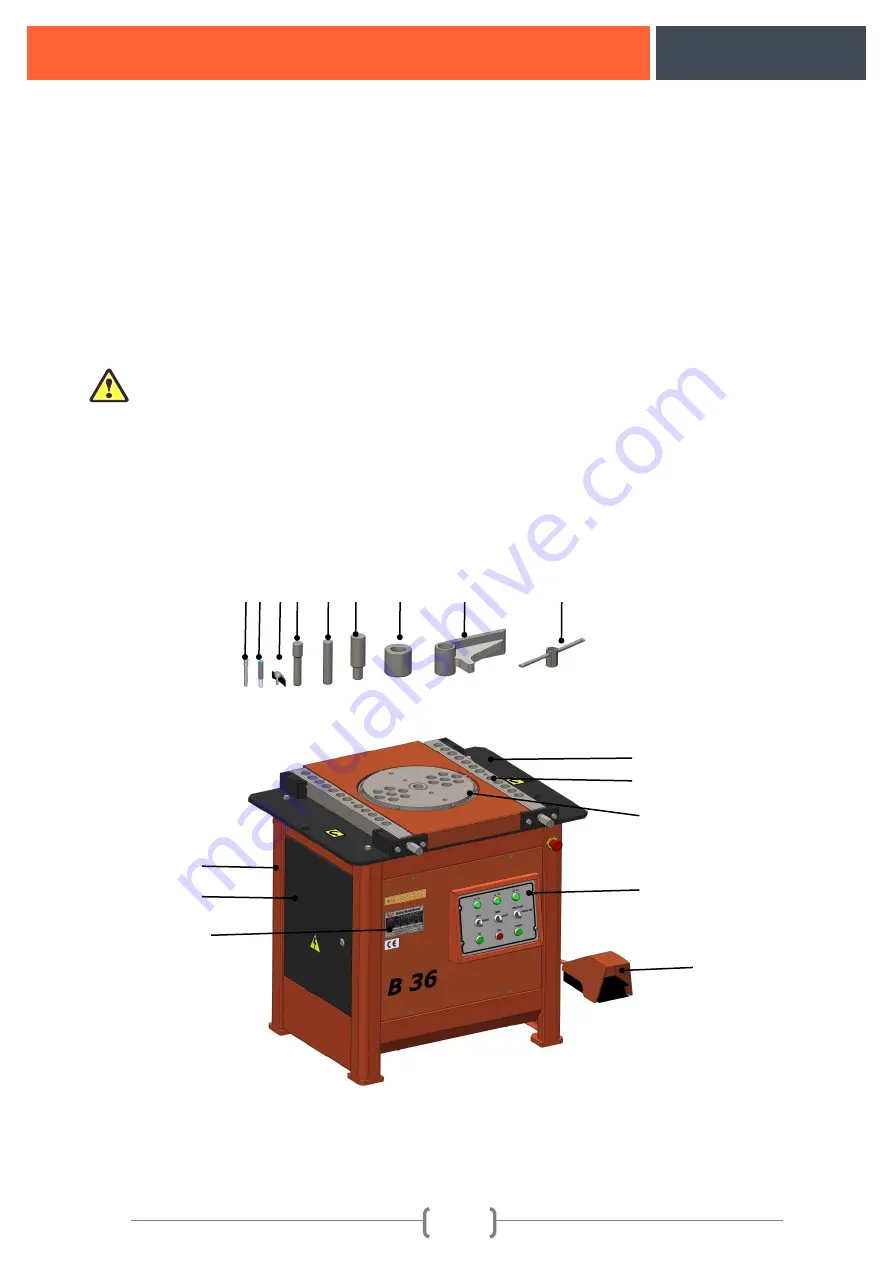
B36
4
INTRODUCTION
B 36 Mechanic Iron Bending Machine
is made only with the purpose of steel material bending.
Using other than the indicated purposes are prohibited. It is possible to mount various apparatuses on
the machine optionally for bending in different shapes.
In order to obtain the best yield from the machine it should be in a situation so that it can be worked
easily and in a position that more productivity might be obtained from the operator. Because of this the
location where the machine is operated should be close to the iron stocks. Besides, it shall be more
useful to cover top of the location where the machine is operated with a shelter. We suggest two
workbenches to be located on two sides of the machine. Length of these workbenches should be as
long as the longest iron that will be bent. Since the operator will be able to work without turning,
lifting any kind of iron, it will enable the operator to work more effectively.
Important Warning !!!
•
User's and maintenance manuals must be read.
•
Machine should be operated by instructed workers.
•
When adjustments such as controlling, maintaining, lubing are being made electricity of the
machine must be cut off.
•
All of the explanations given under user's and maintenance manual must be complied.
1.
MAIN PARTS OF BENDING MACHINE
Figure 1:
Main parts of bending machine
3 4 5 6
7 8
9
10
11
1
2
17
15
12
13
14
16