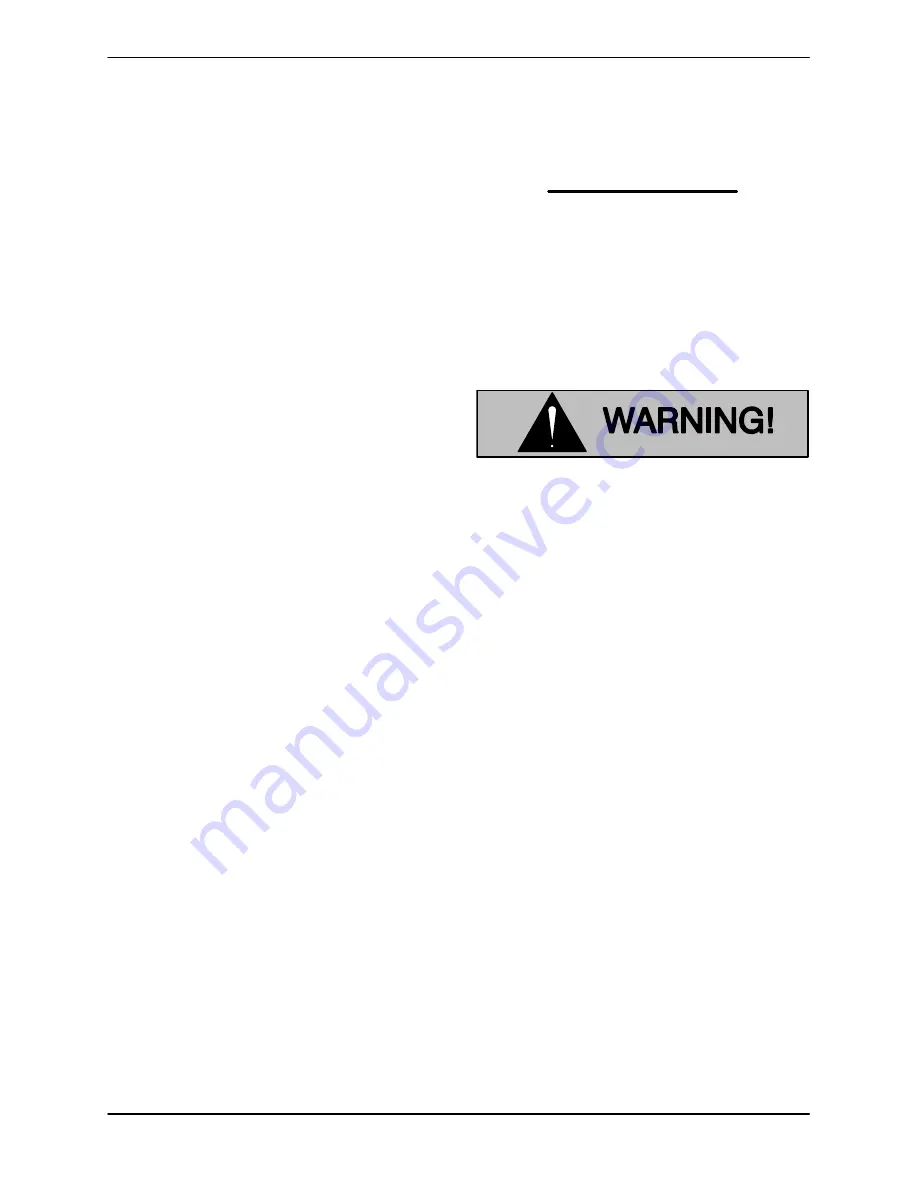
OM−05463
10 SERIES
MAINTENANCE & REPAIR
PAGE E − 7
Pump Casing Removal
(Figure 2)
To service the impeller or seal assembly, discon-
nect the discharge piping. See Figure 1 and re-
move the hardware (12, 13 and 14) securing the
pump casing to the base (3).
Support the pump casing (1) using a suitable hoist
and sling, and remove the hardware (17 and 18)
securing the pump casing to the intermediate (15).
Separate the parts by pulling the casing straight
away from the intermediate. If shims have been
used under the mounting feet to level the pump
casing, tie and tag these shims for ease of reas-
sembly.
Remove the casing o-ring (21). Clean the mating
surfaces of the intermediate and pump casing.
Impeller Removal
(Figure 2)
To loosen the impeller (2), tap the vanes of the im-
peller in a counterclockwise direction (when facing
the impeller) with a block of wood or a soft-faced
mallet. Unscrew the impeller and replace it if
cracked or badly worn. Use caution when remov-
ing the impeller; tension on the seal spring will be
released as the impeller is unscrewed.
Slide the impeller adjusting shims (4) off the impel-
ler shaft. Tie and tag the shims or measure and re-
cord their thickness for ease of reassembly.
Seal Removal and Disassembly
(Figures 2 and 3)
Remove the spring centering washer (5) and seal
spring. Slide the shaft sleeve (6) and rotating por-
tion of the seal off the shaft as an assembly. Lubri-
cate the sleeve adjacent to the seal and work oil up
under the rubber bellows. Slide the rotating portion
of the seal off the shaft sleeve.
Remove the hardware (17 and 18) and carefully
slide the intermediate (15) and stationary portion of
the seal off the shaft as a unit. Use a suitably sized
dowel to press the stationary element out of the in-
termediate from the back side.
NOTE
The seal assembly may be removed without com-
pletely disassembling the pump by using a pair of
stiff wires with hooked ends to pull the seal station-
ary seat out of the intermediate.
If no further disassembly is required, see
Seal
Reassembly and Installation
.
Seal Reassembly and Installation
(Figures 2 and 3)
Clean the seal cavity and shaft with a cloth soaked
in fresh cleaning solvent.
Most cleaning solvents are toxic and
flammable. Use them only in a well ven-
tilated area free from excessive heat,
sparks, and flame. Read and follow all
precautions printed on solvent contain-
ers.
The seal is not normally reused because wear pat-
terns on the finished faces cannot be realigned
during reassembly. This could result in premature
failure. If necessary to reuse an old seal in an emer-
gency,
carefully
wash all metallic parts in
fresh
cleaning solvent and allow to dry thoroughly.
Handle the seal parts with extreme care to prevent
damage. Be careful not to contaminate precision
finished faces; even fingerprints on the faces can
shorten seal life. If necessary, clean the faces with a
non-oil based solvent and a clean, lint-free tissue.
Wipe
lightly
in a concentric pattern to avoid
scratching the faces.
Inspect the seal components for wear, scoring,
grooves, and other damage that might cause leak-
age. Clean and polish the shaft sleeve, or replace it
if there are nicks or cuts on either end. If any com-
ponents are worn, replace the complete seal;
never mix old and new seal parts
.
If a replacement seal is being used, remove it from
the container and inspect the precision finished
faces to ensure that they are free of any foreign
matter.