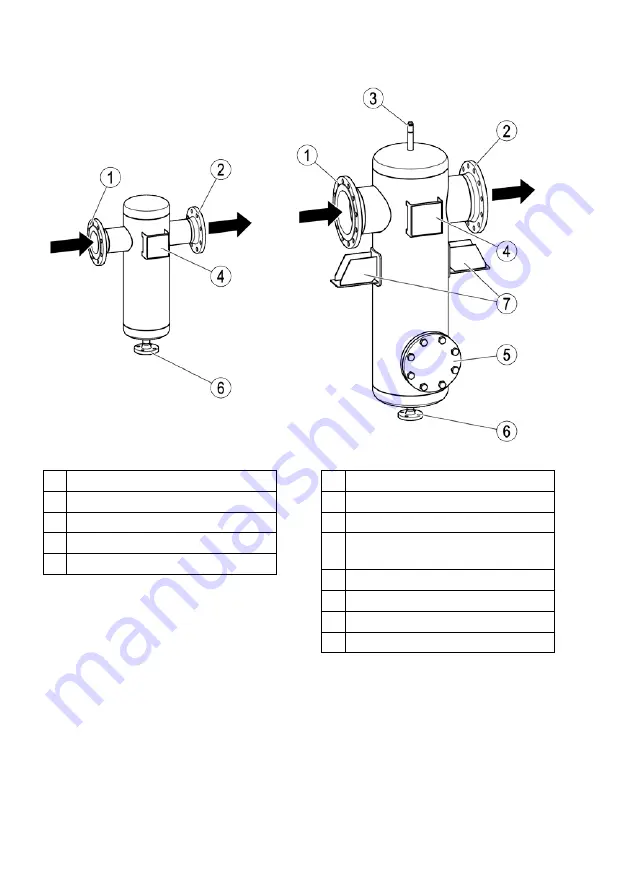
6
Nominal sizes 15 to 175
Nominal size 200 upwards
No. Designation
1 Connection for steam or air inlet
2 Connection for steam or air outlet
4 Name plate
6 Connection for condensate outlet
No. Designation
1 Connection for steam or air inlet
2 Connection for steam or air outlet
3 Vent (only needed for work by the
manufacturer)
4 Name plate
5 Inspection hole
6 Connection for condensate outlet
7 Lugs (nominal size 200 upwards)