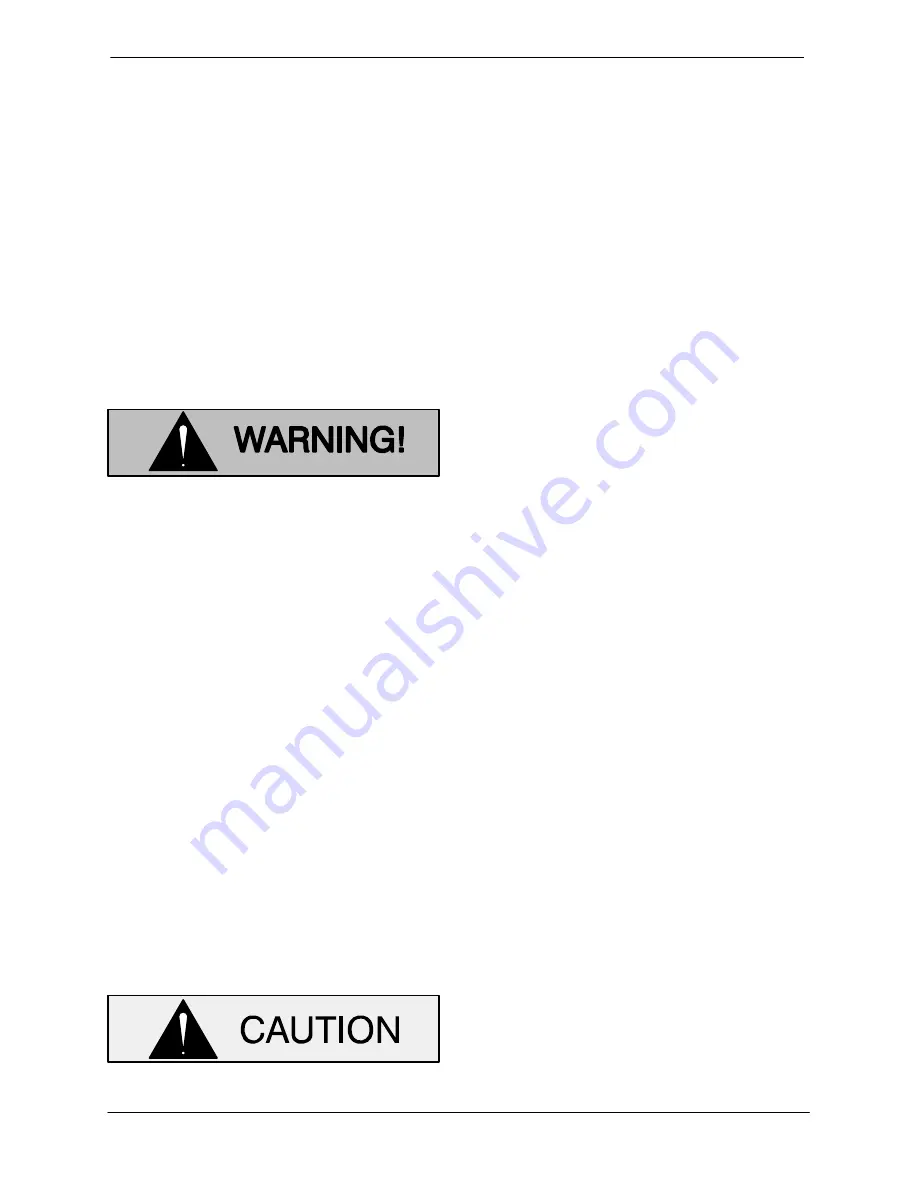
OM-01490
D SERIES
PAGE B - 2
INSTALLATION
If the maximum shelf life has been exceeded, or if
anything appears to be abnormal, contact your
Gorman‐Rupp distributor or the factory to deter
mine the repair or updating policy.
Do not
put the
pump into service until appropriate action has
been taken.
ELECTRIC MOTOR INSTALLATION
The pump is designed to be flex‐coupled to a 1750
RPM synchronous speed electric motor. The pump
base will accept either a 143T or 145T motor frame.
Be sure the motor to be used meets these specifi
cations and is compatible with the intended appli
cation.
Install and operate only an explosion
proof motor in an explosive atmo
sphere. Install, connect, and operate
the motor in accordance with the Na
tional Electric Code and all local codes.
If there is a conflict between the instruc
tions in the manual accompanying the
unit and the National Electric Code or
the applicable local code, the National
or local code shall take precedence.
POSITIONING PUMP
Lifting
Pump unit weights will vary depending on the
mounting and drive provided. Check the shipping
tag on the unit packaging for the actual weight, and
use lifting equipment with appropriate capacity.
Drain the pump and remove all customer‐installed
equipment such as suction and discharge hoses
or piping before attempting to lift existing, installed
units.
The pump assembly can be seriously
damaged if the cables or chains used to lift
and move the unit are improperly wrapped
around the pump.
Mounting
Locate the pump in an accessible place as close as
practical to the liquid being pumped. Level mount
ing is essential for proper operation.
The pump may have to be supported or shimmed
to provide for level operation or to eliminate vibra
tion.
After the pump has been positioned, block the
wheels and secure the pump to prevent creeping.
SUCTION AND DISCHARGE PIPING
Pump performance is adversely effected by in
creased suction lift, discharge elevation, and fric
tion losses. See Page E‐1 to be sure your overall
application allows the pump to operate within the
safe operation range.
Materials
Either pipe or hose maybe used for suction and
discharge lines; however, the materials must be
compatible with the liquid being pumped. If hose is
used in suction lines, it must be the rigid‐wall, rein
forced type to prevent collapse under suction. Us
ing piping couplings in suction lines is not recom
mended.
Line Configuration
Keep suction and discharge lines as straight as
possible to minimize friction losses. Make mini
mum use of elbows and fittings, which substan
tially increase friction loss. If elbows are necessary,
use the long‐radius type to minimize friction loss.
Never pull a line into place by tightening connec
tions at the pump. Lines near the pump must be in
dependently supported to avoid strain on the
pump which could cause excessive vibration and
increased diaphragm and gear train wear. If hose‐
type lines are used, they should have adequate
support to secure them when filled with liquid and
under pressure.