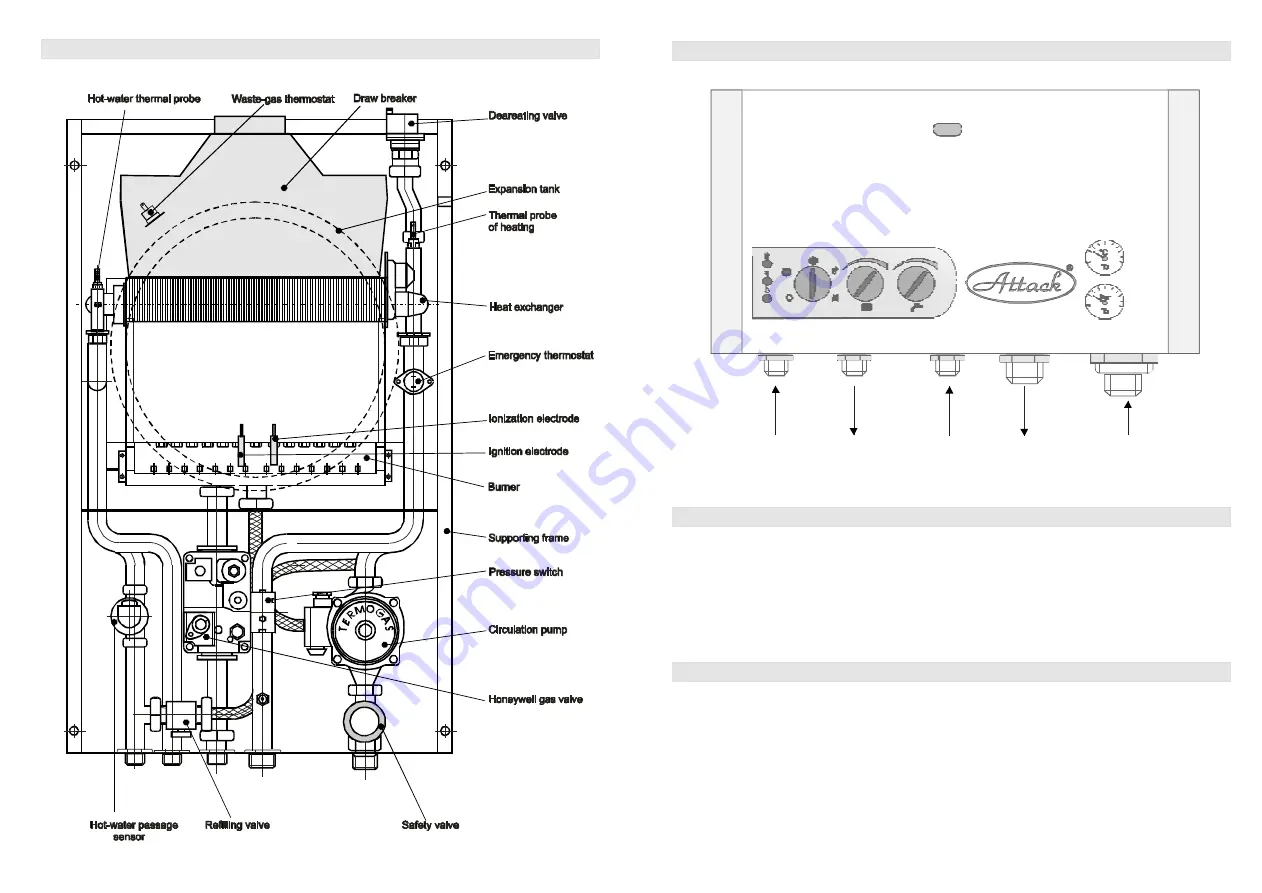
9
Main parts of the NSK boiler
3
Bar
D.H.W. inlet
1/2”
Gas inlet
3/4”
C.H. outlet
3/4”
C.H. inlet
3/4”
D,H.W. outlet
1/2”
10
Connecting the boiler to water and gas:
Connecting the boiler to electric net
Operation control
The boiler is plugged into the electric net socket with a supply lead with a plug. The socket
must suit to appropriate standards , various multiplugs and lenghtening cables are not
allowed to use. Installation of the socket, connecting the space thermostat and service of
electric parts of the boiler can be only performed by a person with special electric
qualification by the Public Notice No. 718/2002 Z.z. Electric installation is ready for
additional connection of room thermostat.
During the operation the boiler is secured against dangerous operation conditions.
However, the breakdowns the cause of which is not included in the boiler mechanism,
cannot be protected to arise. Therefore it is necessary after putting the boiler to operation to
examine the boiler once in three days and check:
– whether the system is filled with water and there is no discharge
– whether waste gases or gas cannot be smelled
Found breakdowns must be reported to the service worker who put the boiler to
operation. If there is a gas discharge, the gas supply must be closed. Found breakdowns
must be removed immediately.
Summary of Contents for Attack NSK
Page 1: ......