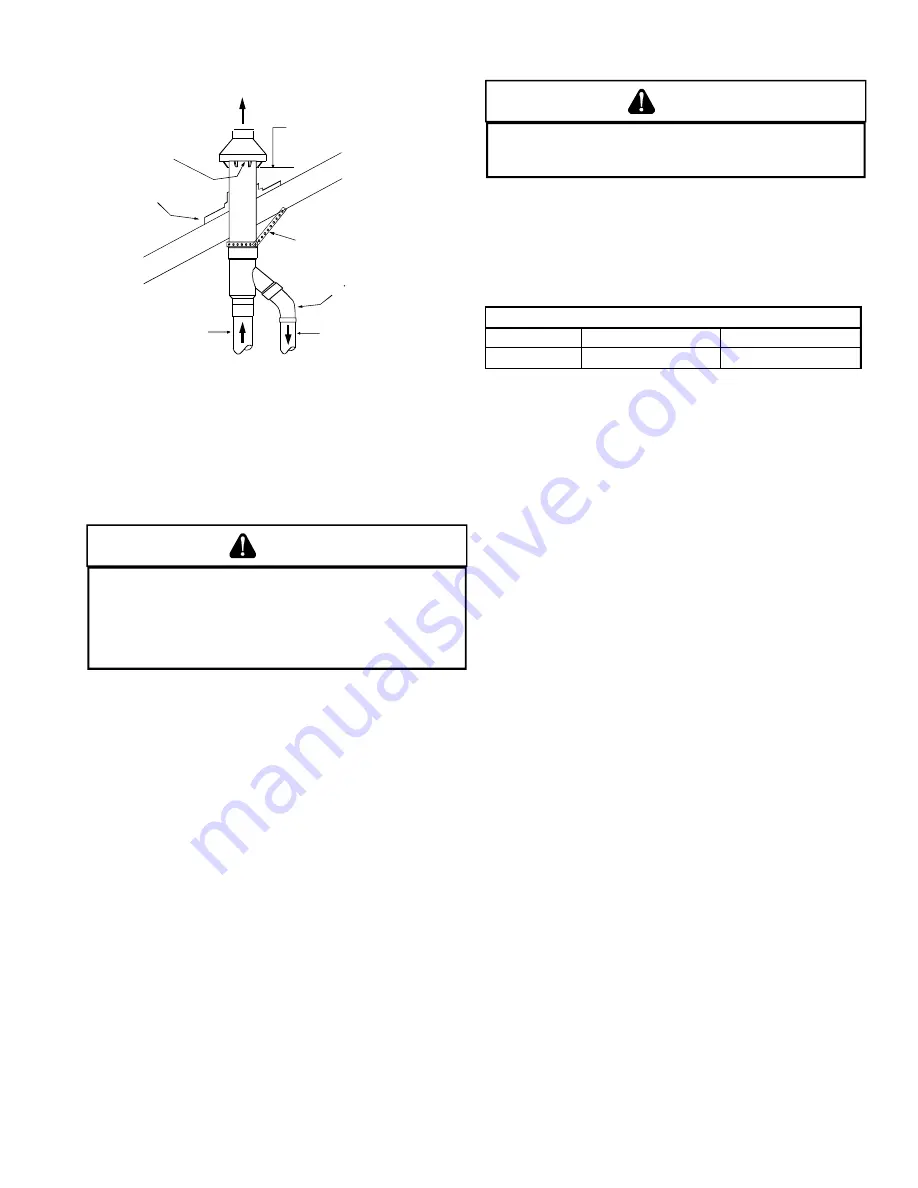
INSTALLATION CONSIDERATIONS
21
Vent
Maintain 12" (18" for Canada)
minimum clearance above highest
anticipated snow level. Maximum of
24" above roof.
Combustion Air
Roof Boot/Flashing
(Field Supplied)
Support (Field Supplied)
45 Elbow
(Field Supplied)
Combustion Air
Vent
Condensate Drain Lines and Drain Trap
A condensing gas furnace achieves its high level of efficiency
by extracting almost all of the heat from the products of
combustion and cooling them to the point where condensa-
tion takes place. The condensate which is generated must
be piped to an appropriate drain location.
WARNING
I
N UPRIGHT UPFLOW INSTALLATIONS, THE DRAIN TRAP MUST BE MOUNTED ON
THE OPPOSITE SIDE OF THE UNIT FROM THE JUNCTION BOX.
T
HIS WILL
REDUCE THE RISK OF WATER REACHING THE JUNCTION BOX IN THE EVENT OF
A BLOCKED DRAIN CONDITION.
F
AILURE TO FOLLOW THESE INSTRUCTIONS
CAN RESULT IN POSSIBLE PROPERTY DAMAGE, PERSONAL INJURY, OR DEATH
DUE TO ELECTRICAL SHOCK.
•
If the drain line is routed through an area which may
see temperatures near or below freezing, precau-
tions must be taken to prevent condensate from
freezing within the drain line.
•
If an air conditioning coil is installed with the
furnace, a common drain may be used. An open
tee must be installed in the drain line, near the
cooling coil, to relieve positive air pressure from the
coil’s plenum. This is necessary to prohibit any
interference with the function of the furnace’s drain
trap.
GAS SUPPLY AND PIPING
The furnace rating plate includes the approved furnace gas
input rating and gas types. The furnace must be equipped to
operate on the type of gas applied. This includes any con-
version kits required for alternate fuels and/or high altitude.
CAUTION
T
O PREVENT UNRELIABLE OPERATION OR EQUIPMENT DAMAGE, THE INLET
GAS SUPPLY PRESSURE MUST BE AS SPECIFIED ON THE UNIT RATING PLATE
WITH ALL OTHER HOUSEHOLD GAS FIRED APPLIANCES OPERATING.
Inlet gas supply pressures must be maintained within the
ranges specified below. The supply pressure must be con-
stant and available with all other household gas fired appli-
ances operating. The minimum gas supply pressure must
be maintained to prevent unreliable ignition. The maximum
must not be exceeded to prevent unit overfiring.
Natural Gas
Minimum: 4.5" w.c.
Maximum: 10.0" w.c.
Propane Gas
Minimum: 11.0" w.c.
Maximum: 13.0" w.c.
INLET GAS SUPPLY PRESSURE
HIGH ALTITUDE DERATE
When this furnace is installed at high altitude, the appropri-
ate High Altitude orifice kit must be applied. This is re-
quired due to the natural reduction in the density of both
the gas fuel and combustion air as altitude increases. The
kit will provide the proper design certified input rate within
the specified altitude range.
High altitude kits are purchased according to the installa-
tion altitude and usage of either natural or propane gas.
Refer to the product Specification Sheet or Technical Manual
for a tabular listing of appropriate altitude ranges and corre-
sponding manufacturer’s high altitude (Natural, Propane gas,
and/or Pressure Switch) kits.
Do
not
derate the furnace by adjusting the manifold pres-
sure to a lower pressure than specified on the furnace rat-
ing plate. The combination of the lower air density and a
lower manifold pressure will prohibit the burner orifice from
drawing the proper amount of air into the burner. This may
cause incomplete combustion, flashback, and possible yel-
low tipping.
In some areas the gas supplier may artificially derate the
gas in an effort to compensate for the effects of altitude. If
the gas is artificially derated, the appropriate orifice size
must be determined based upon the BTU/ft
3
content of the
derated gas and the altitude. Refer to the National Fuel
Gas Code, NFPA 54/ANSI Z223.1, and information provided
by the gas supplier to determine the proper orifice size.
A different pressure switch may be required at high altitude
regardless of the BTU/ft
3
content of the fuel used. Refer to
the product Specification Sheet or Technical Manual for a
tabular listing of appropriate altitude ranges and correspond-
ing manufacturer’s pressure switch kits.