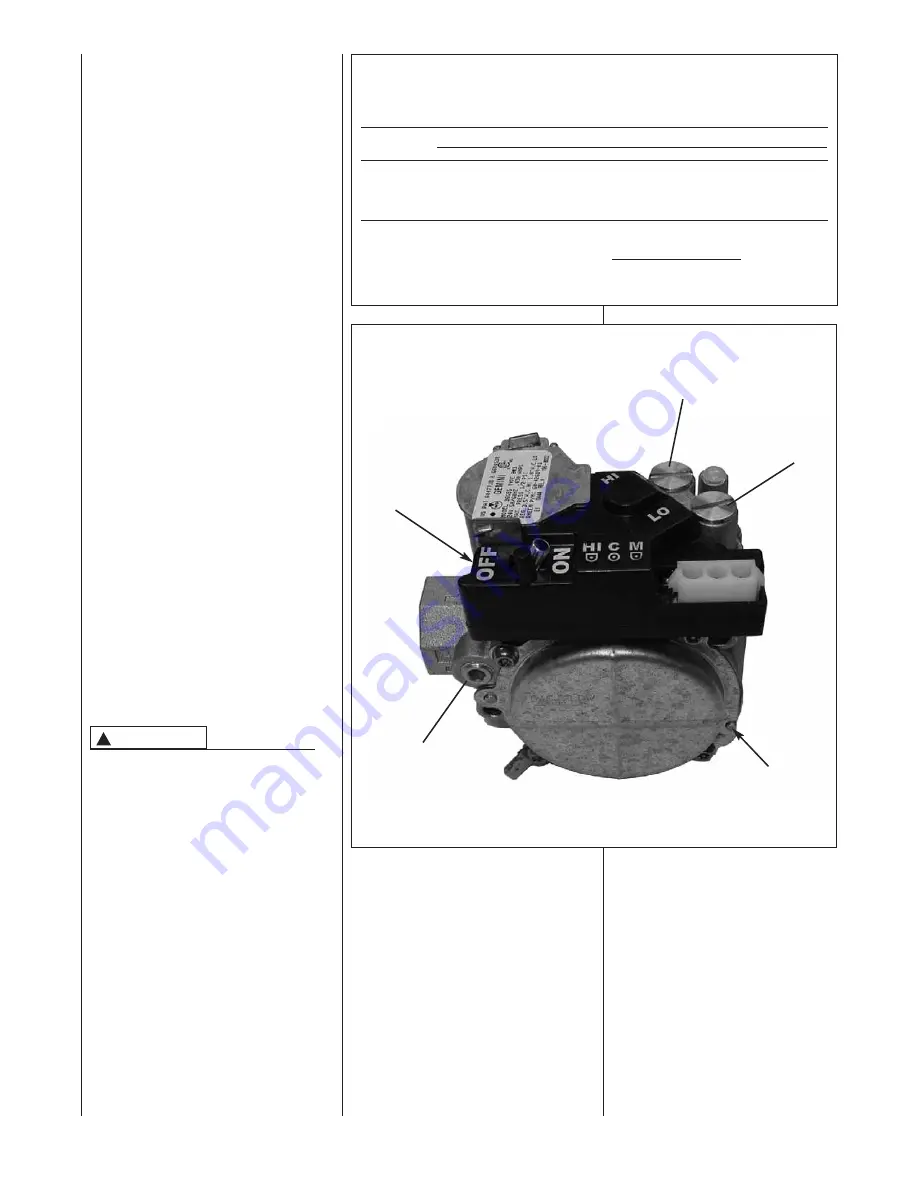
29
1. Shut off the manual main gas
valve and remove the gas
manifold.
2. Replace the orifice spuds.
3. For LP conversion ONLY,
Remove the gas valve.
4. Reassemble in reverse order. In
LP applications, use the new gas
valve provided in the LP
conversion kit.
FIGURE 24
TYPICAL GAS VALVE
GAS VALVE #60-101921-02
To check for gas leakage, use an
approved chloride-free soap and
water solution, or other approved
method.
GAS VALVE
This furnace has a 24-volt gas valve.
It has ports for measuring supply and
manifold gas pressure. The valve
body contains a pressure regulator to
maintain proper manifold gas
pressure.
A control switch is on the valve body.
It can be set to only the
“ON”
or
“OFF”
positions. The gas valve is a
slow-opening valve. See Figure 24.
When energized, it takes 6 to 8
seconds to fully open.
LP CONVERSION
IMPORTANT:
LP gas from trucks
used to transport liquid-based
fertilizers can contain chemicals that
will damage the furnace. Verify that
your gas supplier does not use the
same truck to transport materials
other than LP.
For LP conversion, a new gas valve is
required. The new gas valve is
included in the LP kit. The correct LP
orifices should be selected based on
the altitude of the installation (see
chart below). Orifices included in the
kit are for sea level to 2000 ft.
(1.15mm) and 3000 to 4000 ft.
(1.10mm) The LP Gas Valve Kit is
FP19. Orifices for elevations 4000 ft.
and above must be ordered. Refer to
Table 4.
ELEVATIONS ABOVE 2000 FT
REQUIRE THAT THE FURNACE
INPUT RATING BE ADJUSTED AND
THAT THE SIZE OF THE BURNER
ORIFICES BE RE-CALCULATED
BASED ON ELEVATION AND GAS
HEATING VALUE. THE BURNER
ORIFICES MAY (OR MAY NOT)
NEED TO BE CHANGED. SEE THE
SECTION TITLED “HIGH ALTITUDE
INSTALLATIONS” OF THIS BOOK
FOR INSTRUCTIONS.
NOTE:
Furnace conversion to LP gas
must be performed by a qualified
installer, service agency or the gas
supplier.
To change the gas valve and orifice
spuds for either conversion to LP or
for elevation:
TABLE 3
NATURAL GAS PIPE CAPACITY TABLE (CU. FT./HR.)
Capacity of gas pipe of different diameters and lengths in cu. ft. per hr. with pressure drop of 0.3 in. and specific
gravity of 0.60 (natural gas).
Nominal
Length of Pipe, Feet
Iron Pipe
Size, Inches
10
20
30
40
50
60
70
80
1/2
132
92
73
63
56
50
46
43
3/4
278
190
152
130
115
105
96
90
1
520
350
285
245
215
195
180
170
1-1/4
1,050
730
590
500
440
400
370
350
1-1/2
1,600
1,100
890
760
670
610
560
530
After the length of pipe has been determined, select the pipe size which will provide the minimum cubic feet per hour
required for the gas input rating of the furnace. By formula:
Gas Input of Furnace (BTU/HR)
Cu. Ft. Per Hr. Required
=
Heating Value of Gas (BTU/FT
3
)
The gas input of the furnace is marked on the furnace rating plate. The heating value of the gas (BTU/FT
3
) may be
determined by consulting the local natural gas utility or the LP gas supplier.
5. Attach the notice label alerting
the next service technician that
the furnace has been converted
to LP gas.
6. Turn the gas supply back on and
check for proper operation, leaks
and manifold pressure. See
Figures 26 and 28.
NOTE:
Orifices in the kit are sized for
a heating value of 2500 BTU per
cubic ft. for LP.
GAS CONTROL
SWITCH
INLET
PRESSURE
TAP
OUTLET
PRESSURE
TAP
LOW FIRE
MANIFOLD
PRESSURE
ADJUSTMENT
HIGH FIRE
MANIFOLD
PRESSURE
ADJUSTMENT
CAUTION
!