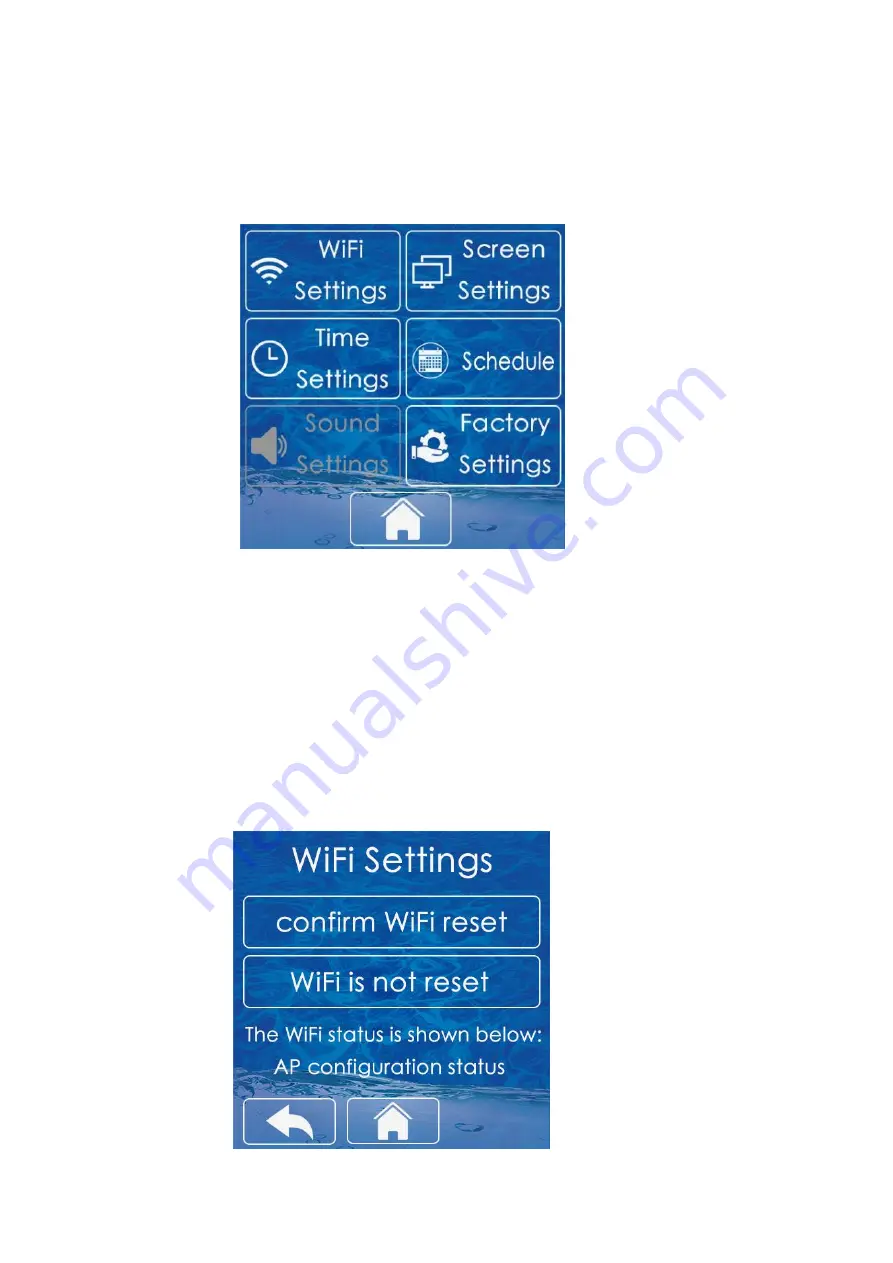
23
2. The Introduction of Wire Controller Functions
The menu interface is divided into 6 setting sections: Wi-Fi setting, screen setting, time setting, timing
setting, sound setting (this function is temporarily canceled), and factory setting, as shown in figure.
Menu interface
1) WIFI Setting
Click the "WIFI Settings" icon on the menu interface to enter the WIFI connection settings. Click "confirm
WIFI reset" to reset the Wi-Fi, and then open the corresponding APP on the phone. After the matching is
successful, the air conditioner can be controlled in the APP. When you have connected to the APP, click
"WIFI is not reset" to choose not to reset Wi-Fi, and then match it on the mobile APP.
Click the "return" icon to return to the menu interface, and click the "main interface" icon to return to the
main interface.
图五
Summary of Contents for NL-BKDX100-400II/R
Page 1: ...1...
Page 7: ...7 NL BKDX50 200II R NL BKDX60 220II R NL BKDX50 200II R32...
Page 8: ...8 NL BKDX80 300II R NL BKDX100 400II R...
Page 18: ...18 7 Connection diagram...
Page 42: ...1...