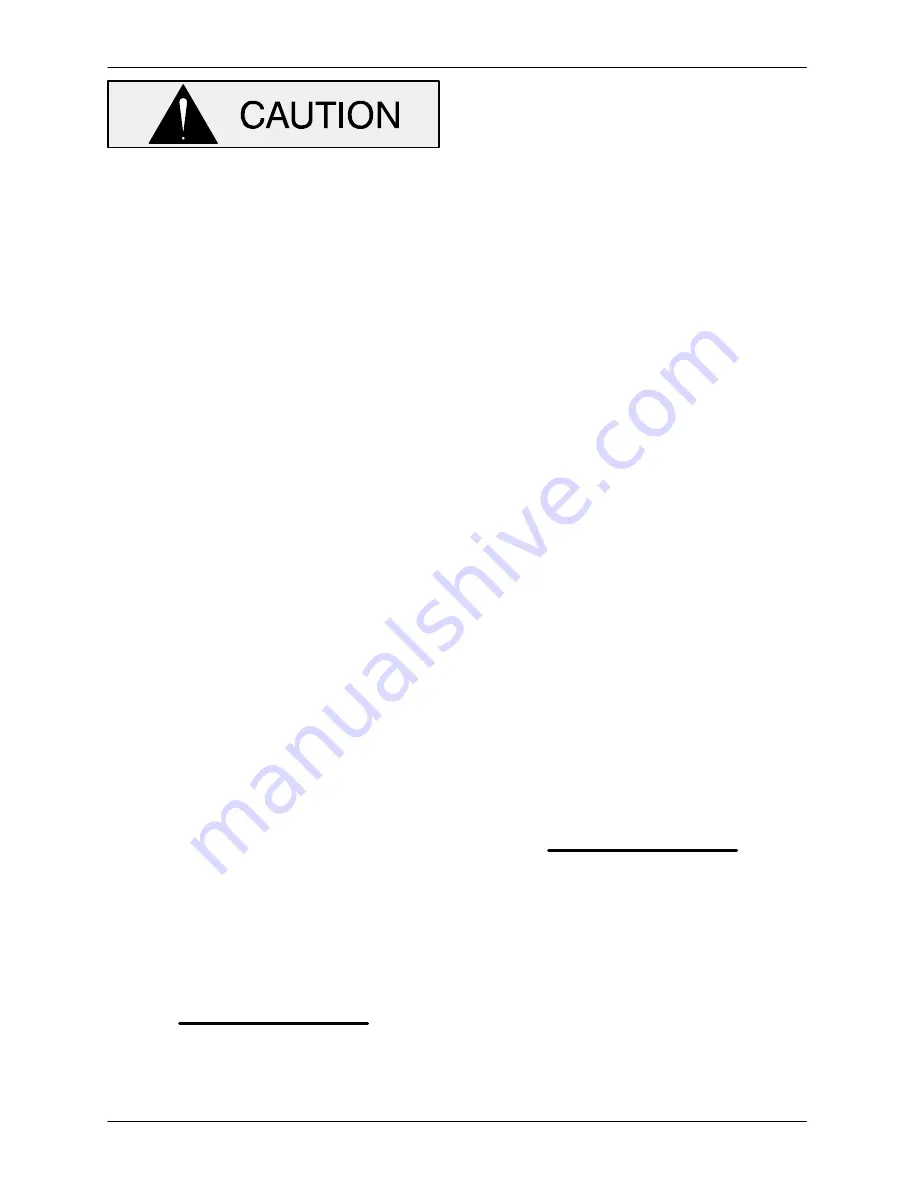
S SERIES PUMPS
OM-07264
MAINTENANCE AND REPAIR
PAGE E - 10
This seal is not designed for operation at
temperatures above 122
_
F (50
_
C). Do not
use at higher operating temperatures.
Seal Installation
(Figures 1 and 3)
Do not
unwrap a new seal assembly until time of
installation. Cleanliness of seal components is criti
cal, especially the seal faces.
Clean the rotor shaft (33) and seal cavity area of the
intermediate (8). Be sure the area is dry and free of
lint and dirt. Check the seal bore for burrs or nicks
that might prevent a good seal. Remove them with
a fine file or emery cloth to restore original con
tours. If the shaft is bent or damaged, the complete
rotor and shaft must be replaced as an assembly.
Apply a
light
coating of oil to the bore of the inter
mediate.
Carefully remove the material stuffed into the seat
bore (or unwrap the shaft).
Be sure
no debris
stopped by the material falls into the seal cavity.
Clean and inspect the shaft sleeve (40). Replace it
if badly scored, or if cut or nicked on the ends. Ap
ply a light coating of oil to the shaft sleeve.
Apply a light coating of oil to the O‐ring (16) and
install it on the rotor shaft.
Unpack the upper stationary element. Apply a light
coating of oil to the O‐ring O.D.. Keep the sealing
face dry.
NOTE
When pressing seal components onto the impeller
shaft, use hand pressure only. A push tube cut from
a length of plastic pipe will aid in installing seal
components. The I.D. of the push tube should be
approximately the same as the I.D. of the seal
spring.
Unpack the upper rotating portion of the seal. Be
certain the seal face of the rotating element is free
of grit or surface damage. Because the rotating
element may not stay in the bellows retainer when
turned upside down, place a
small
amount of
grease at equal spaces on the back of the element
and position it in the bellows retainer. The grease
should hold the element in position until the seal is
installed. Assemble the drive grooves of the rotat
ing element into the drive lugs of the bellows retain
er.
Slide the upper seal rotating portion onto the lubri
cated shaft sleeve with the seal face toward the
stepped end. Apply firm, steady pressure on the
seal retainer until it slides down the sleeve. Inspect
the seal face to ensure that it is clean and dry. If
cleaning is necessary, use a clean tissue to wipe in
a concentric pattern.
Install the seal spring.
Unpack the lower seal rotating element and follow
the same inspection procedure as for the upper ro
tating element. Place a clean tissue over the seal
face, and press the rotating element onto the shaft
sleeve with seal face away from the stepped end.
Remove the tissue and inspect the seal face to en
sure that it is clean and dry. If cleaning is neces
sary, use clean tissue to wipe in a concentric pat
tern.
Slide the sleeve and assembled rotating seal as
semblies onto the rotor shaft until the upper seal
faces contact. Continue to push the sleeve through
the seal until the stepped end of the sleeve fits over
the shaft shoulder.
NOTE
The seal spring will not fully compress until the dif
fuser (1) is installed.
Inspect the diffuser (1) for cracks, distortion, and
erosion. Replace it if defective.
Unpack the stationary portion of the lower seal as
sembly. Be certain the seal face is free of grit or sur
face damage. Protect the seal face with a clean tis
sue.
Lubricate the lower seal seat O‐ring O.D. and posi
tion the seat assembly in the diffuser bore. Apply
firm steady pressure until the stepped portion of
the seat rests firmly against the diffuser. Make sure