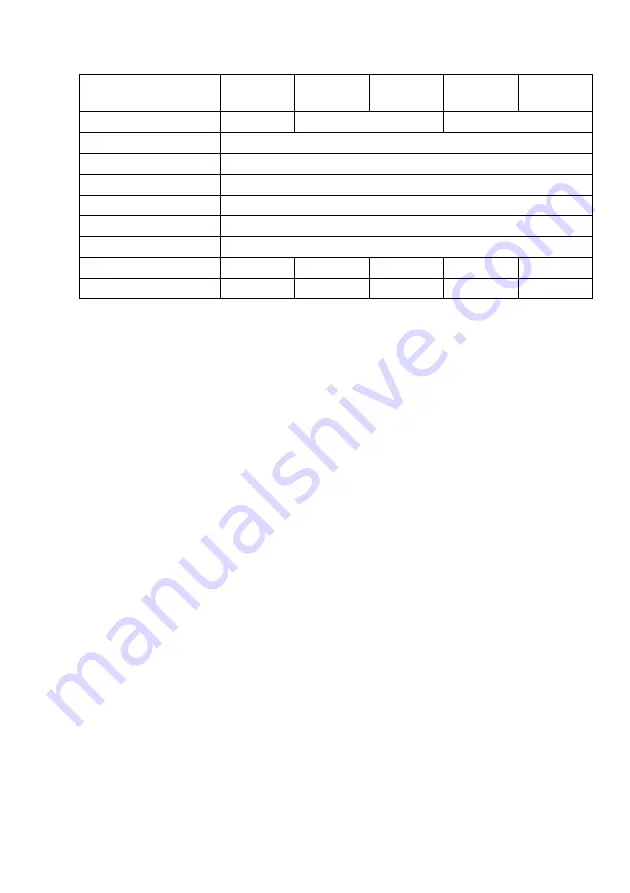
41
UNA 47 PN63 with flange ASME B16.5 class 400/600
Nominal diameter
DN 15
(½”)
DN 20
(¾”)
DN 25
(1”)
DN 40
(1½”)
DN 50
(2”)
Installed length L [mm (in)]
241 (9.5)
267 (10.5)
292 (11.5)
W [mm (in)] standard cover 290
(11.5)
H1 [mm (in)]
110 (4.4)
H2 [mm (in)]
155 (6.2)
1
Total height H [mm (in)]
260 (10.3)
1
Width L1 [mm (in)]
175 (6.8)
2
X [mm (in)]
13 (0.5)
Weight
[kg]
25 26 27 32 34
Weight
[lb]
55.1 57.3 59.5 70.5 75.0
1
Plus 25 mm (1 in) if fitted with manual vent valve.
2
Plus 35 mm (1.4 in) if fitted with manual lifting lever.
Summary of Contents for UNA 46
Page 26: ...26 UNA 45 with cover for installing electrodes ...
Page 28: ...28 UNA 45 with sightglass cover ...
Page 50: ...50 ...
Page 51: ...51 ...