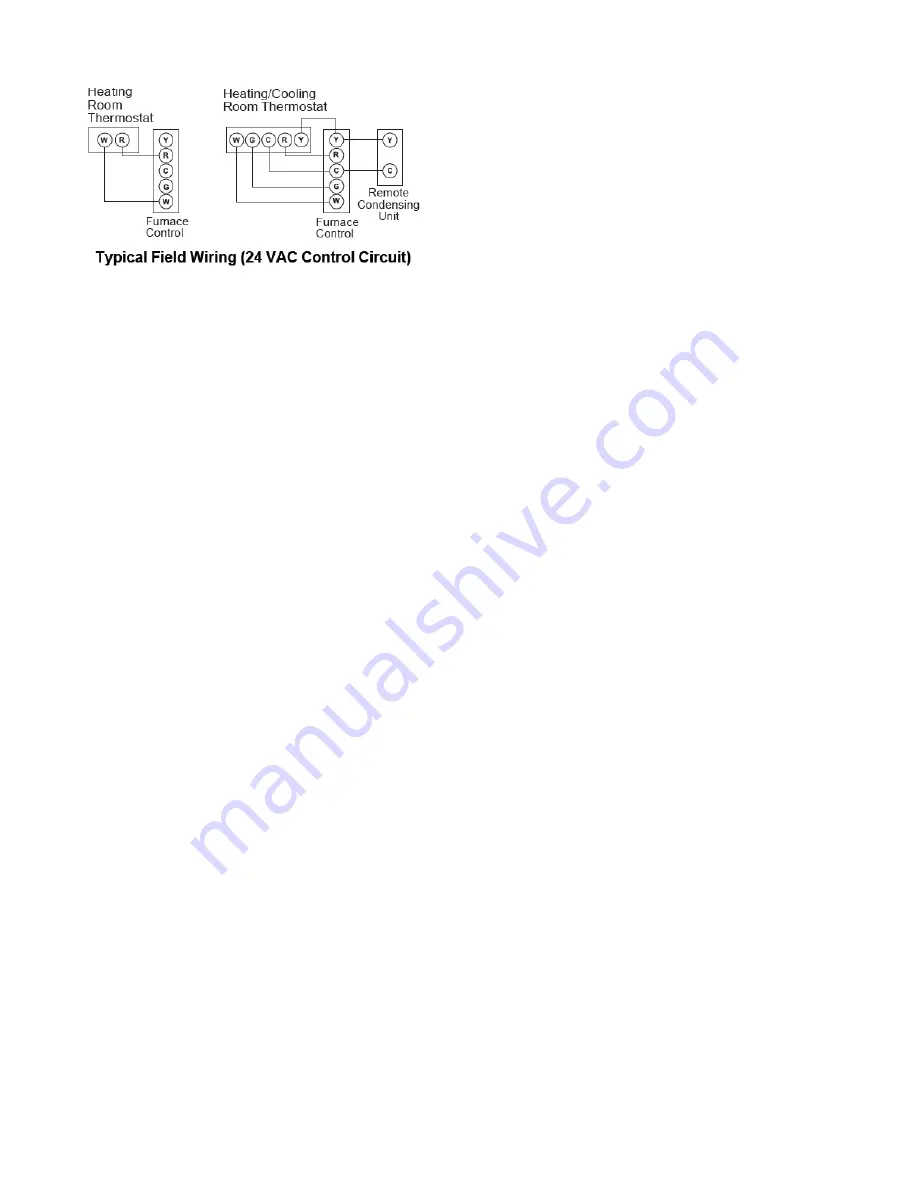
SYSTEM OPERATION
11
ADDITIONAL FILTERING ACCESSORIES
External Filter Rack Kit (EFR02)
The external filter rack kit is intended to provide a location
external to the furnace casing, for installation of a permanent
filter on upflow model furnaces. The rack is designed to mount
over the indoor blower compartment area of either side panel,
and provide filter retention as well as a location for attaching
return air ductwork.
Electronic Air Cleaner or Media Air Cleaner
The electronic air cleaner and media air cleaner are multi-
positional high efficiency air filtration devices that can be
installed in any position, except with the access door facing
down. The best location for the air cleaner is in the return
air duct next to the blower compartment. Before installing
the air cleaner, consider the application. The electronic air
cleaner must be readily accessible for periodic inspection and
cleaning of the pre-filters and electronic cells while the media
air cleaner must be readily accessible for periodic inspection
and replacement of the Media.
NORMAL SEQUENCE OF OPERATION
Power Up
•
120 VAC power applied to furnace.
•
Integrated ignition control performs internal checks.
•
LED light will flash once at power up and then remain on.
•
Integrated ignition control monitors safety circuit
continuously.
•
Furnace awaits call from thermostat.
Heating Mode
The normal operational sequence in heating mode is as
follows:
•
R and W thermostat contacts close, initiating a call for
heat.
•
Integrated control module performs safety circuit checks.
•
Pressure Sensor Verification:
The control operates
the inducer in a manner to verify the pressure sensor
null value and span operation are within specification.
If the system is operating correctly, this test takes only
a few seconds. If the system is not functioning properly,
the control times out after a maximum 90 seconds and
display the proper fault code.
•
Induced draft blower is energized for 30 second
prepurge.
•
Igniter warm up begins after 30 second prepurge expires.
•
Gas valves open at end of igniter warm up period,
delivering gas to burners and establishing flame.
•
Integrated control module monitors flame presence. Gas
valve will remain open only if flame is detected.
•
Circulator blower is energized on high heat speed
following a fixed 30 second blower on delay. Electronic
air cleaner terminals are energized with circulator blower.
•
Furnace operates; integrated control module monitors
safety circuits continuously.
•
R and W thermostat contacts open, completing the call
for heat.
•
Gas valve closes, extinguishing flame.
•
Induced draft blower is de-energized following a thirty
second post purge.
•
HUM terminal is de-energized.
•
Circulator blower continues running for selected heat off
delay period factory set at 120 seconds. If required this
can be changed in the field.
•
Electronic air cleaner is de-energized.
•
Furnace awaits the next call from thermostat.
Cooling Mode
The normal operational sequence in cooling mode is as
follows:
•
R, Y and G thermostat contacts close, initiating a call
for cool.
•
Integrated control module performs safety circuit checks.
•
Outdoor fan and compressor are energized.
•
Circulator blower is energized on cool speed following a
fixed six second on delay. If required this can be changed
in the field to 45 seconds. Electronic air cleaner terminals
are energized with circulator blower.
•
Furnace circulator blower and outdoor cooling unit
run, integrated control module monitors safety circuits
continuously.
•
R, Y and G thermostat contacts open, completing the
call for cool.
•
Outdoor fan and compressor are de-energized.
•
Circulator blower is de-energized following a fixed forty
firve second cool off delay period. Electronic air cleaner
terminals are de-energized.
•
Furnace awaits the next call from thermostat.
Fan Only Mode
The normal operational sequence in Fan Only Mode is as
follows:
•
R and G thermostat contacts close, initiating a call for
Summary of Contents for AMES960403BU AA
Page 25: ...TROUBLESHOOTING 25...
Page 26: ...TROUBLESHOOTING 26...