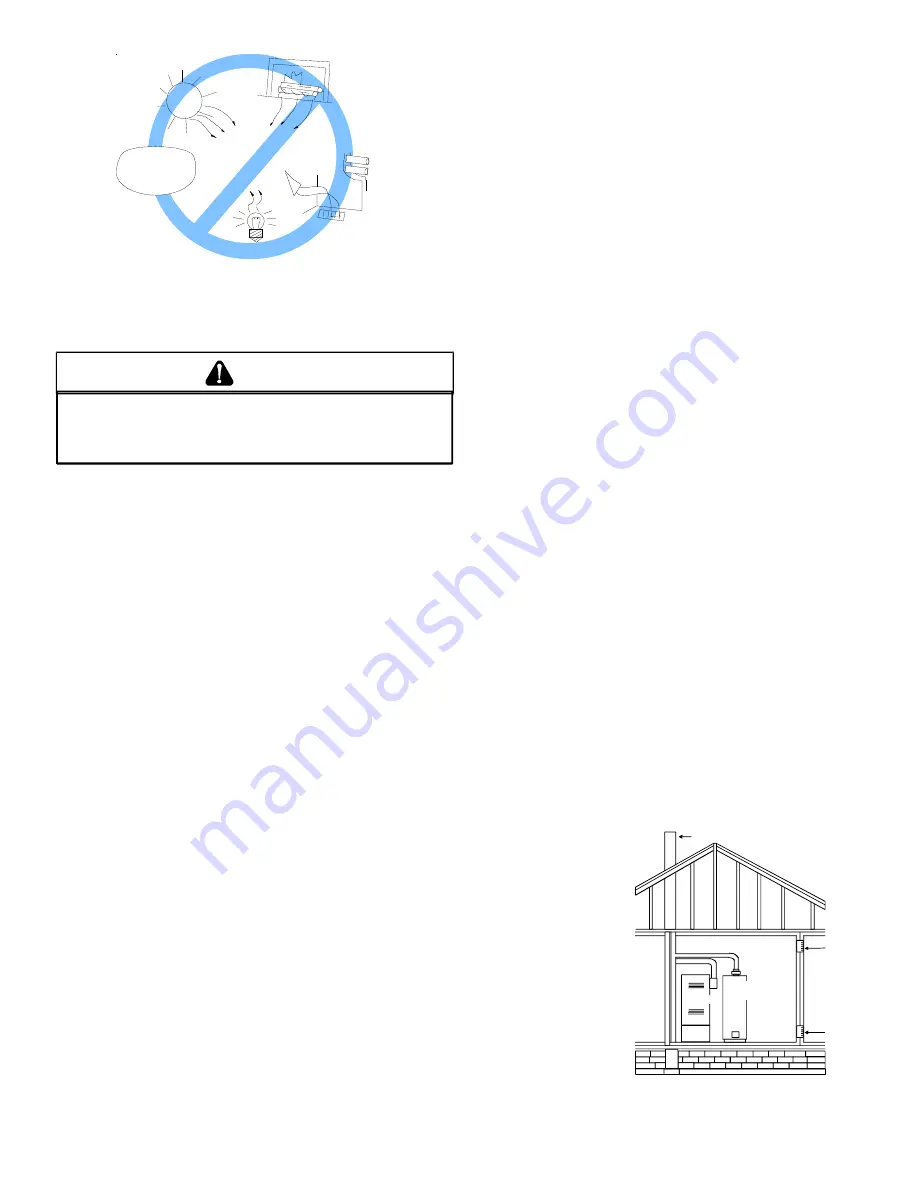
9
HOT
COLD
DRAFTS OR DEAD SPOTS
-BEHIND DOORS
-IN CORNERS
-UNDER CABINETS
Thermostat Influences
Consult the instructions packaged with the thermostat for mounting
instructions and further precautions.
V. COMBUSTION & VENTILATION AIR REQUIREMENTS
T
O
AVOID
PROPERTY
DAMAGE
,
PERSONAL
INJURY
OR
DEATH
,
SUFFICIENT
FRESH
AIR
FOR
PROPER
COMBUSTION
AND
VENTILATION
OF
FLUE
GASES
MUST
BE
SUPPLIED
. M
OST
HOMES
REQUIRE
OUTSIDE
AIR
BE
SUPPLIED
INTO
THE
FURNACE
AREA
.
WARNING
Improved construction and additional insulation in buildings have re-
duced heat loss by reducing air infiltration and escape around doors
and windows. These changes have helped in reducing heating/cool-
ing costs but have created a problem supplying combustion and ven-
tilation air for gas fired and other fuel burning appliances. Appliances
that pull air out of the house (clothes dryers, exhaust fans, fireplaces,
etc.) increase the problem by starving appliances for air.
House depressurization can cause back drafting or improper com-
bustion of gas-fired appliances, thereby exposing building occu-
pants to gas combustion products that could include carbon mon-
oxide.
1. Headaches-Nausea-Dizziness, Flu-Like Symptoms.
2. Excessive humidity-heavily frosted windows or a moist
“clammy” feeling in the home.
3.
Smoke from a fireplace will not draw up the chimney.
4.
Flue gases that will not draw up the appliance vent pipe.
If this furnace is to be installed in the same space with other gas appli-
ances, such as a water heater, ensure there is an adequate supply of
combustion and ventilation air for the other appliances. Refer to the
latest edition of the National Fuel Gas Code ANSI Z223.1 (Section 5.3),
or CSA B149.1-05 Installation Codes (Sections 7.2, 7.3, or 7.4), or
applicable provisions of the local building codes for determining the
combustion air requirements for the appliances.
Most homes will require outside air be supplied to the furnace area
by means of ventilation grilles or ducts connecting directly to the
outdoors or spaces open to the outdoors such as attics or crawl
spaces.
The following information on air for combustion and ventilation is repro-
duced from the
National Fuel Gas Code ANSI Z223.1 Section 5.3.
5.3.1 General:
(a) The provisions of 5.3 apply to gas utilization equipment installed in
buildings and which require air for combustion, ventilation and dilution
of flue gases from within the building. They do not apply to (1) direct
vent equipment which is constructed and installed so that all air for
combustion is obtained from the outside atmosphere and all flue gases
are discharged to the outside atmosphere, or (2) enclosed furnaces
which incorporate an integral total enclosure and use only outside air
for combustion and dilution of flue gases.
(b) Equipment shall be installed in a location in which the facilities for
ventilation permit satisfactory combustion of gas, proper venting and
the maintenance of ambient temperature at safe limits under normal
conditions of use. Equipment shall be located so as not to interfere
with proper circulation of air. When normal infiltration does not pro-
vide the necessary air, outside air shall be introduced.
(c) In addition to air needed for combustion, process air shall be provided
as required for: cooling of equipment or material, controlling dew point,
heating, drying, oxidation or dilution, safety exhaust, odor control, and
air for compressors.
(d) In addition to air needed for combustion, air shall be supplied for ven-
tilation, including all air required for comfort and proper working con-
ditions for personnel.
(e) While all forms of building construction cannot be covered in detail, air
for combustion, ventilation and dilution of flue gases for gas utilization
equipment vented by natural draft normally may be obtained by appli-
cation of one of the methods covered in 5.3.3 and 5.3.4.
(f) Air requirements for the operation of exhaust fans, kitchen ventilation
systems, clothes dryers, and fireplaces shall be considered in deter-
mining the adequacy of a space to provide combustion air require-
ments.
5.3.2 Equipment Located in Unconfined Spaces:
In unconfined spaces (see definition below) in buildings, infiltration may
be adequate to provide air for combustion ventilation and dilution of flue
gases. However, in buildings of tight construction (for example, weather
stripping, heavily insulated, caulked, vapor barrier, etc.), additional air may
need to be provided using the methods described in 5.3.3-b or 5.3.4.
Space, Unconfined.
For purposes of this Code, a space whose volume is not less than 50 cubic
feet per 1,000 BTU per hour of the aggregate input rating of all appli-
ances installed in that space. Rooms communicating directly with the
space in which the appliances are installed through openings not furnished
with doors, are considered a part of the unconfined space.
5.3.3 Equipment Located in Confined Spaces:
(a)
All Air from Inside the Building:
The confined space shall be pro-
vided with two permanent openings communicating directly with an
additional room(s) of sufficient volume so that the combined volume
of all spaces meets the criteria for an unconfined space. The total
input of all gas utilization equipment installed in the combined space
shall be considered in making this determination. Each opening shall
have a minimum free area of 1 square inch per 1,000 BTU per hour
of the total input rating of all gas utilization equipment in the confined
space, but not less than 100 square inches. One opening shall be within
12 inches of the top and one within 12 inches of the bottom of the
enclosure.
Furnace
Water
Heater
Opening
Chimney or Gas Vent
Opening
NOTE: Each opening must have
a free area of not less than one
square inch per 1000 BTU of
the total input rating of all equip-
ment in the enclosure, but not
less than 100 square inches.
Equipment Located in Confined Spaces; All Air from Inside Building.
See 5.3.3-a.