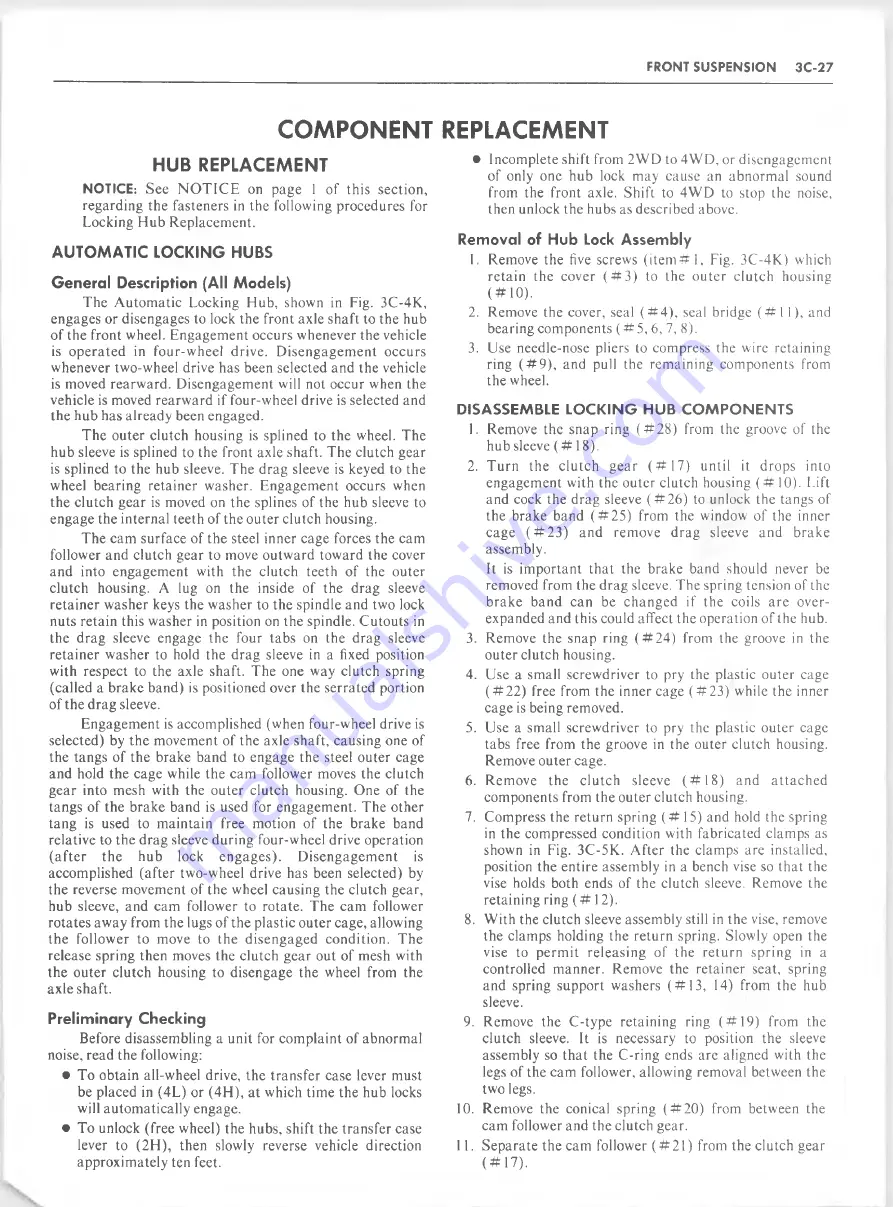
FRONT SUSPENSION
3 C -2 7
C O M P O N EN T REPLACEMENT
HUB REPLACEMENT
NOTICE:
See N O T I C E on page 1 of this section,
regarding the fasteners in the following procedures for
Locking Hub Replacement.
AUTOM ATIC LOCKING HUBS
General Description (All Models)
The Autom atic Locking Hub, shown in Fig. 3C-4K,
engages or disengages to lock the front axle shaft to the hub
of the front wheel. Engagement occurs whenever the vehicle
is o p erated in four-wheel drive. D isengagem ent occurs
whenever two-wheel drive has been selected and the vehicle
is moved rearward. Disengagement will not occur when the
vehicle is moved rearw ard if four-wheel drive is selected and
the hub has already been engaged.
The outer clutch housing is splined to the wheel. The
hub sleeve is splined to the front axle shaft. The clutch gear
is splined to the hub sleeve. The drag sleeve is keyed to the
wheel bearing retainer washer. Engagem ent occurs when
the clutch gear is moved on the splines of the hub sleeve to
engage the internal teeth of the outer clutch housing.
The cam surface of the steel inner cage forces the cam
follower and clutch gear to move outward toward the cover
and into engagement with the clutch teeth of the outer
clutch housing. A lug on the inside of the drag sleeve
retainer washer keys the washer to the spindle and two lock
nuts retain this washer in position on the spindle. Cutouts in
the drag sleeve engage the four tabs on the drag sleeve
retainer washer to hold the drag sleeve in a fixed position
with respect to the axle shaft. The one way clutch spring
(called a brake band) is positioned over the serrated portion
of the drag sleeve.
Engagem ent is accomplished (when four-wheel drive is
selected) by the movement of the axle shaft, causing one of
the tangs of the brake band to engage the steel outer cage
and hold the cage while the cam follower moves the clutch
gear into mesh with the outer clutch housing. One of the
tangs of the brake band is used for engagement. The other
tang is used to maintain free motion of the brake band
relative to the drag sleeve during four-wheel drive operation
( a fte r
th e
hub
lock
engages).
D isengagem ent
is
accomplished (after two-wheel drive has been selected) by
the reverse movement of the wheel causing the clutch gear,
hub sleeve, and cam follower to rotate. The cam follower
rotates away from the lugs of the plastic outer cage, allowing
th e follower to move to the d isengaged condition. The
release spring then moves the clutch gear out of mesh with
the outer clutch housing to disengage the wheel from the
axle shaft.
Preliminary Checking
Before disassembling a unit for complaint of abnormal
noise, read the following:
• To obtain all-wheel drive, the transfer case lever must
be placed in (4L) or (4H ), at which time the hub locks
will automatically engage.
• To unlock (free wheel) the hubs, shift the transfer case
lever to (2H ), then slowly reverse vehicle direction
approxim ately ten feet.
• Incomplete shift from 2W D to 4W D, or disengagement
of only one hub lock may cause an abnormal sound
from the front axle. Shift to 4W D to stop the noise,
then unlock the hubs as described above.
Removal of Hub Lock Assembly
1. Remove the five screws ( i t e m # l , Fig. 3C-4K) which
retain the cover ( # 3 ) to the outer clutch housing
( #
10
).
2. Remove the cover, seal ( # 4 ) , seal bridge ( # 1 1 ) , and
bearing components ( # 5 , 6, 7, 8).
3. Use needle-nose pliers to compress the wire retaining
ring ( # 9 ) , and pull the remaining components from
the wheel.
D IS A S S E M B L E L O C K IN G H U B C O M P O N E N T S
1. Remove the snap ring ( # 2 8 ) from the groove of the
hub sleeve ( # 1 8 ) .
2. T u rn the clutch g ear ( # 1 7 ) until it drops into
engagement with the outer clutch housing ( # 1 0 ) . Lift
and cock the drag sleeve ( # 2 6 ) to unlock the tangs of
the brake band ( # 2 5 ) from the window of the inner
cage ( # 2 3 ) and remove drag sleeve and brake
assembly.
It is im portant that the brake band should never be
removed from the drag sleeve. The spring tension of the
brake band can be changed if the coils are over-
expanded and this could affect the operation of the hub.
3. Remove the snap ring ( # 2 4 ) from the groove in the
outer clutch housing.
4. Use a small screwdriver to pry the plastic outer cage
( # 2 2 ) free from the inner cage ( # 2 3 ) while the inner
cage is being removed.
5. Use a small screwdriver to pry the plastic outer cage
tabs free from the groove in the outer clutch housing.
Remove outer cage.
6. Remove the clutch sleeve ( # 1 8 ) and a tta c h e d
components from the outer clutch housing.
7. Compress the return spring ( # 1 5 ) and hold the spring
in the compressed condition with fabricated clamps as
shown in Fig. 3C-5K. After the clamps are installed,
position the entire assembly in a bench vise so th at the
vise holds both ends of the clutch sleeve. Remove the
retaining ring ( # 1 2 ) .
8. With the clutch sleeve assembly still in the vise, remove
the clamps holding the return spring. Slowly open the
vise to perm it releasing of the retu rn spring in a
controlled manner. Remove the retainer seat, spring
and spring support washers ( # 1 3 , 14) from the hub
sleeve.
9. Remove the C-type retaining ring ( # 1 9 ) from the
clutch sleeve. It is necessary to position the sleeve
assembly so that the C-ring ends are aligned with the
legs of the cam follower, allowing removal between the
two legs.
10. Remove the conical spring ( # 2 0 ) from between the
cam follower and the clutch gear.
11. Separate the cam follower ( # 2 1 ) from the clutch gear
( # 1 7 ) .
Summary of Contents for 1982 Light Duty Truck
Page 1: ......
Page 28: ...HEATER 1A 3 Fig lA 2 Heater Control C K Models Fig lA 3 Heater Control G Models...
Page 37: ...Fig 1A 11 T E E V A L V E A S M TEE AND VALVE C36...
Page 38: ...HEATER 1A 13 Fig 1A l2 Distributor Ducts G Models Fig 1A l5 Control Assembly G Models...
Page 39: ...1A 14 HEATER V IE W A V IE W B Fig 1A l7 Control Cable Routing G Models...
Page 42: ...HEATER 1A 19 Fig 1A 23 Auxiliary Heater Hose Routing...
Page 56: ...AIR CONDITIONING IB 13 Chart 1B 4 Pressure Cycling CCOT System Diagnosis...
Page 64: ...Fig 1B 17 C60 System Vacuum Diagram C K Series...
Page 65: ......
Page 66: ...Fig 1B 19 C60 Motor Home Chassis Wiring Diagram SWITCH AIR CONDITIONING IB 2 3...
Page 67: ...IB 24 AIR CONDITIONING Fig IB 20 1 P A C Harness Wiring...
Page 68: ...AIR CONDITIONING IB 25 VIE W A Fig IB 21 A C Compressor wiring...
Page 76: ...AIR CONDITIONING IB 33 Fig 1B 26 Compressor Mounting...
Page 91: ...IB 48 AIR CONDITIONING Fig 1B 59 C K Models Refrigerant Lines L6...
Page 150: ......
Page 162: ......
Page 164: ...2D 2 BODY Fig 2D 4 Typical Utility Vehicle Model...
Page 182: ...2D 20 BODY Fig 2D 51 Rear Door Controls Fig 2D 52 Rear Door Outside Handle and Lock Cylinder...
Page 193: ...BODY 2D 31 BELTS 3RD SEAT Fig 2D 82 Seat Belt Installation Suburban Driver Seat Suburban...
Page 194: ...2D 32 BODY Fig 2D 85 Passenger s Bucket Seat Chassis Cab...
Page 195: ...BODY 2D 33 Fig 2D 88 Rear Bench Seats Suburban...
Page 196: ...2D 34 BODY Fig 2D 89 CK Utility Seat Attachments...
Page 197: ...BODY 2D 35 Fig 2D 90 Seat Separator Compartment and Door CK Models...
Page 222: ......
Page 223: ...BODY 2D 61 Fig 2D 139 Front Seat Belt Installation...
Page 228: ......
Page 234: ......
Page 252: ...3B2 8 MANUAL STEERING GEAR Fig 3B2 11 Manual Steering Gear Exploded View...
Page 256: ......
Page 273: ...POWER STEERING SYSTEM 3B3 17 with LE3 Engine Exc HC4 LE4 LG9 LF4 LS9 LT9 and JB7 HC4 and JB8...
Page 342: ......
Page 389: ...REAR SUSPENSION 3D 7 Fig 3D 17 Rear Spring Installation C K Models...
Page 428: ...4 B 1 4 REAR AXLE Fig 4B 8 Gear Tooth Nomenclature Fig 4B 9 G ear Tooth Contact Pattern Check...
Page 444: ......
Page 454: ......
Page 468: ...4 B 5 2 REAR AXLE Fig 4B5 2 Rockwell Assembly...
Page 480: ...4 B 5 1 4 REAR AXLE...
Page 482: ...i...
Page 502: ......
Page 520: ......
Page 533: ...Fig 5 5 Front Brake Pipes and Hoses C K Models BRAKES 5 13...
Page 534: ...Fig 5 6 Front Brake Pipes and Hoses G M odels 5 14 B R A K E S...
Page 535: ...Fig 5 7 Front Brake Pipes and Hoses P Models BRAKES 5 15...
Page 536: ...5 16 BRAKES Fig 5 8 Rear Brake Hoses...
Page 538: ...5 18 BRAKES Fig 5 10 Parking Brake System Typical...
Page 539: ...BRAKES 5 19...
Page 570: ...5 50 BRAKES Fig 5 57 Power Steering Hose Routing C K Models...
Page 571: ...BRAKES 5 51 Fig 5 58 Power Steering Hose Routing G Models...
Page 572: ...Fig 5 59 Power Steering H ose Routing P Models 5 52 BRAKES...
Page 577: ...BRAKES 5 57 4 CONT A SECONDARY DIAPHRAGM B SECONDARY POWER 4 CONT C PRIMARY D Fig 5 5A Service...
Page 604: ......
Page 625: ...NOTES ENGINE 6 21...
Page 626: ......
Page 629: ...IN LINE 6 6A1 3 OIL PRESSURE SENDING UNIT Fig 6A1 1 In Line Engine Lubrication...
Page 630: ...6A1 4 IN LINE 6 Fig 6 A l 2 P Series Engine Front Mount...
Page 631: ...IN LINE 6 6A1 5 Fig 6Al 3 P Series Engine Rear Mount Fig 6 A l 4 C Series Engine Rear Mounts...
Page 634: ...6A1 8 IN LINE 6 Fig 6Al 7 K Series Engine Rear Mount...
Page 660: ......
Page 663: ...SMALL BLOCK 6A4 3 Fig 6A4 T Engine Lubrication...
Page 664: ...6A4 4 SMALL BLOCK Fig 6A4 2 Engine Lubrication...
Page 665: ...Fig 6A4 3 P Series Engine Mount Bracket...
Page 667: ...SMALL BLOCK 6A4 7 Fig 6A 4 5 P Series Engine Front Mount...
Page 668: ...6A4 8 SMALL BLOCK...
Page 669: ...SMALL BLOCK 6A4 9 Fig 6A 4 7 K Series Engine Mounts...
Page 670: ...6A4 10 SMALL BLOCK Fig 6A 4 8 C Series Engine Mounts...
Page 703: ...MARK IV 6A5 7 Fig 6A 5 6 P Series Engine Front Mount...
Page 704: ...6A5 8 MARK IV Fig 6 A 5 7 C Series Engine Mounts...
Page 731: ...6 2 DIESEL 6A7 3...
Page 760: ...6B 6 ENGINE COOLING Fig 6B 7 A C and A I R Adjustment...
Page 771: ...ENGINE COOLING 6B 17 Fig 6B 20 Engine O il C o o le r 6 2L Diesel...
Page 784: ......
Page 807: ...CARBURETOR MODEL 2SE 6C2 9 Fig 6C2 6 Typical 2SE Carburetor Assembly...
Page 820: ......
Page 830: ...6C4 10 CARBURETOR MODEL M4ME M4MC 101368 Fig 6C4 12 M 4M C M 4M E Carburetor Exploded View...
Page 848: ......
Page 876: ......
Page 888: ...6D 12 ENGINE ELECTRICAL Fig 6D 6C Generator Mounting Fig 6D 7C Generator Mounting...
Page 919: ...ENGINE ELECTRICAL 6D 43...
Page 934: ...Fig 6D 8E Starter M otor Mounting...
Page 974: ......
Page 1011: ...Figure 350C 25A Neutral Engine Running AUTOMATIC TRANSMISSION 350C 11...
Page 1054: ...Fig 7A 1C 400 Autom atic Transmission Side Cross Section Typical...
Page 1152: ...700 R4 40 AUTOMATIC TRANSMISSION Figure 700 R4 76 Transmission Assembly Exploded View...
Page 1162: ......
Page 1189: ...89MM MANUAL TRANSMISSION 7B3 5 Fig 7 3 4 4 Speed 89mm Exploded View...
Page 1219: ...CLUTCH 7C 5 Fig 7C 6 C K Truck Clutch Controls...
Page 1220: ...Fig 7C 7 G Truck Clutch Controls...
Page 1221: ...CLUTCH 7C 7 Fig 7C 8 P Truck Clutch Controls...
Page 1234: ...7E 2 TRANSFER CASE Fig 7E 1 Model 208 Transfer Case Cross Section...
Page 1252: ...7E 20 TRANSFER CASE Fig 7E 39 Transfer Case Attachment Typical...
Page 1278: ...8A 16 ELECTRICAL BODY AND CHASSIS Fig 8A 11 License Plate Lamps C K Series...
Page 1280: ...8A 18 ELECTRICAL BODY AND CHASSIS VIEW A VIEW B Fig 8A 15 CK Series Rear Lamp W iring...
Page 1281: ...ELECTRICAL BODY AND CHASSIS 8A 19 Fig 8A 16 CK Series Auxiliary W iring...
Page 1290: ...8B 8 ELECTRICAL AND WIRING Fig 8B 13 Seat Belt Reminder System Schematic...
Page 1292: ......
Page 1346: ...8C 54 INSTRUMENT PANEL AND GAGES Fig 8C 46 CK Series W iring 3 of 29...
Page 1351: ...INSTRUMENT PANEL AND GAGES 8C 59 SUBURBAN Fig 8C 51 CK Series W iring 8 of 29...
Page 1364: ...8C 72 INSTRUMENT PANEL AND GAGES Fig 8C 64 CK Series W iring 21 of 29...
Page 1365: ...INSTRUMENT PANEL AND GAGES 8C 73 CAB CRFW CAB CHASSIS Fig 8C 65 CK Series W iring 22 of 29...
Page 1366: ...8C 74 INSTRUMENT PANEL AND GAGES Fig 8C 66 CK Series W iring 23 of 29...
Page 1374: ...8C 82 INSTRUMENT PANEL AND GAGES Fig 8C 74 G Series W iring 2 of 19...
Page 1375: ...INSTRUMENT PANEL AND GAGES 8C 83 Fig 8C 75 G Series W iring 3 of 19...
Page 1376: ...8C 84 INSTRUMENT PANEL AND GAGES Fig 8C 76 G Series W iring 4 of 19...
Page 1379: ...INSTRUMENT PANEL AND GAGES 8C 87 Fig 8C 79 G Series W iring 7 of 19...
Page 1383: ...INSTRUMENT PANEL AND GAGES 8C 91 Fig 8C 83 G Series W iring 11 o f 19...
Page 1384: ...8C 92 INSTRUMENT PANEL AND GAGES BUS BARGWO Fig 8C 84 G Series W iring 12 of 19...
Page 1390: ...8C 98 INSTRUMENT PANEL AND GAGES Fig 8C 90 G Series W iring 18 of 19...
Page 1391: ...INSTRUMENT PANEL AND GAGES 8C 99 Fig 8C 91 G Series W iring 19 of 19...
Page 1392: ...8C 100 INSTRUMENT PANEL AND GAGES Fig 8C 92 P Series W iring 1 of 11...
Page 1393: ...INSTRUMENT PANEL AND GAGES 8C 101 Fig 8C 93 P Series W iring 2 of 11...
Page 1396: ...8C 104 INSTRUMENT PANEL AND GAGES Fig 8C 96 P Series W iring 5 of 11...
Page 1399: ...INSTRUMENT PANEL AND GAGES 8C 107 Fig 8C 99 P Series W iring 8 of 11...
Page 1401: ...INSTRUMENT PANEL AND GAGES 8C 109 START RUN OF LOCK ACC Fig 8C 101 P Series W iring 10 of 11...
Page 1415: ...ACCESSORIES 9 13 RADIO NOISE BLOWER MOTOR Fig 9 6R Radio Diagnosis Chart B...
Page 1416: ...9 14 ACCESSORIES D E A D R A D IO A M R A D IO I Fig 9 7R Radio Diagnosis Chart C...
Page 1417: ...ACCESSORIES 9 15 DEAD RADIO AM FM RADIO Fig 9 8R Radio Diagnosis Chart D...
Page 1435: ...t f l i t 1...