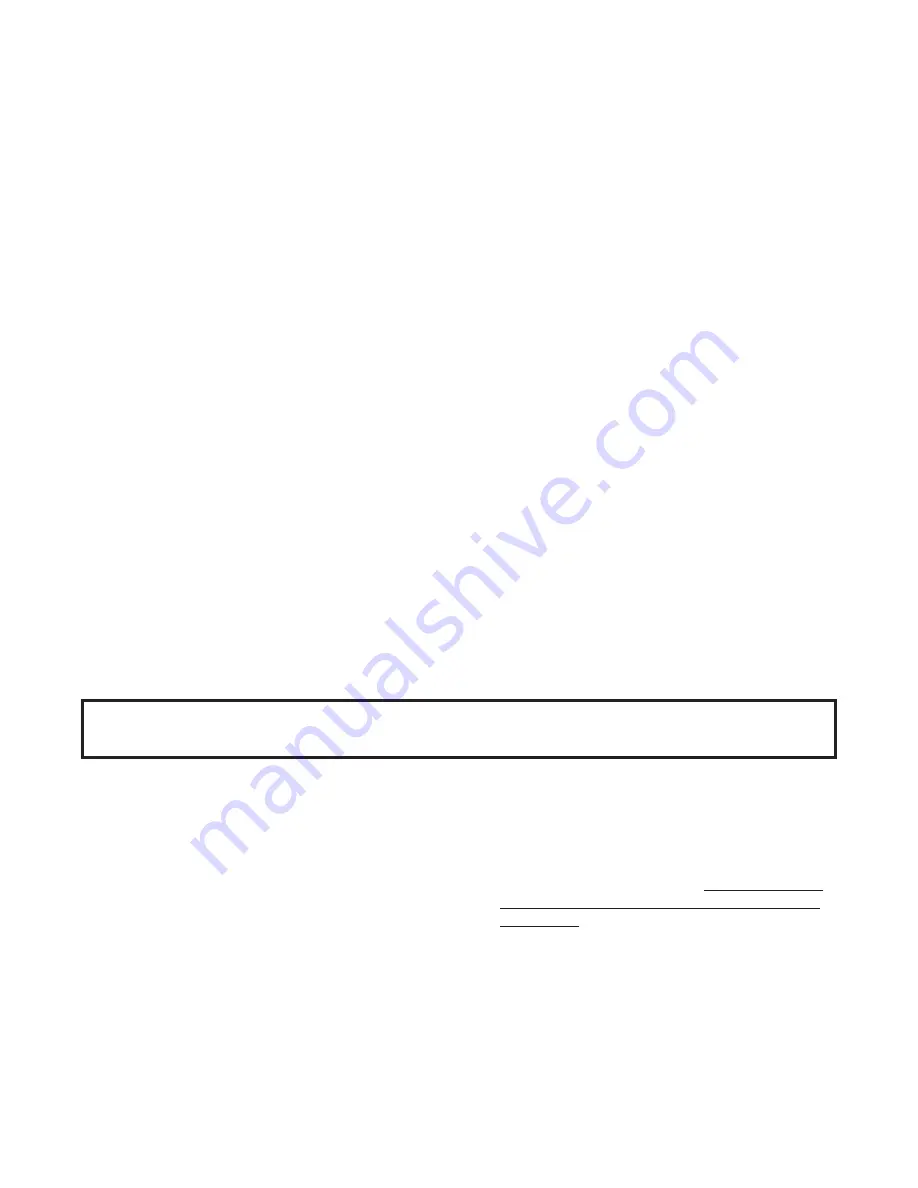
2
INSTALLATION INSTRUCTIONS
4. Use of a dampener is necessary to minimize
pulsation at drive elements, plumbing, con-
nections, and other system areas. The use of
a dampener with Giant Industries, Inc. pumps
is optional, although recommended by Giant
Industries, Inc. to further reduce system pulsa-
tion. Dampeners can also reduce the severity
of pressure spikes that occur in systems using
a shut-off gun. A dampener must be positioned
downstream from the unloader.
5. Crankshaft rotation on Giant Industries, Inc.
pumps should be made in the direction desig-
nated by the arrows on the pump crankcase.
Reverse rotation may be safely achieved by fol-
lowing a few guidelines available upon request
from Giant Industries, Inc. Required horsepow-
er for system operation can be obtained from
the charts on page 3.
6. Before beginning operation of your pumping
system, remember: Check that the crankcase
and seal areas have been properly lubricated
per recommended schedules. Do not run the
pump dry for extended periods of time. Cavi-
tation will result in severe damage. Always
remember to check that all plumbing valves are
open and that pumped media can flow freely to
the inlet of the pump.
Installation of the Giant Industries, Inc.,
pump is not a complicated procedure, but
there are some basic steps common to all
pumps. The following information is to be
considered as a general outline for instal-
lation. If you have unique requirements,
please contact Giant Industries, Inc. or your
local distributor for assistance.
1. The pump should be installed flat on a base
to a maximum of a 15 degree angle of inclina-
tion to ensure optimum lubrication.
2. The inlet to the pump should be sized for the
flow rate of the pump with no unnecessary re
-
strictions that can cause cavitation. Teflon tape
should be used to seal all joints. Maximum inlet
fluid temperature is 160
o
F (71
o
C).
3. The discharge plumbing from the pump
should be properly sized to the flow rate to pre
-
vent line pressure loss to the work area. It is es-
sential to provide a safety bypass valve between
the pump and the work area to protect the pump
from pressure spikes in the event of a blockage
or the use of a shut-off gun.
1. Prior to initial operation, add oil to the
crankcase so that oil level is between the two
lines on the oil dipstick. DO NOT OVERFILL.
Use SAE 80W-90 Industrial Gear Lube
Oil (Giant’s p/n 01154)
Crankcase oil should be changed after
the first 50 hours of operation, then at regular
intervals of 500 hours or less depending on
operating conditions.
2. Pump operation must not exceed rated
pressure, volume, or RPM. A pressure relief
device must be installed in the discharge of
the system.
3. Acids, alkalines, or abrasive fluids can
-
not be pumped unless approval in writing is
obtained before operation from Giant Indus-
tries, Inc.
4. Run the pump dry approximately 10
seconds to drain the water before exposure
to freezing temperatures.
IMPORTANT OPERATING CONDITIONS
Failure to comply with any of these conditions invalidates the warranty.
Finally, remember that high pressure operation in a pump system has many advantages. But, if it is
used carelessly and without regard to its potential hazard, it can cause serious injury.