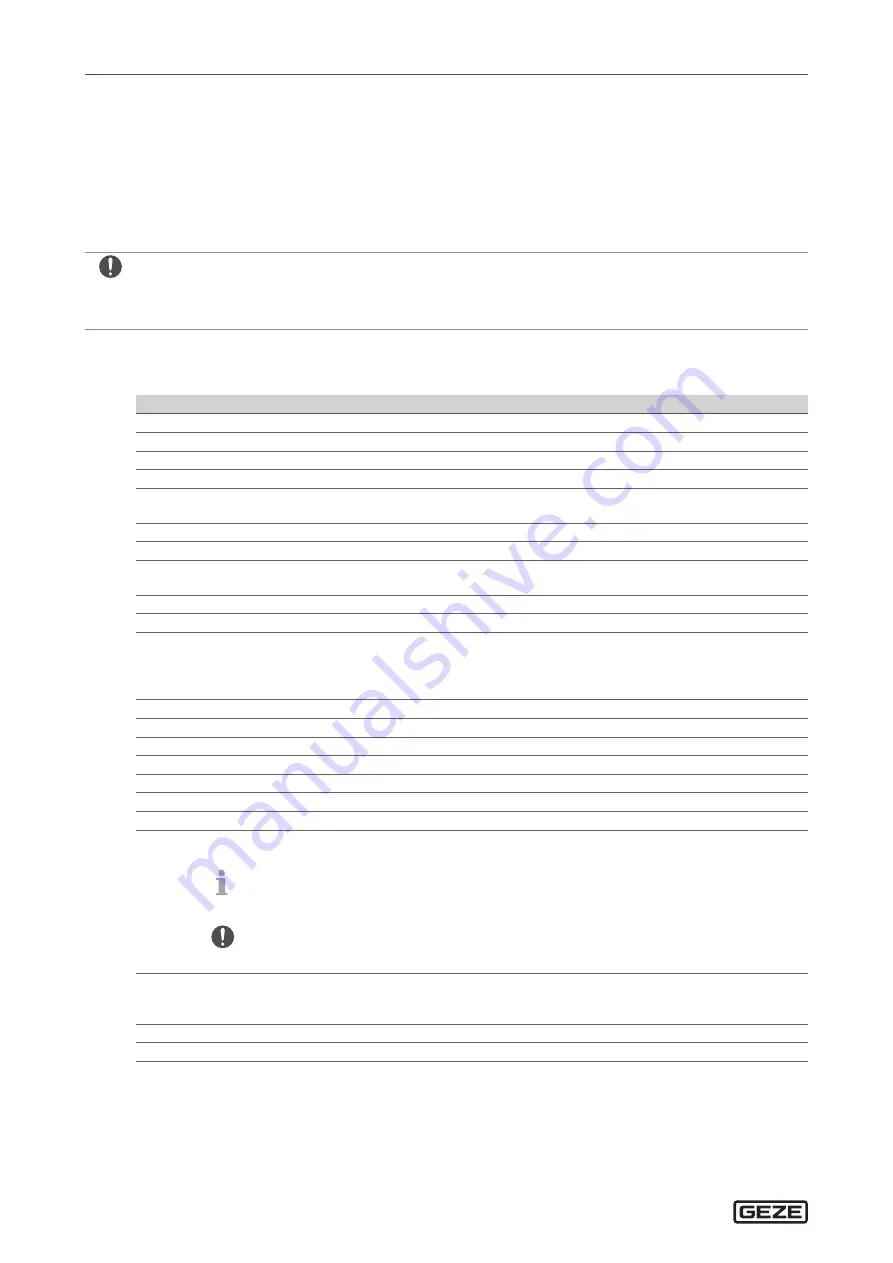
Powerturn
48
Powerturn installation check list
10.4 Electrical faults
Fault messages are stored and can be retrieved using the display programme switch or the service terminal ST220.
If a fault is currently active, it is shown every 10 seconds on the display programme switch or the service terminal ST220.
If the dot lights up on the left half of the display programme switch, the system was unable to completely
initialise after being switched on. There is either an obstruction in the way or something in the system itself has
become jammed.
The dot extinguishes as soon as the door has been opened completely and closed again once.
For troubleshooting and fault elimination see the fault table in the wiring diagram, chapter “Fault messages” chapter.
X
After changes to the drive (spring pre-load, opening width, fitting dimensions, change in the coupling ele-
ments) or modifications to the “Open” safety sensor, check the control parameters (see wiring diagram).
X
Reteach the drive (see wiring diagram).
X
Let “service mode” be executed completely (see wiring diagram).
11 Powerturn installation check list
No.
Test
on Page
in Chapter
Completed
1
All cables routed correctly for installation of the Powerturn?
–
–
2
Mounting plate installed?
Option: Door transmission angle installed for door leaf installation?
Option: Cover mounting plate installed?
3
à
Rail installed; suspension bolt and opening restrictor inserted before-
hand?
à
Link arm bearing block installed?
4
230-V connection with locking latch established?
Option: Connection can be set up later by a professional electrician;
separate 230-V Schuko plug cable used for set-up?
5
Bottom clamping claw released?
Option: Insert counter piece?
6
Drive unit:
à
set in place?
Option: Door leaf installation with door transmission angle, insert
side panel
à
locked? (slide)
à
Corrugated-head screw set?
à
Clamping claw tightened?
7
Counter piece inserted?
Option: Spindle extension attached?
8
Shaft cover installed?
Option: Mounting aid used?
9
Lever inserted on the drive and fastened (pre-tensioned corresponding
to the type of installation)?
Set lever in place, see supplementary installation
sheet, chapter 12
Lever pre-load ≠ Spring pre-load.
X
Follow the installation instructions.
10
Connection to the door element established
(suspension bolt screwed into the lever or link arm jammed)?
Mounting aid removed?
11
Identification plate completed?
12
Mechanical mobility of the door checked?
–
–
Summary of Contents for Powerturn
Page 50: ...Powerturn 50 Powerturn installation check list...
Page 51: ...Powerturn 51 Powerturn installation check list...
Page 52: ...Powerturn 52 Powerturn installation check list...
Page 53: ...Powerturn 53 Powerturn installation check list...
Page 54: ...Powerturn 54 Powerturn installation check list...
Page 55: ...Powerturn 55 Powerturn installation check list...