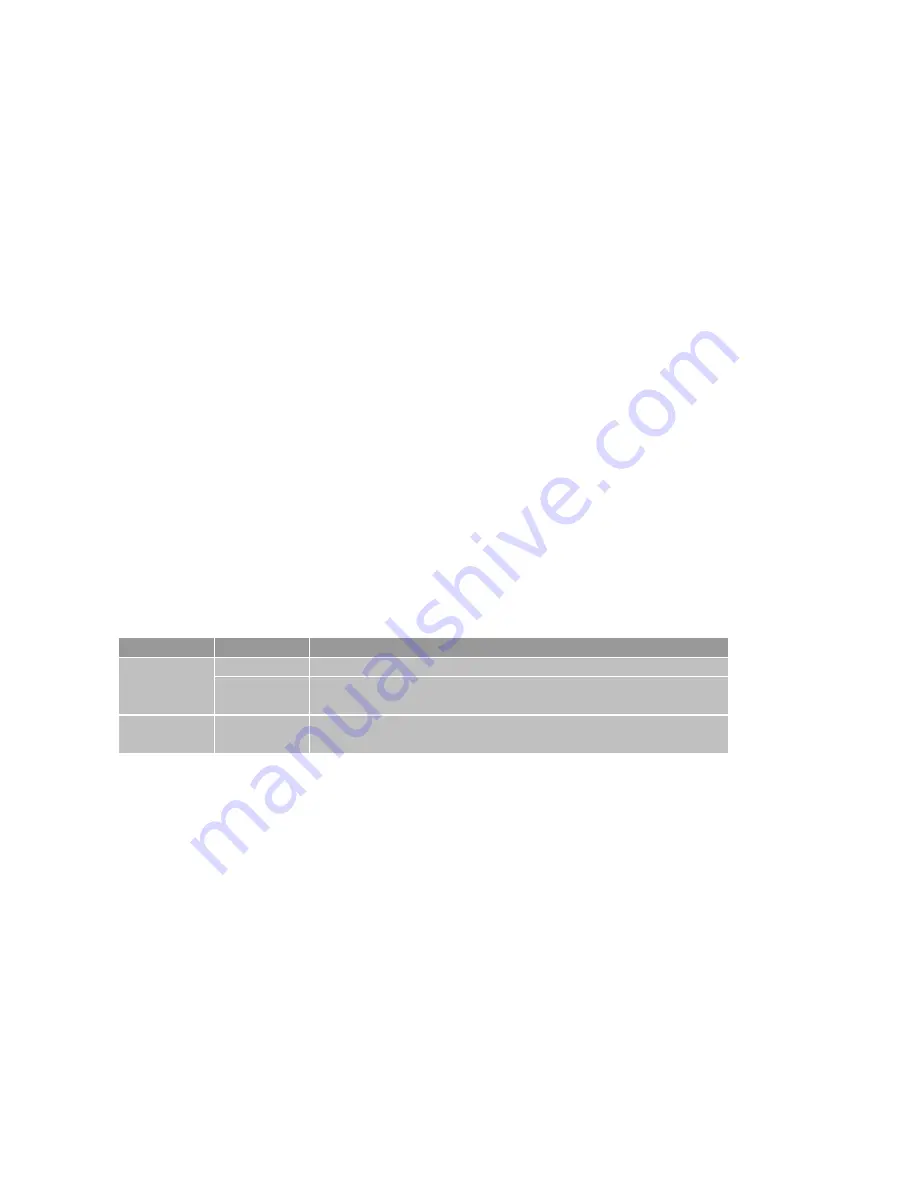
RAIL SAW SR 310 H
OPERATION MANUAL
23
7
Maintenance
Proper, on schedule maintenance increases the service life of the machine, ensures availability and helps prevent unwanted
standstill. The components of the machine are subject to different maintenance intervals depending on the use. The maintenance
intervals must be determined by the system operator as part of the hazard evaluation and risk assessment. Observe the guidelines
in the applicable directives.
Service and maintenance measures are permitted only by qualified specialist companies.
Maintenance must be documented by the operator. It should be clear who carried out the work, when and where (proof of
maintenance).
Only original spare parts as well as suitable tools may be used:
-
The recommended maintenance intervals and inspection intervals are to be followed!
-
The causes of possible defects are looked for, e.g. damage, disturbing sounds, overheating, etc.
The machine must always be depressurized before maintenance work.
7.1
Recommended maintenance plan
Components for which wear and tear or even malfunction is determined during inspection, must be repaired or replaced at the
earliest possible date.
Components
Inspection
Intervals
Entire device
Cleaning
The entire device must be cleaned with a lint-free cloth at the end of the shift
Visual inspection
The entire device must be checked for damage daily. Damaged parts must be
replaced.
Hydraulic system Inspection
The hydraulic system must be checked for damage monthly. Damaged
components must be replaced.
Table 6: Maintenance plan
7.2
Change of hydraulic fluid
The hydraulic fluid must be replaced annually. Depending on usage and contamination, the hydraulic fluid may need to be replaced
at shorter intervals. Old hydraulic fluid must be disposed of properly. Refilling must be carried out via the the hydraulic unit. The
hydraulic unit is not contained in the scope of service of the machine. Old hydraulic fluid must be disposed of properly.