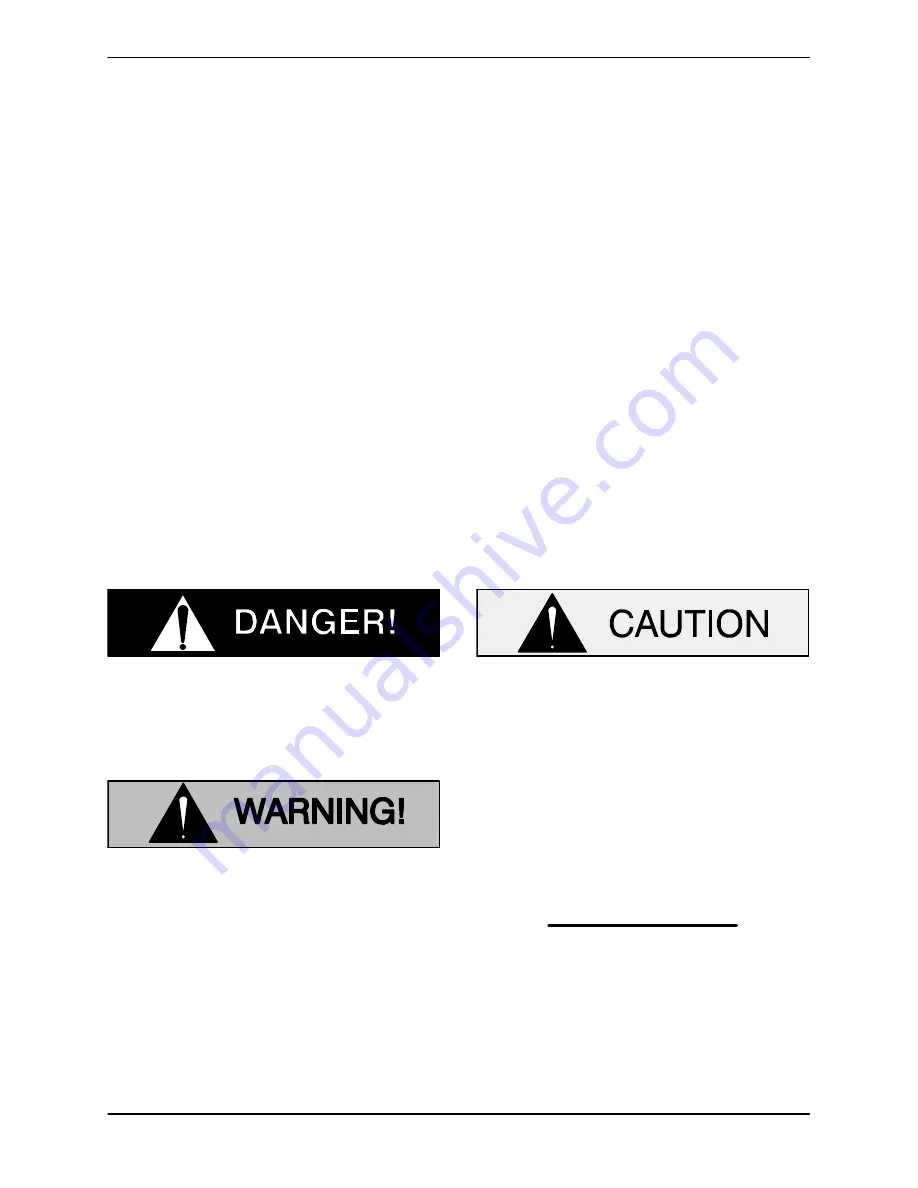
T SERIES
OM--01970
PAGE I -- 1
INTRODUCTION
INTRODUCTION
This Installation, Operation, and Maintenance
manual is designed to help you achieve the best
performance and longest life from your Gorman-
Rupp pump.
This pump is a T Series, semi-open impeller, self-
priming centrifugal model with a suction check
valve. The pump is designed for handling mild in-
dustrial corrosives, residues and slurries contain-
ing large entrained solids. The basic material of
construction for wetted parts is gray iron.
If there are any questions regarding the pump or its application which are not covered in this manual or in
other literature accompanying this unit, please contact your Gorman-Rupp distributor, or write:
The Gorman-Rupp Company
or
Gorman-Rupp of Canada Limited
P.O. Box 1217
70 Burwell Road
Mansfield, Ohio 44901--1217
St. Thomas, Ontario N5P 3R7
For information or technical assistance on the power source, contact the power source manufacturer’s local
dealer or representative.
The following are used to alert maintenance personnel to procedures which require special attention, to
those which could damage equipment, and to those which could be dangerous to personnel:
Immediate hazards which WILL result in
severe personal injury or death. These
instructions describe the procedure re-
quired and the injury which will result
from failure to follow the procedure.
Hazards or unsafe practices which
COULD result in severe personal injury
or death. These instructions describe
the procedure required and the injury
which could result from failure to follow
the procedure.
Hazards or unsafe practices which COULD
result in minor personal injury or product
or property damage. These instructions
describe the requirements and the possi-
ble damage which could result from failure
to follow the procedure.
NOTE
Instructions to aid in installation, operation, and
maintenance or which clarify a procedure
.