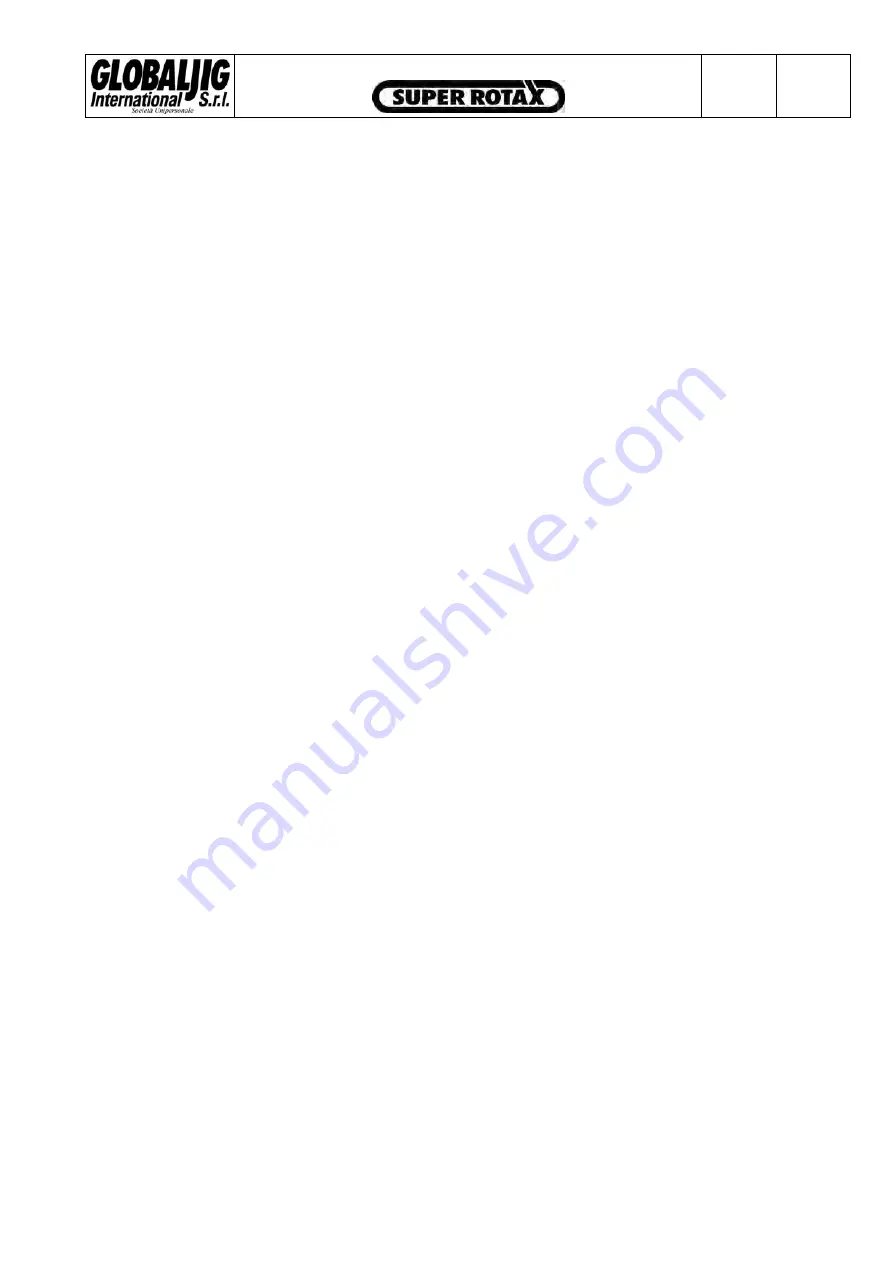
INSTRUCTION MANUAL
Issue.
08 / 2004
Pag.
1 - 42
CHAPTERS :
1.
INTRODUCTION
2.
GENERAL SAFETY RULES
3.
CHARACTERISTICS AND TECHNICAL DATA
4.
FREIGHT AND UNPACKING
5.
INSTALLATION
6.
COMMISSIONING
7.
CONTROLS AND SET UP
8.
OPERATING
9.
SAFETY DEVICE
10.
WORKING AREA
11.
START/ STOP/ EMERGENCY
12.
MAINTENANCE
13.
REPAIR / COMPONENTS AND SPARE PARTS
14.
DIAGRAMS AND OVERALL DIMENSIONS
15.
DEMOLITION
APPEDIX: CE CONFORMITY DECLARATION
Summary of Contents for Super Rotax
Page 2: ...USERS MANUAL Year of Manufacture ...
Page 21: ...INSTRUCTION MANUAL Issue 08 2004 Pag 19 42 7 1 1 ELECTRICAL PLANT DIAGRAM ...
Page 22: ...INSTRUCTION MANUAL Issue 08 2004 Pag 20 42 7 1 2 HYDRAULIC PLANT DIAGRAM ...
Page 23: ...INSTRUCTION MANUAL Issue 08 2004 Pag 21 42 7 1 3 PNEUMATIC PLANT DIAGRAM ...
Page 42: ...INSTRUCTION MANUAL Issue 08 2004 Pag 40 42 14 OVERALL DIMENSIONS DRAWING ...