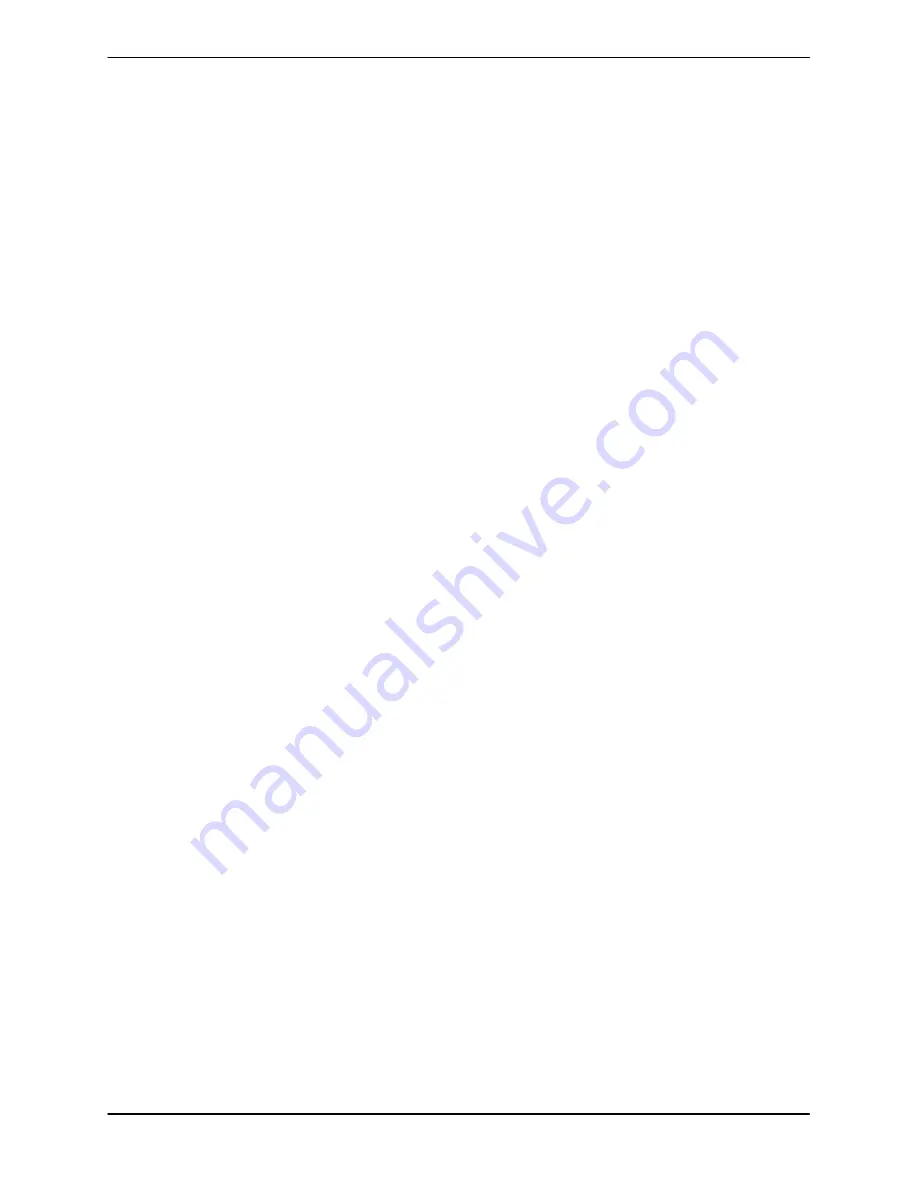
OM-07297
DIAPHRAGM PRIMER
MAINTENANCE & REPAIR
PAGE E - 9
in the grooves of the crankshaft (37). Turn the
crankshaft on the drive end to operate the di
aphragm primer. It should move smoothly by hand
and not bind up.
It is recommended that the oil seal be replaced and
not reused. The new oil seal (28) will need to be
pressed into the drive end bearing cover (29). After
removing the used oil seal, place the bearing cover
(29) onto a press. Insert the oil seal (28) over its
pocket. Place a piece of round metal that is be
tween the diameter of the oil seal and the opening
on the cover and press the two pieces together.
Apply a thin layer of grease or oil on the lip of the
drive end bearing cover (29). Roll O‐ring (20) over
the lip of the bearing cover (29) using caution not to
damage or rip the material. Place the bearing cover
(29) over the crankshaft (27). Use caution not to
dislodge the oil seal (28), or damage it on the
crankshaft key way edges, while sliding the cover
onto the crankshaft (27) and into the bearing hous
ing (1). Secure with the cap screws and lock wash
ers (16 and 17). Torque hardware to 9 ft-lbs (12.20
N-m).
Install the inspection cover (34) and inspection
cover gasket (35). Use the cap screws (16) and
lock washers (17) to hold them in place. With the
gasket (35) between the inspection cover (34) and
the bearing housing (1), finger tighten the cap
screws all the way around the cover. Torque hard
ware to 9 ft-lbs (12.20 N-m).
Lubricate the I.D. and O.D. of the neck seal as
needed (3) using P80 lubricant or water and slide it
over the connecting rod assembly (2) shaft. Care
fully press the component by hand into the bearing
housing until fully seated. The top of the neck seal
(3) outer lip should be flush with, or below, the top
face of the bearing housing (1) when seated.
Pre-assemble the lower housing (4) with the valve
(32) and discharge port (8). Insert the retaining pin
(30) through the washer (31). Insert the retaining
pin (30) through a valve (32) and another washer
(31). The high side of the valve should be towards
the shoulder on the retaining pin (30).
With the bottom of the lower housing (4) facing up
and the machined surface laying flat on a work ta
ble, install the retaining pin (30) holding the valve
(32) into the center hole of the valve opening. While
holding the valve in place, flip over the lower hous
ing. Install the retaining ring (33) into the groove on
the retaining pin (30) with pliers.
Flip the lower housing (4) back over and lay it flat
with the valve opening on the opposite side of the
table. Line up the discharge port gasket (7) with the
four tapped holes around the installed valve. Line
up the discharge port (8) with the four holes of the
gasket (7). Orient the discharge port (8) with the
opening turned 90° to the right hand side from the
center hole in the lower housing (4) (facing the GR
logo). Install cap screws (16) and lock washers
(17). Torque all four to 9 ft-lbs (12.20 N-m).
Clean mating surfaces of the bearing housing (1)
and the lower housing (4). Apply Loctite® 515 gas
ket maker to the top machined surface of the bear
ing housing (1). Install two long studs into the
tapped holes at opposite corners of the bearing
housing (1) top surface. Hand tighten only. Use
these studs to line up the pre-assembled lower
housing (4) with the bearing housing (1). With the
lower housing positioned over the studs, install two
of the cap screws (43) and two flat washers (44) in
to the two remaining holes in the bearing housing
(1). Remove the two studs. Insert the two remain
ing cap screws (43) and lock washers (44). Torque
all four to 38 ft-lbs (51.52 N-m).
Install the new valves (32) for the diaphragm as
sembly (6) as follows. Lay the diaphragm assem
bly (6) flat with the recessed valve pockets facing
up. Insert the retaining pin (30) through the washer
(31). Insert the retaining pin (30) through a valve
(32) and another washer (31). The high side of the
valve should be towards the shoulder on the retain
ing pin (30). install the retaining pin (30) holding the
valve (32) into a center hole of a valve opening.
While holding the valve in place, flip over the di
aphragm assembly (6). Install the retaining ring
(33) into the groove on the retaining pin (30) with
pliers. Repeat this process to install the second
valve.
Turn the crankshaft until the connecting rod as
sembly (2) is at the highest point in its travel. With
the valves facing down towards the lower housing
(4) align the center post of the diaphragm assem
bly (6) with the top of the of the connecting rod as
sembly (2) in the center of the lower housing (4). If
installed correctly, the diaphragm edge should
seat down in the lower housing (4) edge lip at the