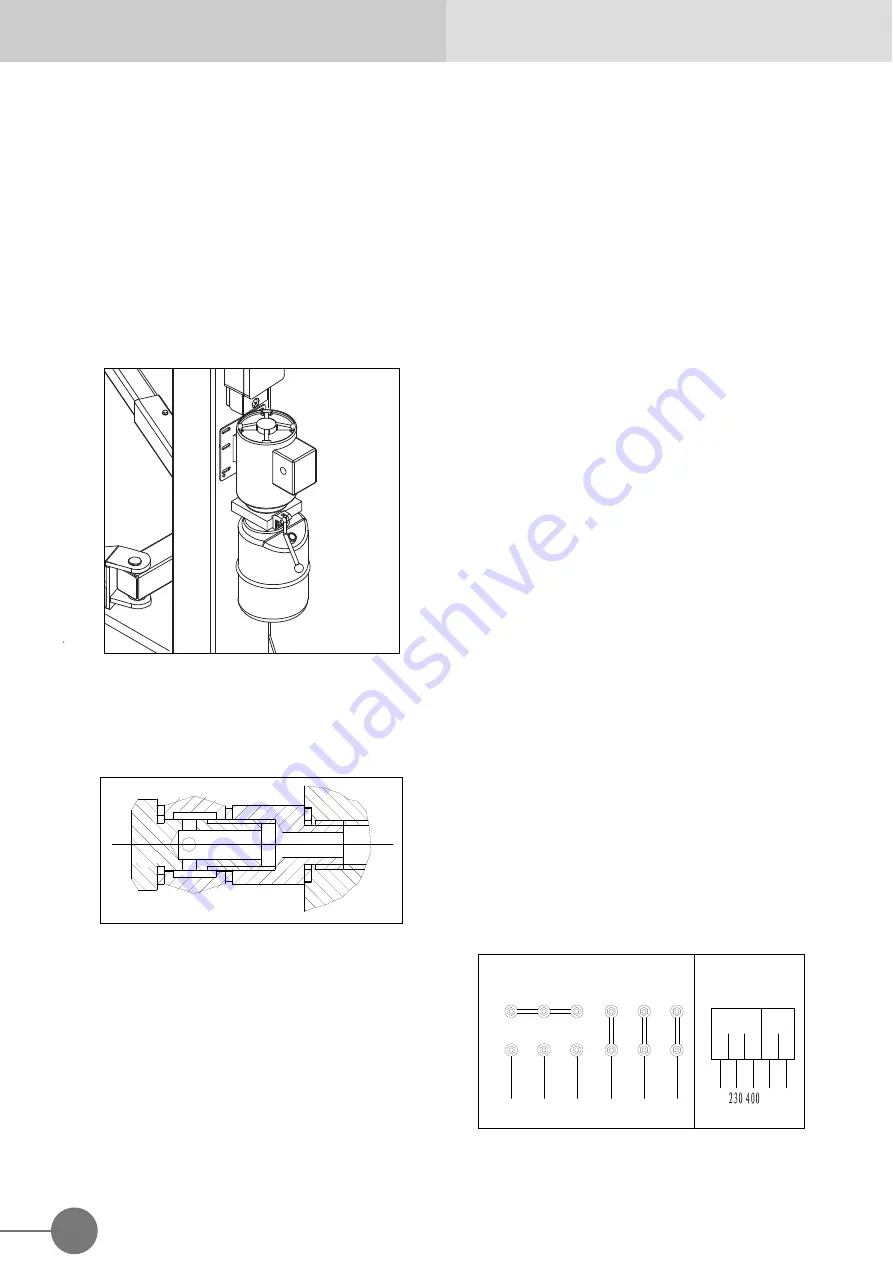
14
Installation/Operation & Maintenance Manual
GM
-
6140H 2-POST LIFT
◆
Install the safety devices.
◆
Adjust both cables and keep the carriage in
balance.
◆
Screw the joint of the high-pressure hose and
fix it on the base.
4.4.2 HYDRAULIC PALNT
◆
Install the pump on the hock board according to
Fig. 34
and fix it on the bottom of main column.
Fig. 34
◆
Connect the hydraulic unit to the circuit crossing
with a flexible pipe.
(Fig. 35)
Fig. 35
◆
Tight all the fittings very well, even the one
already mounted by the manufacturer.
◆
Fill the hydraulic unit tank with 8 liters of
hydraulic oil ISO 32 as IP HYDRUS OIL 32,
SHELL TELLUS OIL T32 or similar
(See
Chapter 2, TECHNICAL SPECIFICATIONS)
.
◆
Remove the oil filling cap and substitute it with
the given drain cap.
4.4.3 ELECTRIC PLANT CONNECTION
WARNING
The operations listed below must be performed
by skilled personnel.
4.4.3.1
Before connecting the electric system, make
sure that:
◆
The power supply plant to the lift is equipped
with the protection device required by current
standards in the country where the machinery is
installed.
◆
The power supply line has the following cross-
section:
Lift voltage 400V, three-
phase………….……Min.
2.5mm
2
Lift voltage 230V, three-
phase…………………Min.
4mm
2
Lift voltage 230V, single-
phase……………..…Min.
6mm
2
◆
The voltage oscillations are within the tolerance
range set forth by the specifications.
The manufacturer supplies the rack to operate at
400V with a three-phase configuration; if the line
voltage is different, the motor and transformer
connection must be changed.
(Fig. 36)
It is also
necessary to replace the thermal relay requesting
that part from the manufacture and/or service
center.
Fig. 36
W2
U2
V2
W1
V1
U1
L1
L2
L3
U2
W2
V2
W1
V1
U1
L3
L2
L1
Motor
0
0 24
Trasformer
Summary of Contents for GM - 6140H
Page 27: ......