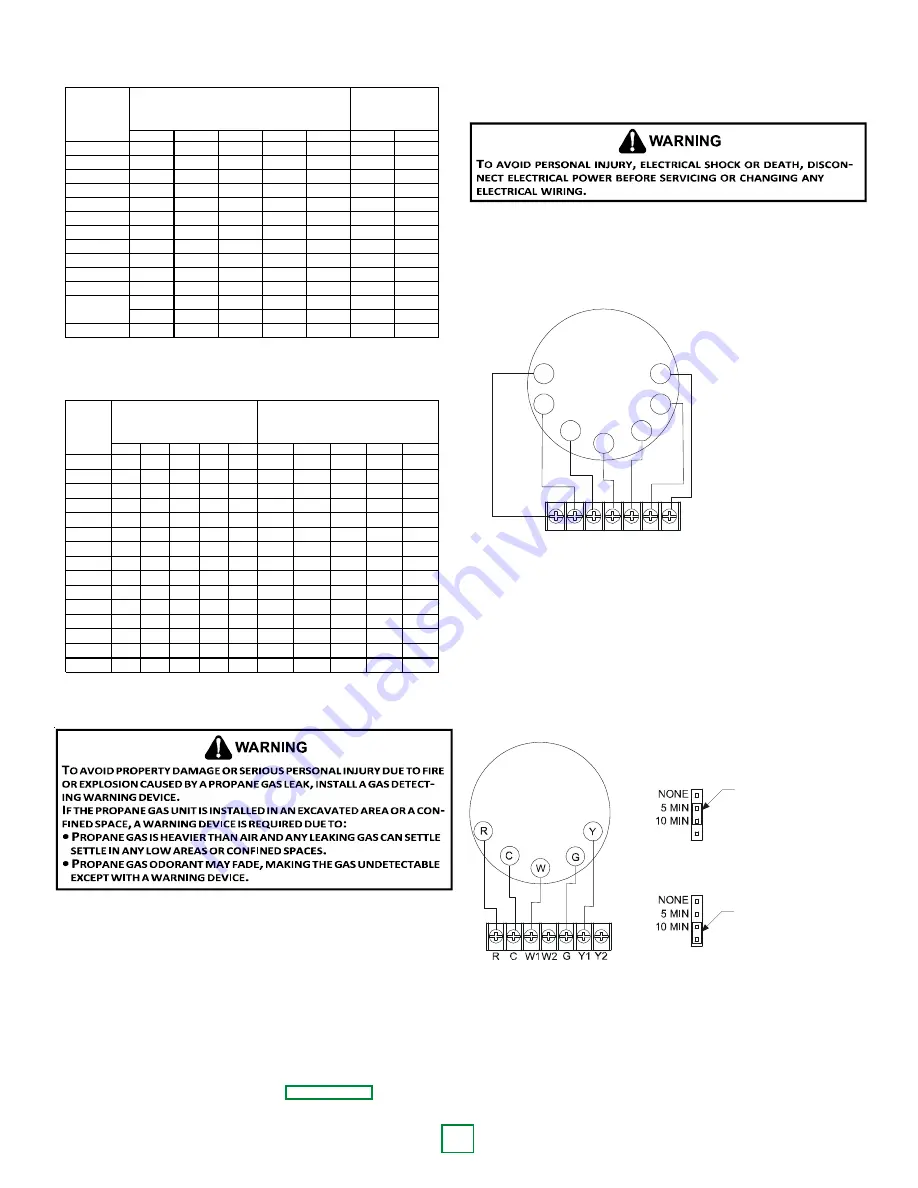
9
cooling. Units which will have economizers may use thermostats
with two or three stages of cooling. All units can use single stage
or multi-stage thermostats. Refer to figures later in this section
for wiring.
The units are designed for operation on 60 hertz current and at
voltages as shown on the rating plate. All internal wiring in the
unit is complete. It is necessary to bring in the power supply to
the contactor as shown on the unit wiring diagram which is
supplied with each unit. The low voltage wiring must be connected
between the unit control panel and the room thermostat.
R C W1W2 G Y1 Y2
R
Y2
C
Y1
W1
G
W2
Furnace Integrated
Control Module
Thermostat
Two-Stage Heating
with
Two-Stage Cooling
(
(
Two-Stage Heating with Two-Stage Cooling
Thermostat Diagram
S
INGLE
S
TAGE
T
HERMOSTAT
To use a single stage thermostat, move jumper located to the
left of the terminal strip labeled “Stage Delay” from NONE to
“5” or “10” minutes. This selection will cause the control to
run on low stage for the selected time (5 or 10 minutes) then
shift to HIGH STAGE. This option controls both cooling and
heating modes. If the jumper is not moved, only low-stage
cool and low-stage heat will operate.
5 MINUTE DELAY
PERIOD WITH
JUMPER IN THIS
POSITION
10 MINUTE DELAY
PERIOD WITH
JUMPER IN THIS
POSITION
Two-Stage Heating (timed) and Two-Stage Cooling (timed)
with Single Stage Thermostat Diagram
Refer to the unit wiring diagram for electrical connections.
When installed, the unit must be electrically grounded in
accordance with local codes or in the absence of local codes,
with the National Electrical Code, ANSI/NFPA No. 70, and/or
the CSA C22.1 Electrical Code. Ensure low voltage
connections are waterproof.
Sizing Between First and Second Stage Regulator
Maximum Propane Capacities listed are based on 1 PSIG Pressure Drop at 10
PSIG Setting. Capacities in 1,000 BTU/HR
3/8"
1/2"
5/8"
3/4"
7/8"
1/2"
3/4"
30
309
700
1,303
2,205
3,394
1,843
3,854
40
265
599
1,115
1,887
2,904
1,577
3,298
50
235
531
988
1,672
2,574
1,398
2,923
60
213
481
896
1,515
2,332
1,267
2,649
70
196
446
824
1,394
2,146
1,165
2,437
80
182
412
767
1,297
1,996
1,084
2,267
90
171
386
719
1,217
1,873
1,017
2,127
100
161
365
679
1,149
1,769
961
2,009
150
130
293
546
923
1,421
772
1,613
200
111
251
467
790
1,216
660
1,381
250
90
222
414
700
1,078
585
1,224
300
89
201
378
634
976
530
1,109
350
82
185
345
584
898
488
1,020
400
76
172
321
543
836
454
949
To convert to Capacities at 15 PSIG Settings -- Multiply by 1.130
To convert to Capacities at 5 PSIG Settings -- Multiply by 0.879
PIPE OR
TUBING
LENGTH,
FEET
NOMINAL PIPE SIZE,
SCHEDULE 40
TUBING SIZE, O.D., TYPE L
Sizing Between Single or Second Stage Regulator and Appliance*
Maximum Propane Capacities Listed are Based on 1/2" W.C. Pressure Drop at
11" W.C. Setting. Capacities in 1,000 BTU/HR
3/8"
1/2"
5/8"
3/4"
7/8"
1/2"
3/4"
1"
1-1/4"
1-1/2"
10
49
110
206
348
539
291
608
1,146
2,353
3,525
20
34
76
141
239
368
200
418
788
1,617
2,423
30
27
61
114
192
296
161
336
632
1,299
1,946
40
23
52
97
164
253
137
284
541
1,111
1,665
50
20
46
86
146
224
122
255
480
985
1,476
60
19
42
78
132
203
110
231
436
892
1,337
80
16
36
67
113
174
94
198
372
764
1,144
100
14
32
59
100
154
84
175
330
677
1,014
125
12
28
52
89
137
74
155
292
600
899
150
11
26
48
80
124
67
141
265
544
815
200
10
22
41
69
106
58
120
227
465
697
250
9
19
36
61
94
51
107
201
412
618
300
8
18
33
55
85
46
97
182
374
560
350
7
16
30
51
78
43
89
167
344
515
400
7
15
28
47
73
40
83
156
320
479
*DATA IN ACCORDANCE WITH NFPA PAMPHLET NO. 54
NOMINAL PIPE SIZE,
SCHEDULE 40
TUBING SIZE, O.D., TYPE L
PIPE OR
TUBING
LENGTH,
FEET
Propane Gas Pipe Sizing
ELECTRICAL WIRING
T
HERMOSTAT
L
OCATION
Mount the thermostat approximately five feet above the floor,
in an area that has an inside, vibration-free wall and has
good air circulation.
Movement of air must not be obstructed by furniture, door,
draperies, etc. The thermostat must not be mounted where it
will be affected by drafts, hot or cold water pipes or air ducts in
walls, radiant heat from fireplace, lamps, the sun, television,
etc. Consult the Instruction Sheet packaged with thermostat
for mounting instructions.
NOTE:
*PG1524, *PG1530, *PG1537, and *PG1549 units have
one stage of mechanical cooling and two stages of heat. All other
units have two stages of heating and two stages of mechanical
Summary of Contents for GPG152407041
Page 19: ...19 APPENDIX ...