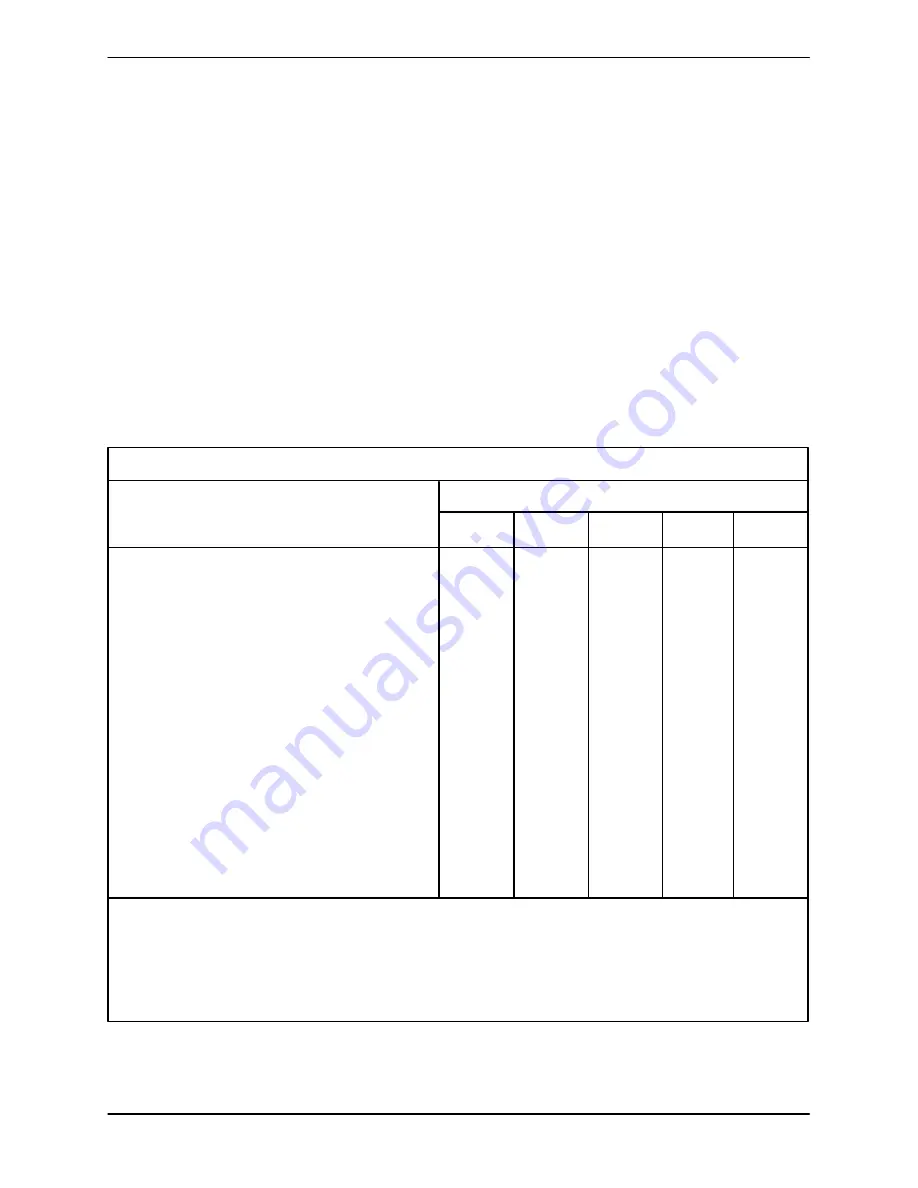
OM−05463
10 SERIES
TROUBLESHOOTING
PAGE D − 3
PREVENTIVE MAINTENANCE
Since pump applications are seldom identical, and
pump wear is directly affected by such things as
the abrasive qualities, pressure and temperature
of the liquid being pumped, this section is intended
only to provide general recommendations and
practices for preventive maintenance. Regardless
of the application however, following a routine pre-
ventive maintenance schedule will help assure
trouble-free performance and long life from your
Gorman-Rupp pump. For specific questions con-
cerning your application, contact your Gorman-
Rupp distributor or the Gorman-Rupp Company.
Record keeping is an essential component of a
good preventive maintenance program. Changes
in suction and discharge gauge readings (if so
equipped) between regularly scheduled inspec-
tions can indicate problems that can be corrected
before system damage or catastrophic failure oc-
curs. The appearance of wearing parts should also
be documented at each inspection for comparison
as well. Also, if records indicate that a certain part
(such as the seal) fails at approximately the same
duty cycle, the part can be checked and replaced
before failure occurs, reducing unscheduled down
time.
For new applications, a first inspection of wearing
parts at 250 hours will give insight into the wear rate
for your particular application. Subsequent inspec-
tions should be performed at the intervals shown
on the chart below. Critical applications should be
inspected more frequently.
General Condition (Temperature, Unusual
Noises or Vibrations, Cracks, Leaks,
Loose Hardware, Etc.)
I
Pump Performance (Gauges, Speed, Flow)
I
Bearing Lubrication
I
R
Seal Lubrication (And Packing Adjustment,
If So Equipped)
I
R
V-Belts (If So Equipped)
I
Air Release Valve Plunger Rod (If So Equipped)
I
C
Front Impeller Clearance (Wear Plate)
I
Rear Impeller Clearance (Seal Plate)
I
Check Valve
I
Pressure Relief Valve (If So Equipped)
C
Pump and Driver Alignment
I
Shaft Deflection
I
Bearings
I
Bearing Housing
I
Piping
I
Driver Lubrication − See Mfgr’s Literature
Legend:
I = Inspect, Clean, Adjust, Repair or Replace as Necessary
C = Clean
R = Replace
* Service interval based on an intermittent duty cycle equal to approximately 4000 hours annually.
Adjust schedule as required for lower or higher duty cycles or extreme operating conditions.
Preventive Maintenance Schedule
Item
Daily
Weekly
Monthly
Semi-
Annually
Annually
Service Interval*