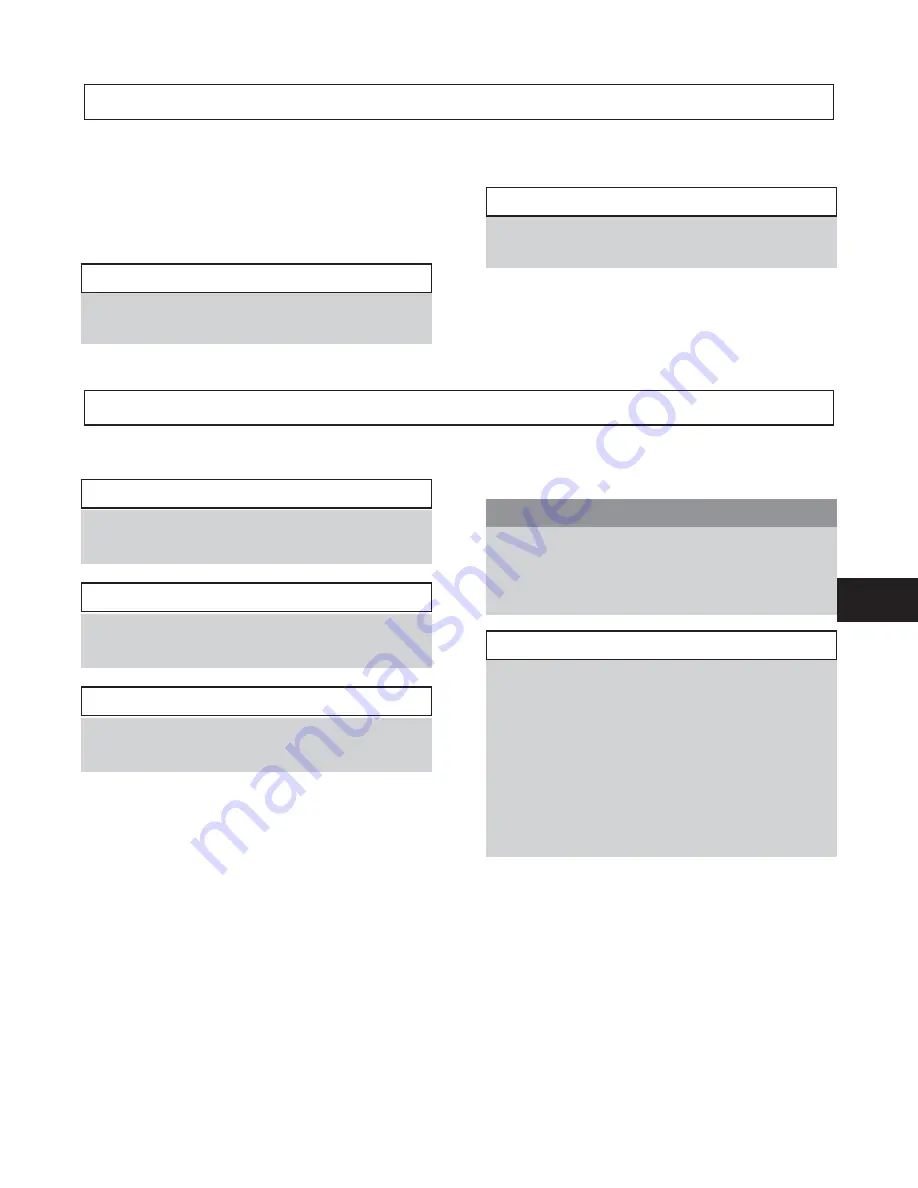
STARTING PUMP
1.
Make sure suction valve and any recirculation or
cooling lines are open.
2.
Fully close or partially open discharge valve as
dictated by system conditions.
3.
Start Driver.
$
!
CAUTION
Immediately observe pressure gauges. If discharge
pressure is not quickly attained - stop driver, reprime
and attempt to restart.
4.
Slowly open discharge valve until the desired flow
is obtained.
$
!
CAUTION
Observe pump for vibration levels, bearing
temperature and excessive noise. If normal levels are
exceeded, shut down and resolve.
OPERATION
GENERAL CONSIDERATIONS
$
!
CAUTION
Always vary capacity with regulating valve in the
discharge line. NEVER throttle flow from the suction
side.
$
!
CAUTION
Driver may overload if the pumpage specific gravity
(density) is greater than originally assumed, or the
rated flow rate is exceeded.
$
!
CAUTION
Always operate the pump at or near the rated
conditions to prevent damage resulting from
cavitation or recirculation.
OPERATING AT REDUCED
CAPACITY
s
!
WARNING
DO NOT operate pump below minimum rated flows
or with suction and/or discharge valve closed. These
conditions may create an explosive hazard due to
vaporization of pumpage and can quickly lead to
pump failure and physical injury.
$
!
CAUTION
Damage occurs from:
1.
Increased vibration levels - Affects bearings,
stuffing box or seal chamber, and mechanical seal.
2.
Increased radial loads - Stresses on shaft and
bearings.
3.
Heat build up - Vaporization causing rotating parts to
score or seize.
4.
Cavitation - Damage to internal surfaces of pump.
OPERATING UNDER FREEZING
CONDITIONS
Exposure to freezing conditions, while pump is idle,
could cause liquid to freeze and damage the pump.
Liquid inside pump should be drained. Liquid inside
cooling coils, if supplied, should also be drained.
3996 IOM 9/2010
25
4
A
A
A
A
A
A
Summary of Contents for 3996
Page 12: ...8 3996 IOM 9 2010 ...
Page 16: ...12 3996 IOM 9 2010 ...
Page 20: ...16 3996 IOM 9 2010 ...
Page 46: ...BEARING OPTIONS SECTIONALVIEW RECOMMENDED SPARE PARTS 42 3996 IOM 9 2010 ...
Page 48: ...44 3996 IOM 9 2010 ...
Page 51: ...3996 IOM 9 2010 47 ...