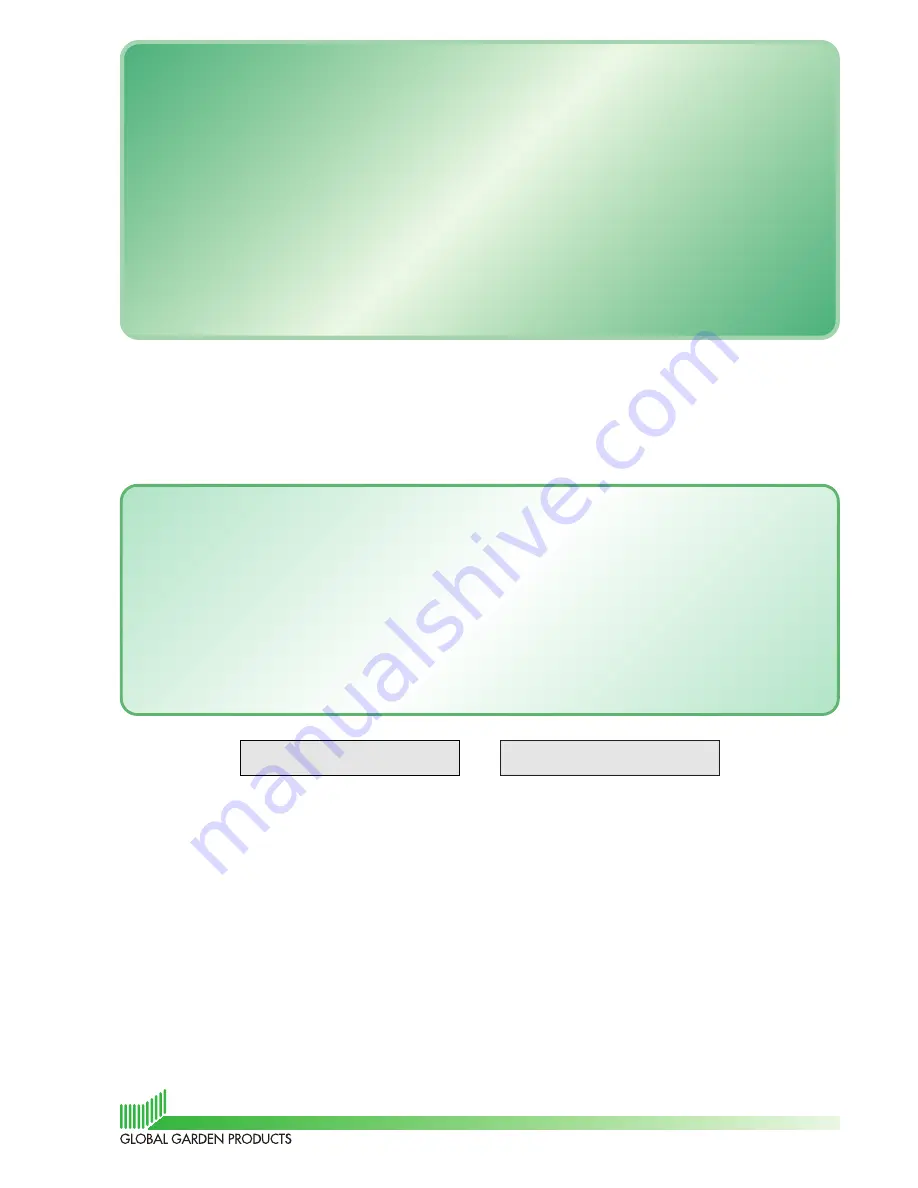
The Manufacture reserves the right to make any improvements to the product of a technical or commercial
nature that may be necessary. There may be, therefore, differences between the various series of machines
and that described here, though the basic features and various repair methods will remain the same.
© by GLOBAL GARDEN PRODUCTS - No use of the illustrations or duplication, reproduction or translation,
even partial, of the texts in this document may be made without explicit authorization.
WORKSHOP
MANUAL
Rel. 7.0
YEAR OF MANUFACTURE
2006
9
9
9
9
2
2
2
2
9
9
9
9
2
2
2
2
h
h
h
h
y
y
y
y
d
d
d
d
r
r
r
r
o
o
o
o