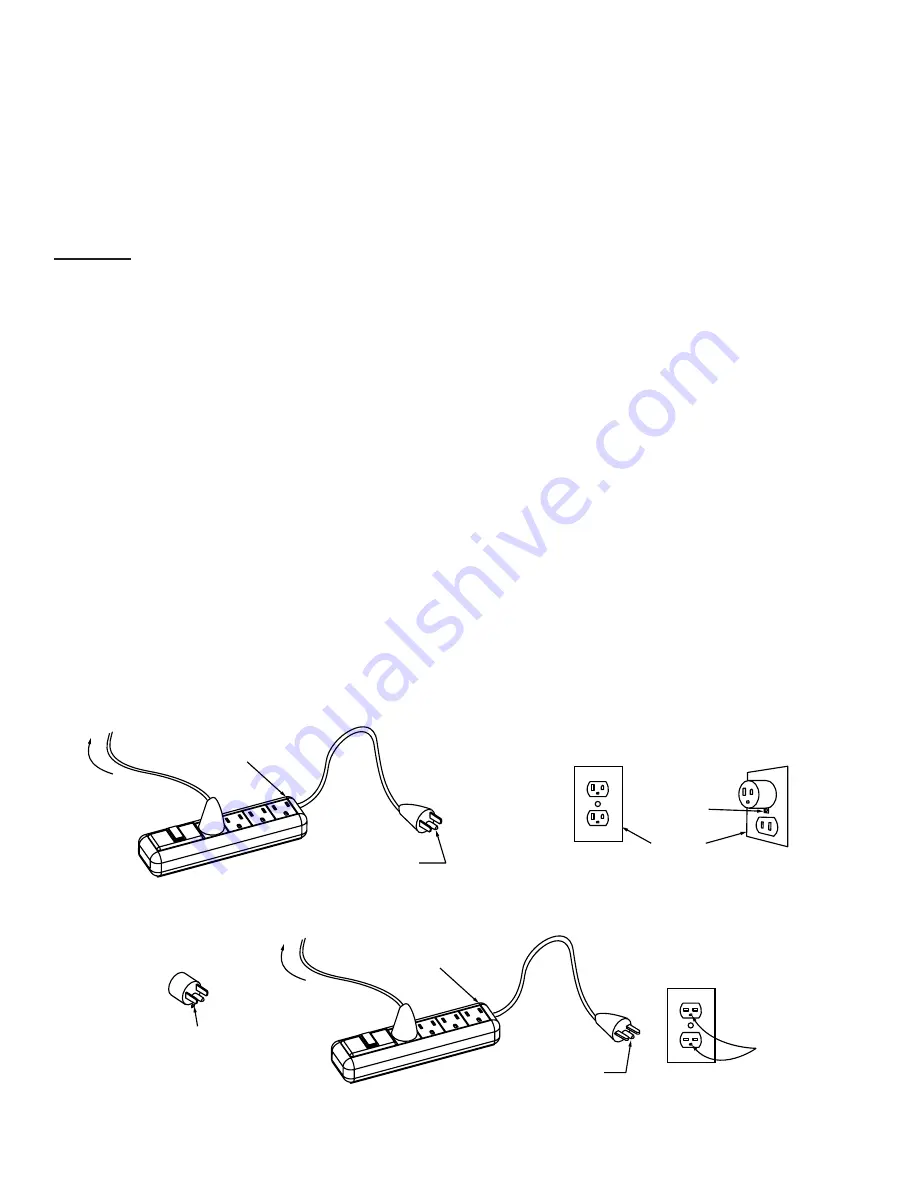
3
Grounding Methods
Figure 61.1
(B)
Cover of
Grounded
Outlet Box
Metal
Screw
(A)
Grounding
Pin
Surge
Protector
To Sewing
Machine
(C)
Adapter
Grounding
Means
(D)
Grounding
Pin
Surge
Protector
To Sewing
Machine
Grounding
Conductor
IMPORTANT SAFETY INSTRUCTIONS
GROUNDING INSTRUCTIONS
This product must be grounded. In the event of malfunction or breakdown, grounding provides a path
of least resistance for electric current to reduce the risk of electric shock. This product is equipped
with a cord that has an equipment-grounding conductor and a grounding plug. Plug the cord from
the Quilting Machine into a surge protector. The surge protector must be plugged into an appropriate
outlet that is properly installed and grounded in accordance with all local codes and ordinances.
DANGER
- Improper connection of the equipment-grounding conductor can result in a risk of electric
shock. The conductor with insulation having an outer surface that is green with or without yellow
stripes is the equipment-grounding conductor. If repair or replacement of the cord or plug is necessary,
do not connect the equipment-grounding conductor to a live terminal. Check with a qualified electrician
or serviceman if the grounding instructions are not completely understood, or if in doubt as to whether
the product is properly grounded.
Do not modify the plug provided with the product - if it will not fit the outlet, have a proper outlet
installed by a qualified electrician.″
This product is for use on a nominal 120 V circuit, and has a grounding plug that looks like the plug
illustrated in sketch A in Figure 61.1. A temporary adapter, which looks like the adapter illustrated in
sketches B and C, may be used to connect this plug to a 2-pole receptacle as shown in sketch B if a
properly grounded outlet is not available. The temporary adapter should be used only until a properly
grounded outlet can be installed by a qualified electrician. The green colored rigid ear, lug, and the like,
extending from the adapter must be connected to a permanent ground such as a properly grounded
outlet box cover. Whenever the adapter is used, it must be held in place by the metal screw.
A qualified electrician should be consulted if there is any doubt as to whether an outlet box is properly
grounded.