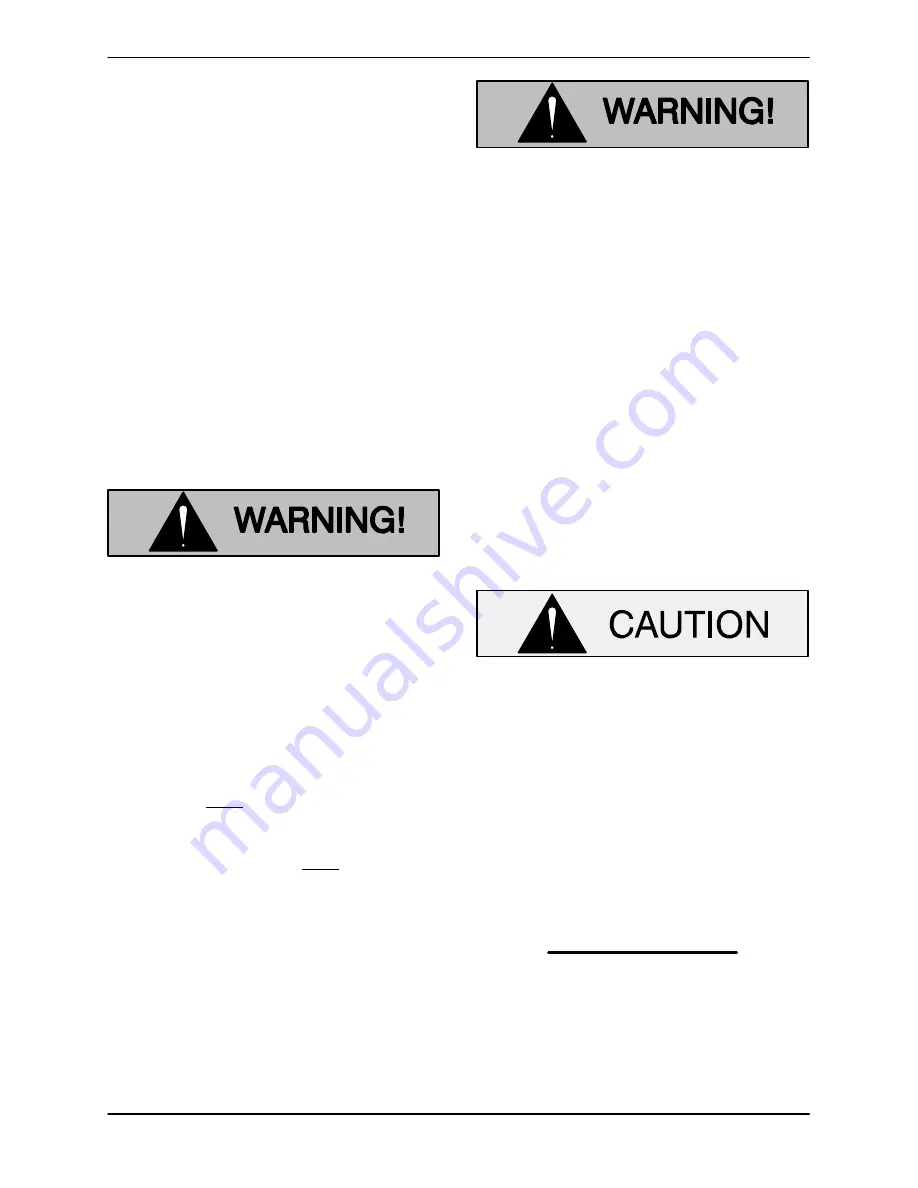
D SERIES
OM-01490
MAINTENANCE & REPAIR
PAGE E - 10
PUMP AND GEARBOX DISASSEMBLY
AND REASSEMBLY
Review all SAFETY information in Section A.
Follow the instructions on all tags, label and de
cals attached to the pump.
This pump requires little service due to its rugged,
minimum‐maintenance design. However, if it be
comes necessary to inspect or replace the wearing
parts, follow these instructions which are keyed to
the sectional views (see Figures 1, 2, 3 and 4) and
the accompanying parts lists.
Most service functions may be performed without
separating the pump and gearbox from the motor.
If major repair is required, the pump, gearbox and
motor must be disconnected.
This manual will alert personnel to
known procedures which require spe
cial attention, to those which could
damage equipment, and to those which
could be dangerous to personnel.
How
ever, this manual cannot possibly antici
pate and provide detailed instructions
and precautions for every situation that
might occur during maintenance of the
unit. Therefore, it is the responsibility of
the owner/maintenance personnel to
ensure that only safe, established main
tenance procedures are used, and that
any procedures not addressed in this
manual are performed only after estab
lishing that neither personal safety nor
pump integrity are compromised by
such practices.
Before attempting to service the pump, shut off in
coming power to the motor and lock it out to ensure
that it will remain inoperative. Close all valves in the
suction and discharge lines.
For motor disassembly and repair, consult the lit
erature supplied with the motor, or contact your lo
cal motor representative.
Before attempting to open or service the
pump:
1. Familiarize yourself with this man
ual.
2. Disconnect or lock out the power
source to ensure that the pump will
remain inoperative.
3. Allow the pump to completely cool
if overheated.
4. Check the temperature before
opening any covers, plates, or
plugs.
5. Close the suction and discharge
valves.
6. Vent the pump slowly and cau
tiously.
7. Drain the pump.
Before attempting to service the pump, drain the
pump by removing the drain plug (17, Figure 2).
Clean and reinstall the drain plug.
Use
Only Genuine Gorman-Rupp
re
placement parts. Failure to do so may cre
ate a hazard and damage the pump or di
minish optimal pump performance. Any
such hazard, damage or diminished per
formance is not covered by the warranty.
NOTE
When appropriate recycling facilities are available,
the user should recycle components and fluids
when doing any routine maintenance / repairs and
also at the end of the pump’s useful life. All other
components and fluids shall be disposed of ac
cording to all applicable codes and regulations.
Suction And Discharge Check Valve Removal
(Figure 2)
To service the suction and discharge check valves,
remove the suction and discharge piping.