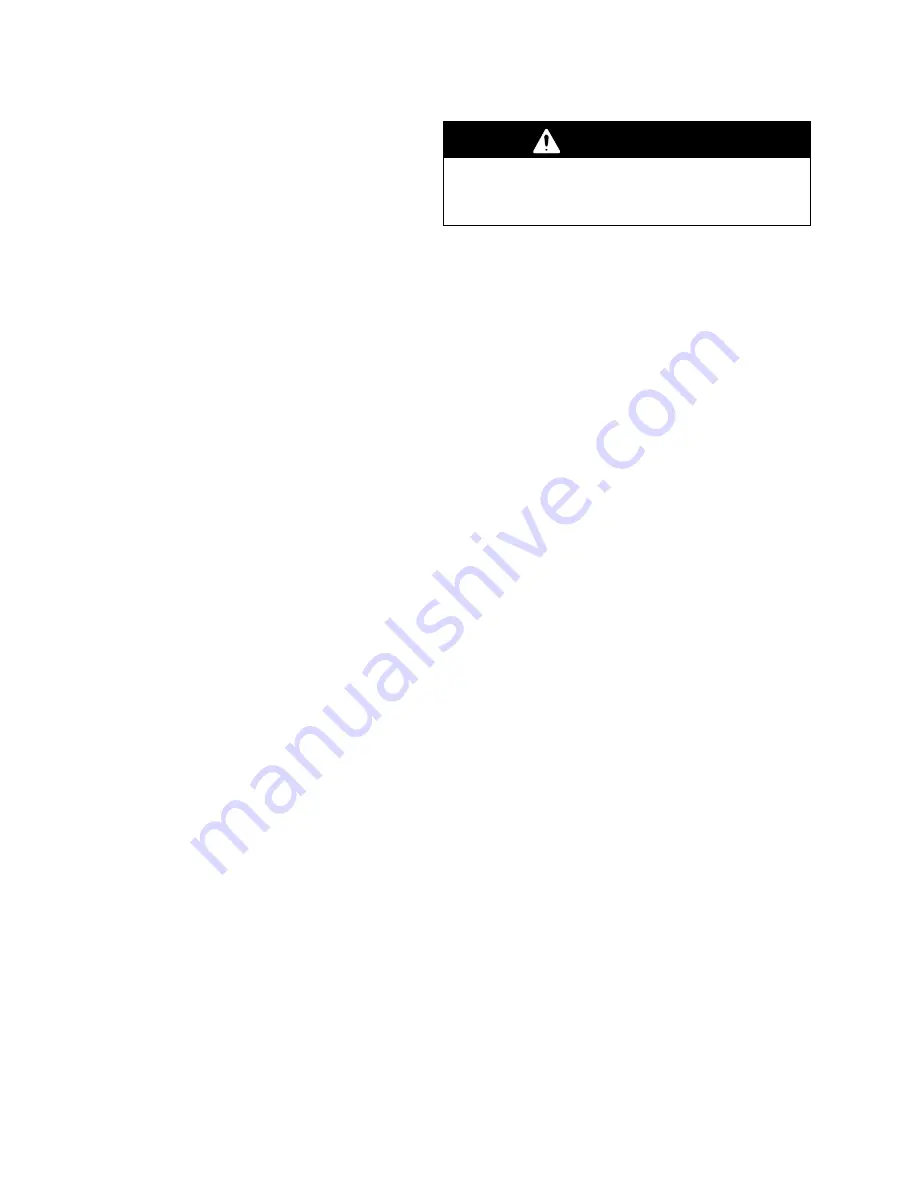
10
306818
Service
Before you start:
D
Have all the necessary repair parts on hand. Rec-
ommended spare parts are shown in the parts list,
for example (32†).
D
A packing repair kit is available for each pump. Use
Kit No. 206931 for rubber packed pumps, and
207349 for
PTFE
R
packed pumps. Use all the new
parts in the kit for the best results. Kit parts are
indicated with an asterisk, for example, (17*).
D
Always replace the glands when replacing the
packings, whether or not you use a repair kit.
D
Use a compatible solvent to clean parts. Inspect
parts for wear or damage and replace parts as
needed. Scoring or irregular surfaces of the dis-
placement rod or polished inner wall of the cylinder
causes premature packing wear and leaking. Check
these parts by rubbing a finger on the surface and
by holding the parts up to the light at a slight angle.
D
Use light, water-proof grease wherever lubrication
is indicated.
Disassembly
WARNING
To reduce the risk of serious injury whenever you
are instructed to relieve pressure, always follow the
Pressure Relief Procedure
on page 6.
1.
Flush the pump, if possible. Then
relieve the
pressure
. Disconnect all air and fluid hoses.
Remove the pump from its mounting and place it
upright in a vise by clamping the intake valve
housing (20).
2.
Remove the tie rod locknuts (29), the cotter pin
(28) and the coupling nut (38). If the riser tube (50)
is installed, remove the outlet adapter (48). Re-
move the intake tube (51, if used). Pull the pump
away from the motor.
3.
Remove the screws (7) from the packing retainer
(4). Remove the packing retainer.
4.
Screw the tie bolts (6) out of the intake housing
(20).
5.
Pull the outlet housing (21) off the cylinder (19).
6.
Remove the bearing (10), female gland (14),
v-packings (24 & 25, or 44), and male gland (13)
from the outlet housing (21).
7.
Remove the displacement rod (3) from the cylinder
(19). Remove the cylinder. Inspect the outer
surface of the displacement rod and the inner
surface of the cylinder for scoring or damage.
8.
Remove the intake valve housing (20) from the
vise. Remove the pin (8), plate (18), and o-ring (23
or 43). Inspect the seat (16) in place.
9.
Place the displacement rod assembly in a vise,
holding it by the flats. Use a 2–1/2 in. hex wrench
to remove the valve seat (15). Remove the bearing
(11), packing (12), plate (17) and o-ring (22 or 42).
If the rod needs replacing, remove one cotter pin
(5) and pull the stop pin (9) out.
10. Clean all parts thoroughly, replace worn or dam-
aged parts. Lubricate all parts before reassem-
bling.
Summary of Contents for 206418
Page 8: ...8 306818 Notes...
Page 13: ...13 306818 Notes...