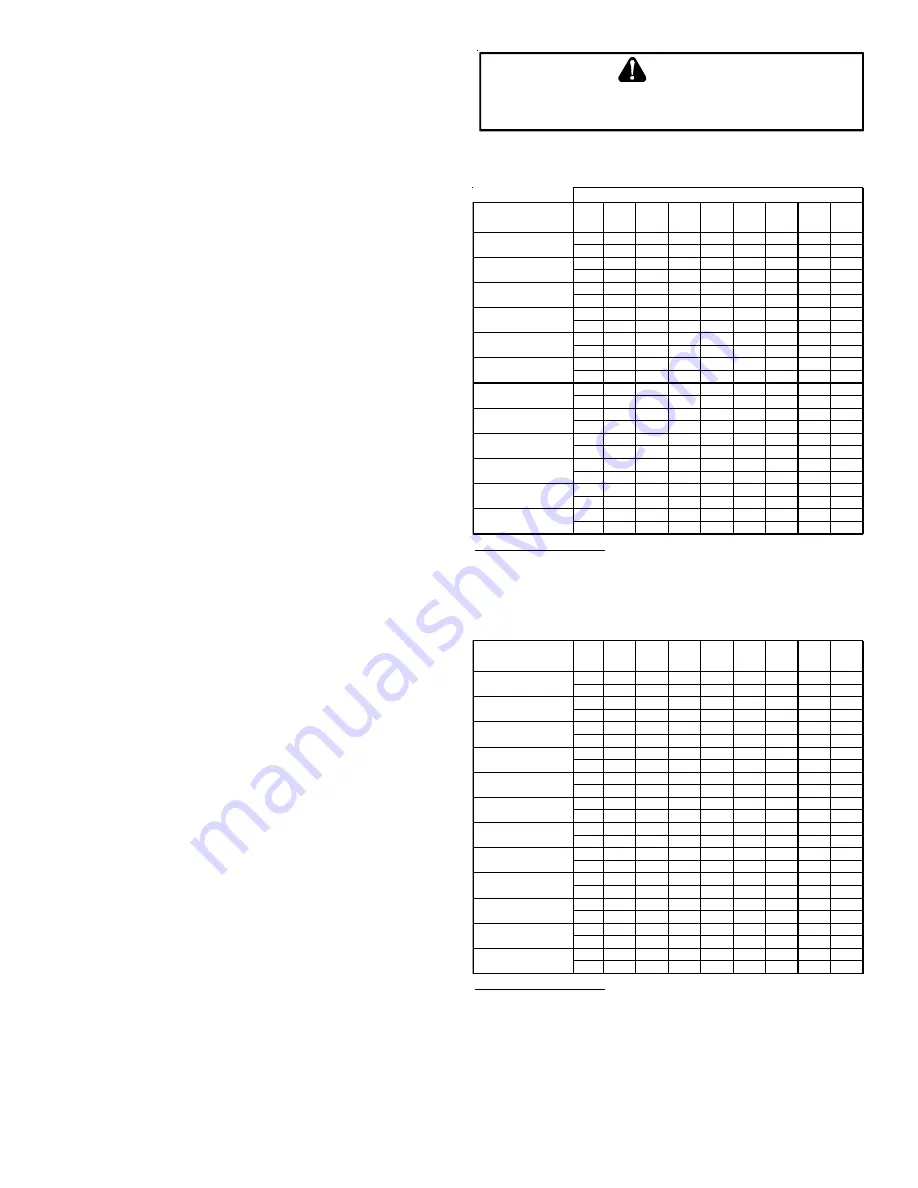
15
4. Use a knockout tool to create a 3" diameter hole
5. Install combustion air flange and secure with screws
removed in step one.
N
ON
-D
IRECT
V
ENT
(S
INGLE
P
IPE
) P
IPING
Non-direct
vent
installations require only a vent/flue pipe. The
vent pipe can be run horizontally with an exit through the side of
the building or run vertically with an exit through the roof of the
building. The vent can also be run through an existing
unused
chimney; however, it must extend a minimum of 12 inches above
the top of the chimney. The space between the vent pipe and the
chimney must be closed with a weather-tight, corrosion-resistant
flashing.
Although
non-direct
vent
installations do not require a combustion
air intake
pipe
, a minimum of one 90° elbow should be attached to
the furnace’s combustion air intake
if
: an upright installation uses
the standard intake location, or a horizontal installation uses the
alternate air intake location. This elbow will guard against inad-
vertent blockage of the air intake.
V
ENT
/F
LUE
P
IPE
L
ENGTHS
AND
D
IAMETERS
(For Installations At or Above 7,000 Feet using 3” Venting)
NOTE:
If either a 90 degree or 45 degree elbow is used for
termination, it must be pointed downward.
Refer to the Direct and Non-Direct Vent Table for applicable length,
elbows, and pipe diameter for construction of the vent/flue pipe
system of a non-direct vent installation. In addition to the vent/
flue pipe, a single 90° elbow should be secured to the combustion
air intake to prevent inadvertent blockage. The tee used in the
vent/flue termination must be included when determining the num-
ber of elbows in the piping system.
V
ENT
/F
LUE
P
IPE
T
ERMINATIONS
NOTE:
If either a 90 degree or 45 degree elbow is used for
termination, it must be pointed downward.
The vent/flue pipe may terminate vertically, as through a roof, or
horizontally, as through an outside wall.
Vertical vent/flue pipe terminations should be as shown in the fol-
lowing figure. Refer to
Vent/Flue Pipe and Combustion Air Pipe -
Termination Locations
for details concerning location restrictions.
The penetration of the vent through the roof must be sealed tight
with proper flashing such as is used with a plastic plumbing vent.
Horizontal vent/flue pipe terminations should be as shown in the
following figure. Refer to
Vent/Flue Pipe and Combustion Air Pipe.
To secure the pipe passing through the wall and prohibit damage to
piping connections, a coupling should be installed on either side of
the wall and solvent cemented to a length of pipe connecting the
two couplings. The length of pipe should be the wall thickness plus
the depth of the socket fittings to be installed on the inside and
outside of the wall. The wall penetration should be sealed with silicone caulking material.
NOTE: Terminate both pipes in the same pressure zone (same side of roof, no major obstacles between pipes, etc.).
B
E
SURE
NOT
TO
DAMAGE
INTERNAL
WIRING
OR
OTHER
COMPONENTS
WHEN
REINSTALLING
COUPLING
AND
SCREWS
.
CAUTION
MODEL
PIPE
SIZE
1
2
3
4
5
6
7
8
2
^
145
140
135
130
125
120
115
110
3
168
161
154
147
140
133
126
119
2
55
50
45
40
35
30
25
20
3
127
120
113
106
99
92
85
78
2
^
30
25
20
15
10
5
N/A
N/A
3
^
72
65
58
51
44
37
30
23
2
^
30
25
20
15
10
5
N/A
N/A
3
^
72
65
58
51
44
37
30
23
2
^
40
35
30
25
20
15
10
5
3
72
65
58
51
44
37
30
23
2
60
55
50
45
40
35
30
25
3
168
161
154
147
140
133
126
119
2
30
25
20
15
10
5
N/A
N/A
3
113
106
99
92
85
78
71
64
2
N/A
N/A
N/A
N/A
N/A
N/A
N/A
N/A
3
65
58
51
44
37
30
23
16
2
100
95
90
85
80
75
70
65
3
137
130
123
116
109
102
95
88
2
60
55
50
45
40
35
30
25
3
127
120
113
106
99
92
85
78
2
35
30
25
20
15
10
5
N/A
3
160
153
146
139
132
125
118
111
2
N/A
N/A
N/A
N/A
N/A
N/A
N/A
N/A
3
127
120
113
106
99
92
85
78
7,000 f t altitude or above use 3" pipe
^
*MSS920402BN - add 20' of 2" pipe for upflow position
^
*MSS920803BN - add 10' of 2" pipe for upf low position, add 66' of 3" pipe f or upflow position
^
*MSS920804CN - add 25' of 2" pipe for upf low position, add 58' of 3" pipe f or upf low position
^ *MSS920805CN - add 15' of 2" pipe for upflow position, add 58' of 3" pipe f or upf low position
MODEL
PIPE
SIZE
1
2
3
4
5
6
7
8
2
^
100
95
90
85
80
75
70
65
3
168
161
154
147
140
133
126
119
2
45
40
35
30
25
20
15
10
3
168
161
154
147
140
133
126
119
2
^
35
30
25
20
15
10
5
N/A
3
168
161
154
147
140
133
126
119
2
60
55
50
45
40
35
30
25
3
113
106
99
92
85
78
71
64
2
45
40
35
30
25
20
15
10
3
120
113
106
99
92
85
78
71
2
40
35
30
25
20
15
10
5
3
151
144
137
130
123
116
109
102
2
N/A
N/A
N/A
N/A
N/A
N/A
N/A
N/A
3
158
151
144
137
130
123
116
109
2
100
95
90
85
80
75
70
65
3
137
130
123
116
109
102
95
88
2
45
40
35
30
25
20
15
10
3
168
161
154
147
140
133
126
119
2
40
35
30
25
20
15
10
5
3
120
113
106
99
92
85
78
71
2
N/A
N/A
N/A
N/A
N/A
N/A
N/A
N/A
3
113
106
99
92
85
78
71
64
2
N/A
N/A
N/A
N/A
N/A
N/A
N/A
N/A
3
110
103
96
89
82
75
68
61
7,000 f t altitude or above use 3" pipe
^ *MSS960402BN - add 25' of 2" pipe for upflow position
^
*MSS960803BN - add 20' of 2" pipe for upf low position
Number of Elbows
*MSS920402BN
*MSS920603BN
*MSS921004CN
*MSS960603BN
*MSS920803BN
*MSS920804CN
*MSS920805CN
*CSS920804CN
*CSS921005CN
*MSS960402BN
*MSS921005CN
*MSS921205DN
*CSS920402BN
*CSS920603BN
*MSS960804CN
*MSS960805CN
*MSS961005CN
*CSS961005CN
*MSS960803BN
*CSS961205DN
*MSS961205DN
*CSS960402BN
*CSS960603BN
*CSS960804CN
*MSS9* / *CSS9 Direct Vent (2-Pipe) & Non-Direct Vent (1-Pipe)
Maximum Allowable Length of Vent/FLue Pipe