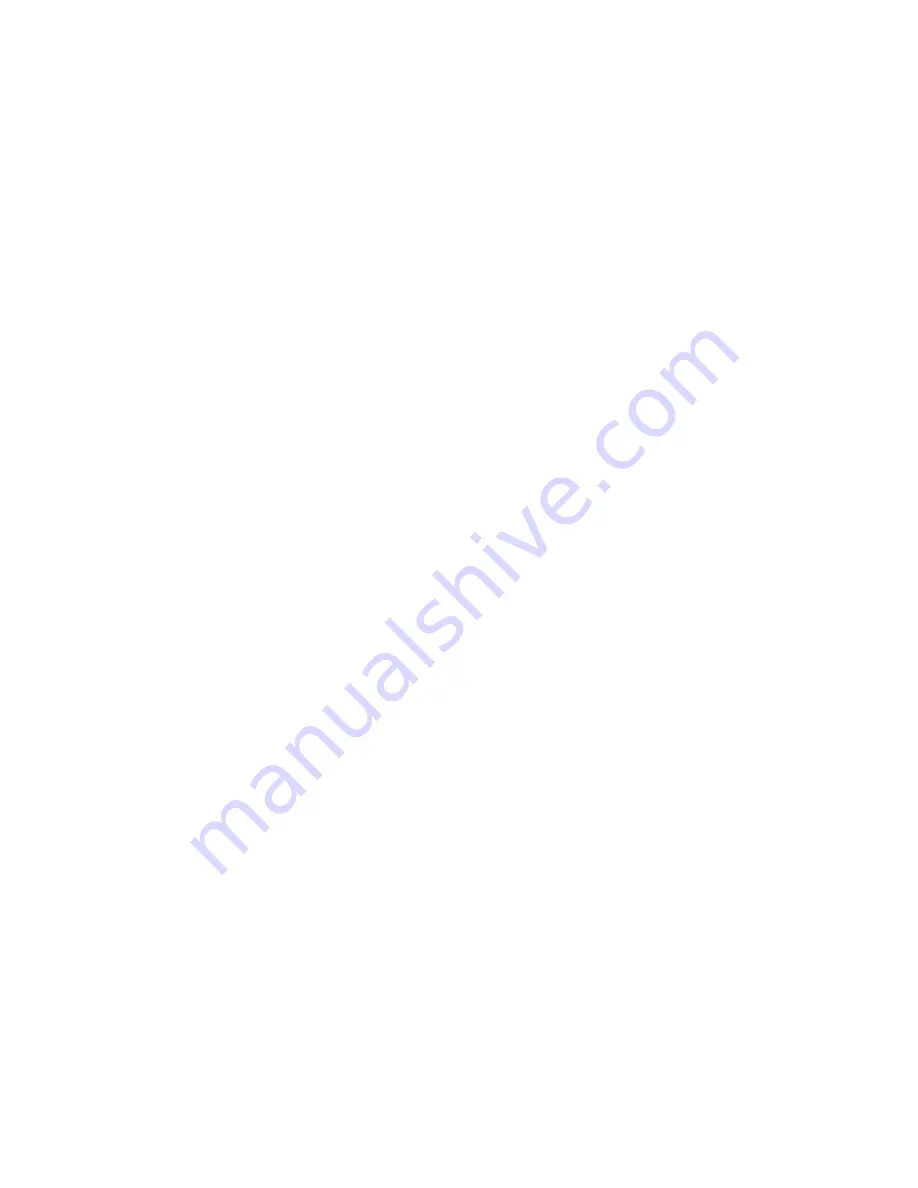
- 9 -
Position yourself to where you can read the
air pressure. Press the torch switch (air will
exhaust from torch, adjust the air regulator
to read approximately 60 to 70 pounds (PSI)
and release torch switch.
Note: The Air pressure has a generally
acceptable range of 50 to 80 PSI. You may
experiment as desired… but be careful not
to lower the pressure too much as
consumable damage will occur.
Secure ground clamp to workpiece.
Connect clamp to main part of workpiece,
not the part being removed.
B. Cutting
1. Drag Cutting
Position torch tip slightly above workpiece,
press torch switch and lower torch tip
toward workpiece until contact is made and
cutting arc is established. After cutting arc
is established, move the torch in the
desired direction keeping the torch tip
slightly angled, maintaining contact with the
workpiece.
This methodology is called Drag-Cutting.
Avoid moving too fast as would be
indicated by sparks radiating from the top
side of workpiece. Move the torch just fast
enough to maintain sparks concentration at
the underside of the work-piece and
making sure the material is completely cut
through before moving on. Adjust drag
speed as desired/required.
3. Stand-off Cutting
In some cases, it may be beneficial to cut
with the torch tip raised above the work-
piece approximately 1/16" to 1/8” to reduce
material blow-back into the tip and to
maximize penetration of thick material cuts.
An example of "stand-off cutting" would be
used when penetration cutting or gouging
operation is being performed. You can also
use “stand-off” technique when cutting
sheet metal to reduce the chance of
splatter-back tip damage.
4. Piercing
For
piercing,
position
the
tip
approximately 1/8" (3.2 mm) above the
workpiece. Angle the torch slightly to
direct sparks away from the torch tip and
operator.
Initiate the pilot arc and lower the tip of the
torch until the main cutting arc transfers,
sparks start.
Start the pierce off the cutting line on the
scrap piece or template and then continue
the cut onto the cutting line.
Hold the torch perpendicular to the
workpiece after the pierce is complete
and continue cutting as desired.
Clean spatter and scale from the shield
cup and the tip as soon as possible.
5. Quality Cuts
Dross (slag) is the excess material that
spatters and builds up on the underside of
the work-piece as you cut.
Dross occurs when the operating
procedure and technique is less than
optimal. It will require practice and
experience to obtain cuts without dross.
Although less than optimal cuts will
contain dross, it is relatively easy to
remove by breaking it off using pliers or
chipping off with a chisel or scraping or
grinding the finished cut as needed and is
generally only a minor inconvenience.
A combination of factors contribute to the
buildup of dross. They include... material
type, material thickness, amperage used
for the cut, speed of the torch across the
work-piece, condition of the torch tip, input
line voltage, air pressure, etc. Generally
there is an inversely proportional
relationship between output current and
speed of cut. Do not use more output
current than is necessary and adjust