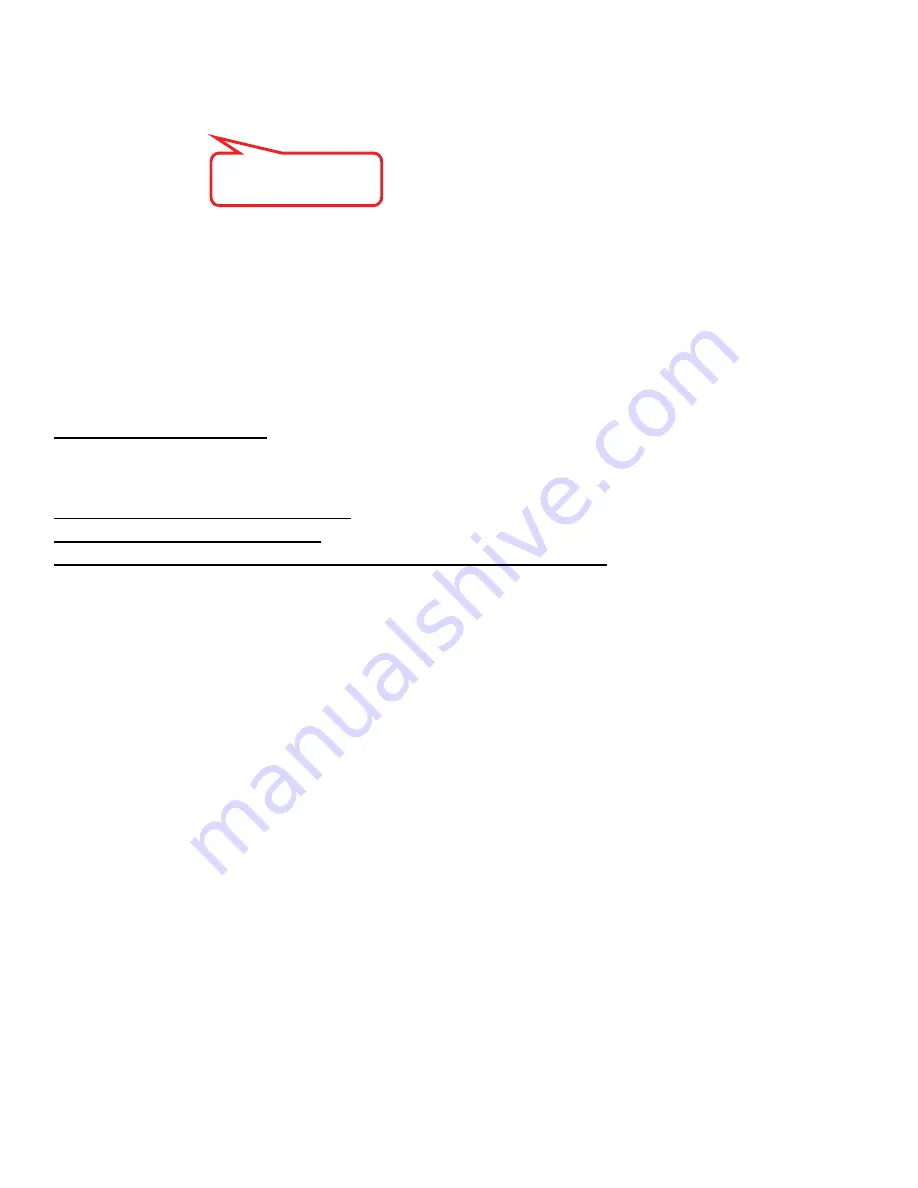
SCHEDULED MAINTENANCE
26
5. Use this formula to verify the Cubic Feet per Hour (CFH) input determined in step 4 is correct:
(3600 x Gas Meter Dial Size) / Time (seconds) = Cubic Feet per Hour (CFH)
3600 is used as there are 60 seconds in
a minute and 60 minutes in an hour.
60x60=3600
6. Check with your local utility for actual BTU content (caloric value) of natural gas in the area (the average is 1025
BTU’s).
7. Use this formula to calculate the BTU/HR input (See BTU/HR Calculation Example):
Cubic Feet per Hour (CFH) x BTU content of your natural gas = BTU/HR input
8. Should the figure you calculated not fall within five (5) percent of the nameplate rating of the unit, adjust the gas valve
pressure regulator or resize orifices. To adjust the pressure regulator on the gas valve, turn downward (clockwise) to
increase pressure and input, and upward (counterclockwise) to decrease pressure and input. A properly operating unit
must have the BTU per hour input and CFM of air, within the limits shown to prevent short cycling of the equipment.
As the external static pressure goes up, the temperature rise will also increase. Consult the proper tables for tempera-
ture rise limitation.
BTU/HR Calculation Example:
The unit being tested takes 40 seconds for the 1 cubic foot dial to make one complete revolution. Using the chart, this
translates to 90 cubic feet per hour. Based upon the assumption that one cubic foot of natural gas has 1,025 BTU’s (Check
with your local utility for actual BTU content), the
calculated input is 92,250 BTU’s per hour.
Furnace Nameplate Input in this example:
90,000 BTU/HR
Calculated Gas Input in this example:
92,250 BTU/HR
This example is within the 5% tolerance input and does not need adjustment.