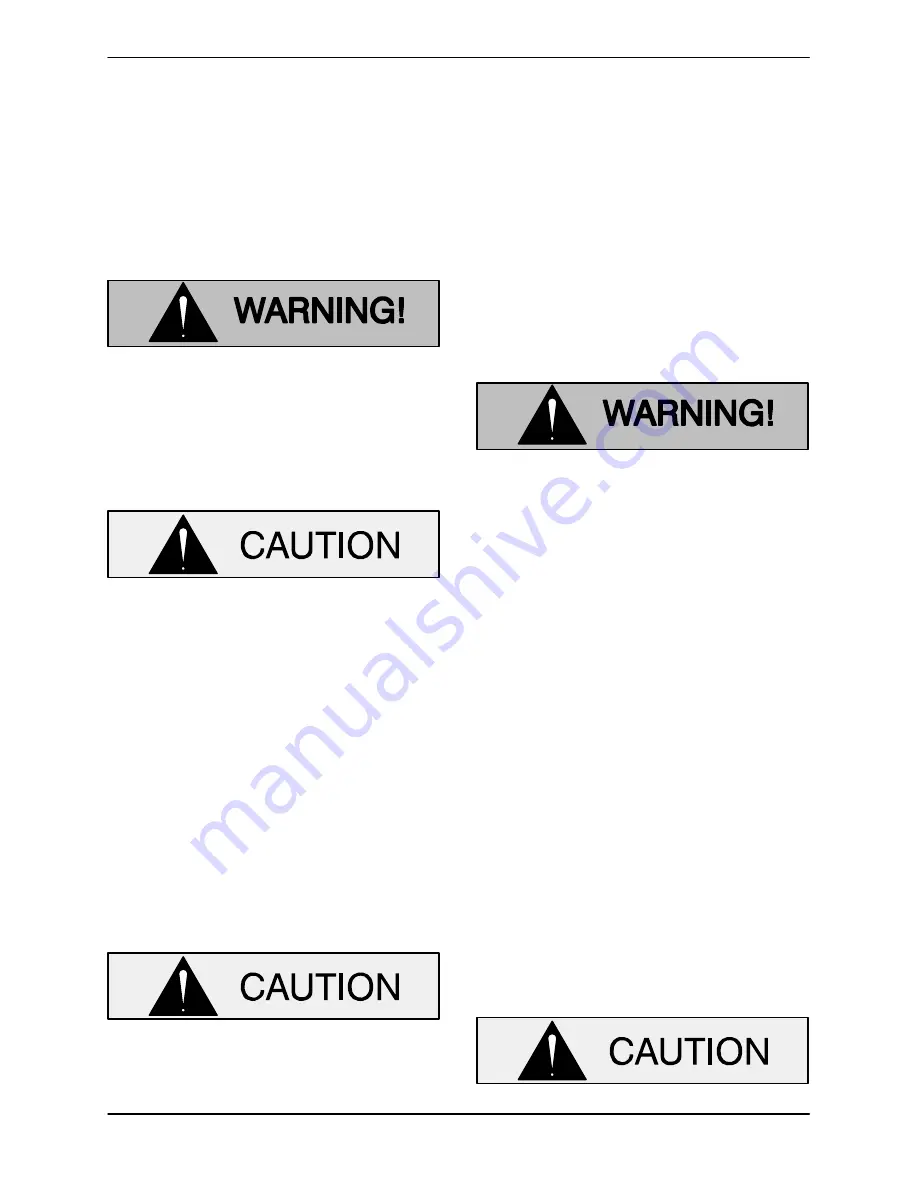
SUPER T SERIES
OM-05350
OPERATION
PAGE C - 1
OPERATION - SECTION C
Review all SAFETY information in Section A.
Follow the instructions on all tags, labels and de
cals attached to the pump.
This pump is designed to handle liquids
containing large entrained solids and
slurries. Do not attempt to pump vola
tile, corrosive, or flammable liquids
which may damage the pump or endan
ger personnel as a result of pump fail
ure.
Pump speed and operating conditions
must be within the performance range
shown on page E‐1.
PRIMING
Install the pump and piping as described in
IN
STALLATION
. Make sure that the piping connec
tions are tight, and that the pump is securely
mounted. Check that the pump is properly lubri
cated (see
LUBRICATION
in
MAINTENANCE
AND REPAIR
).
This pump is self‐priming, but the pump should
never be operated unless there is liquid in the
pump casing.
Never operate this pump unless there is
liquid in the pump casing. The pump will
not prime when dry. extended operation of
a dry pump will destroy the seal assembly.
Add liquid to the pump casing when:
1. The pump is being put into service for the
first time.
2. The pump has not been used for a consider
able length of time.
3. The liquid in the pump casing has evapo
rated.
Once the pump casing has been filled, the pump
will prime and reprime as necessary.
After filling the pump casing, reinstall
and tighten the fill plug. Do not attempt
to operate the pump unless all connect
ing piping is securely installed. Other
wise, liquid in the pump forced out
under pressure could cause injury to
personnel.
To fill the pump, remove the pump casing fill cover
or fill plug in the top of the casing, and add clean
liquid until the casing is filled. Replace the fill cover
or fill plug before operating the pump.
STARTING
Consult the operations manual furnished with the
power source.
Rotation
The correct direction of pump rotation is counter
clockwise when facing the impeller. The pump
could be damaged and performance adversely af
fected by incorrect rotation. If pump performance
is not within the specified limits (see the curve on
page E‐1), check the direction of power source ro
tation before further troubleshooting.
Only operate this pump in the direction in