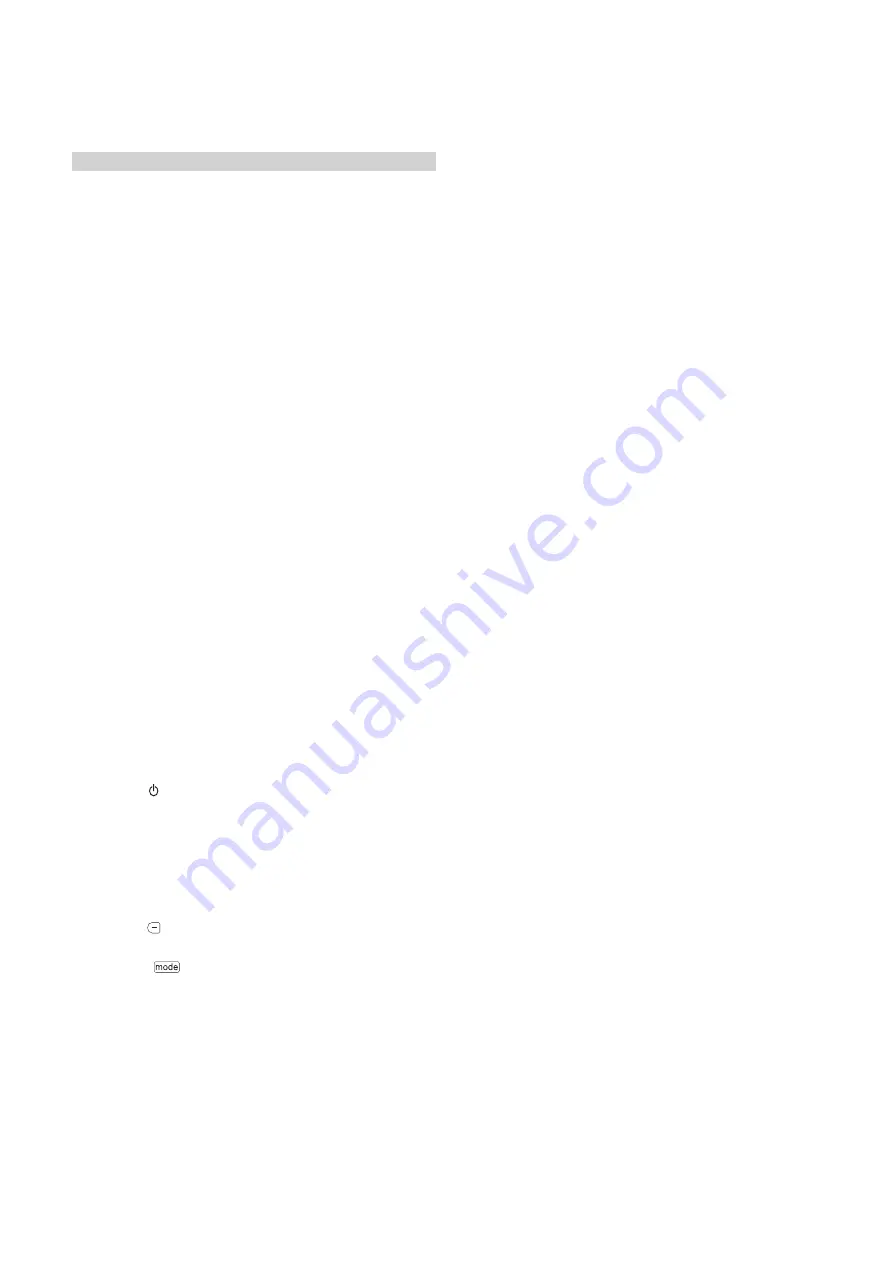
0020238426_04 EASICOM 3 Installation and maintenance instructions
33
12.14 Checking the pre-charge pressure of the
expansion vessel
1.
Drain the product. (
2.
Measure the pre-charge pressure of the expansion ves-
sel at the vessel valve.
Condition
: Pre-charge pressure < 0.075 MPa (0.75 bar)
▶
Top up the expansion vessel in accordance with the
static height of the heating installation, ideally with ni-
trogen, otherwise with air. Check that the drain valve is
open when topping up.
3.
If water escapes from the valve of the expansion
vessel, you must replace the expansion vessel
(
4.
Fill and purge the heating installation. (
12.15 Completing inspection and maintenance
work
1.
Fill and purge the heating installation. (
2.
Check the gas connection pressure (gas flow pressure).
(
3.
Check the CO
₂
content. (
4.
If required, set the maintenance interval.
5.
Check the product for tightness. (
6.
Install the front casing. (
7.
Fill out the relevant Service Record section in the
Benchmark Checklist located at the rear of this
document.
13 Troubleshooting
13.1
Rectifying faults
▶
If fault codes (F.
XX
) are present, refer to the table in the
appendix for advice or use the check programme(s).
Overview of fault codes (
Check programmes
–
Overview (
If several faults occur at the same time, the fault codes are
shown alternately on the display.
▶
Hold the
button down for more than 3 seconds.
▶
If you are unable to clear the fault code and it reappears
despite several fault clearance attempts, contact cus-
tomer service.
13.2
Calling up the fault memory
The last ten fault codes are stored in the fault memory.
▶
Hold the
button down for more than 7 seconds.
Overview of fault codes (
▶
Press the
button to exit this menu.
13.3
Deleting the fault memory
1.
Delete the fault memory using the diagnostics code
d.94
.
2.
Set diagnostics code . (
Overview of diagnostics codes (
13.4
Resetting parameters to factory settings
1.
Reset all parameters to the factory settings using the
diagnostics code
d.96
.
2.
Set diagnostics code . (
Overview of diagnostics codes (
13.5
Preparing the repair work
1.
Decommission the product.
2.
Disconnect the product from the power grid.
3.
Remove the front casing.
4.
Close the gas stopcock.
5.
Close the service valves in the heating flow and in the
heating return.
6.
Close the service valve in the cold water pipe.
7.
Drain the product if you want to replace water-bearing
components of the product.
8.
Ensure that water does not drip on live components
(e.g. the electronics box).
9.
Use only new seals and O-rings. Do not use any addi-
tional components.
13.5.1 Procuring spare parts
The original components of the product were also certified
by the manufacturer as part of the declaration of conformity.
If you use other, non-certified or unauthorised parts during
maintenance or repair work, this may void the conformity of
the product and it will therefore no longer comply with the
applicable standards.
We strongly recommend that you use original spare parts
from the manufacturer as this guarantees fault-free and safe
operation of the product. To receive information about the
available original spare parts, contact the contact address
provided on the back page of these instructions.
▶
If you require spare parts for maintenance or repair
work, use only the spare parts that are permitted for the
product.
13.6
Replacing defective components
13.6.1 Replacing the burner
1.
Remove the gas-air mixture unit. (
2.
Remove the burner seal.
3.
Remove the burner.
4.
Install the new burner complete with new burner seal on
the heat exchanger.
5.
Install the gas-air mixture unit. (
13.6.2 Replacing the gas-air mixture unit
1.
Remove the gas-air mixture unit. (
2.
Install the new gas-air mixture unit (