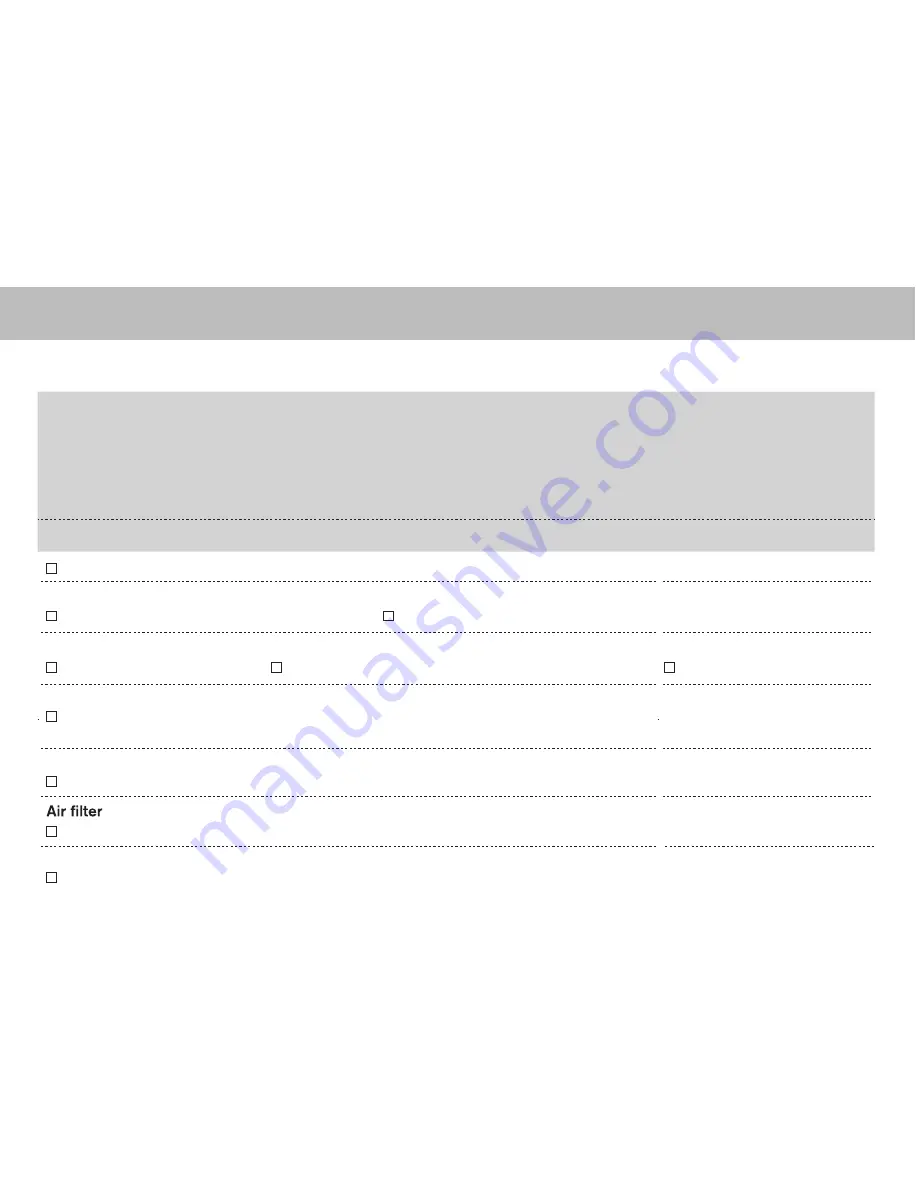
SAMPLE PRE-OPERATION CHECKLIST
Add to or adapt this checklist to suit your quad bike and place photocopies in a sturdy folder where vehicle keys and operator
PPE are stored.
•
Maintain completed forms to provide a record of completed inspection and/or training.
•
The operator’s manual provides information about minimum maintenance activity.
•
Additional copies of checklists are available at worksafe.vic.gov.au
Pre-operation checklist:
Check the fuel, oil and coolant every time before use with the engine off.
Visually inspect
Check for damaged or loose parts.
Check for
fuel or oil leaks.
Wheels and Tyres
Check tyres for damage.
Ensure tyre pressure is correct and even in each tyre.
Check wheel nuts.
Throttle
Check the throttle operates smoothly across its range. Accumulated mud and dirt can restrict cable movement and
prevent the throttle from closing.
Brakes
Check brakes operate properly before reaching full speed.
Check it is not choked with dirt. Clean and replace regularly.
Lights and switches
Check lights and switches work.
VEHICLE MAINTENANCE - BEFORE YOU RIDE CHECKLIST
Summary of Contents for HAMMER DUNE
Page 6: ...1 ...
Page 7: ...Turn off ...
Page 22: ......
Page 23: ......
Page 24: ......
Page 34: ...VEHICLE MAINTENANCE ...
Page 39: ...VEHICLE MAINTENANCE ...