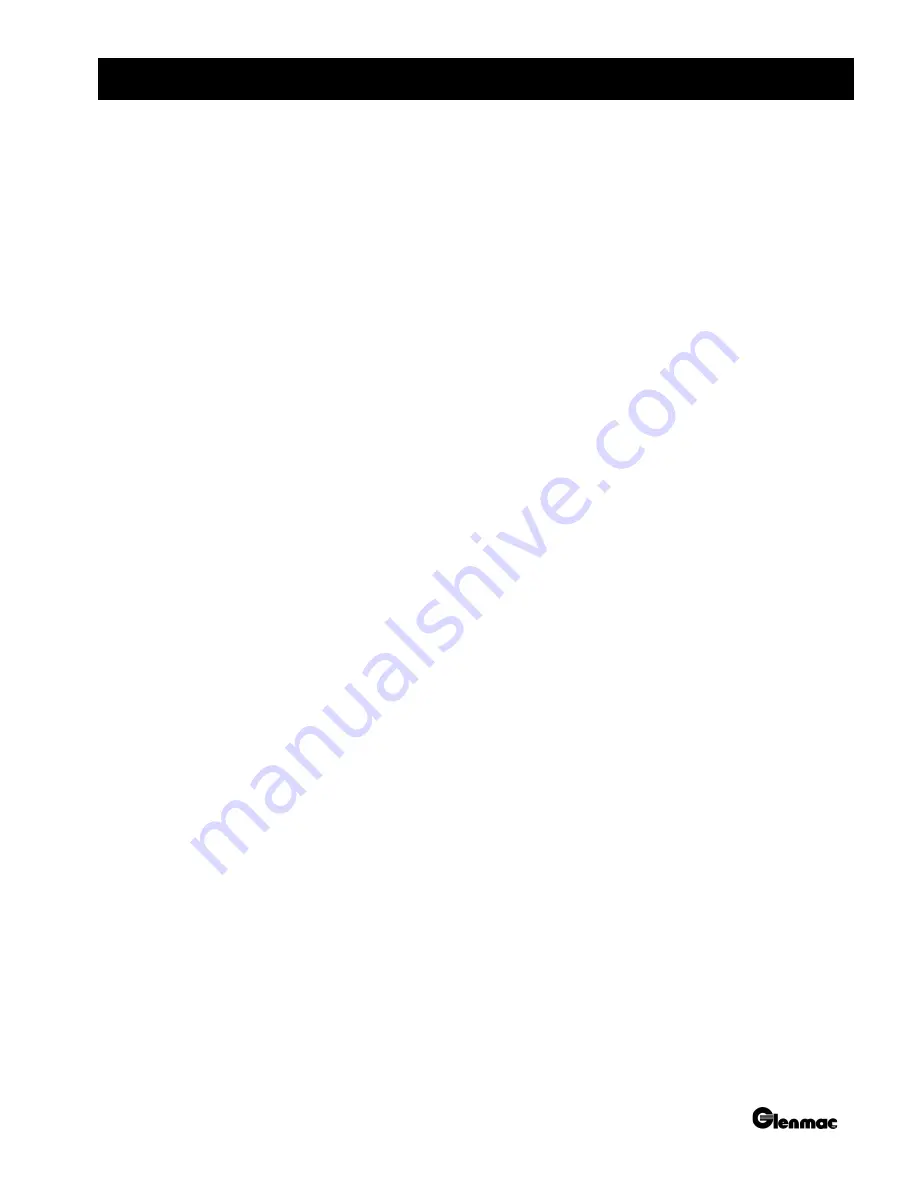
13
PN-P970620 (03/2005)
IMPORTANT
•
If the PTO is too long, severe PTO and gearbox
damage is possible when hooking up the PTO
from the power rake to the tractor. The front
PTO is long enough to fit a variety of tractors.
It is possible that the front PTO will need to
be cut. There will be NO benefit by cutting
only one telescoping section. Both sections of
the PTO must be cut. DO NOT FORCE THE
PTO TO FIT.
•
WARRANTY IS VOID IF THE PTO IS
TOO LONG, resulting in gearbox, PTO, yoke,
or cross bearing damage.
The PTO, when attached to the tractor and gearbox,
must not extend so there is less than five inches of
overlap within the PTO.
Attach the two hydraulic lines on the rake to the two
female hydraulic couplers on the tractor. The hydraulic
hose ends on the power rake are ISO male couplers,
which are compatible with newer tractors.
Raise jackstand and secure in operating position.
IMPORTANT
••
Always clean connector ends prior to attaching.
Dirt could contaminate hydraulic fluid and
damage the hydraulic system.
POWER RAKE FUNCTION
The tractor PTO drives the two rollers. The lower
roller digs in the ground pulling up rocks and debris.
The clean soil goes between the rollers and the rock,
and the debris works to the side in a windrow. The
scarifier also brings up debris from below the ground
and loosens the soil so the rollers can function more
efficiently.
Maximum safe PTO operating speed is 540 RPM.
PRE-OPERATION CHECK LIST
___ Review and follow all safety rules and safety decal
instructions on pages 6 through 11.
___ Check that all safety decals are installed and in
good condition. Replace if damaged.
___ Check that all shields and guards are properly
installed and in good condition. Replace if
damaged.
___ Check that all hardware and cotter pins are
properly installed and secured.
___ Check that equipment is properly and securely
attached to tractor.
___ Make sure driveline spring-activated locking pin
or collar slides freely and is seated firmly in
tractor PTO spline groove.
___ Before starting tractor, check all equipment
driving guards for damage and make sure they
rotate freely on all drivelines. Replace any
damaged guards. If guards do not rotate
freely
on drivelines, repair and replace bearings before
operating.
___ Do not allow riders.
___ Check for and keep all bystanders away from
equipment working area.
___ Make sure gearbox is filled to the correct level
with high quality 80W-90 gear oil.
___ Check all lubrication points and grease as
instructed in “Maintenance, Lubrication”
information.
___ Check that all hydraulic hoses and fittings are
in good condition and not leaking before starting
tractor. Check that hoses are not twisted, bent
sharply, kinked, frayed, or pulled tight. Replace
any damaged hoses immediately.
___ Make sure tractor ROPS or ROPS CAB and seat
belt are in good condition. Keep seat belt
securely fastened during operation.
___ Check tire pressure and service if necessary.
OPERATION
Summary of Contents for Harley Pro 6
Page 1: ......
Page 21: ...19 PN P970620 03 2005 Figure 3 LUBRICATION MAINTENANCE ...
Page 23: ...21 PN P970620 03 2005 NOTES ...
Page 30: ...28 PN P970620 03 2005 ROLLER ASSEMBLY ...
Page 31: ...29 PN P970620 03 2005 ROLLER ASSEMBLY ...
Page 33: ...31 PN P970620 03 2005 NOTES ...
Page 34: ...32 PN P970620 03 2005 Figure 8L FINAL ASSEMBLY ...
Page 35: ...33 PN P970620 03 2005 FINAL ASSEMBLY Figure 8R ...