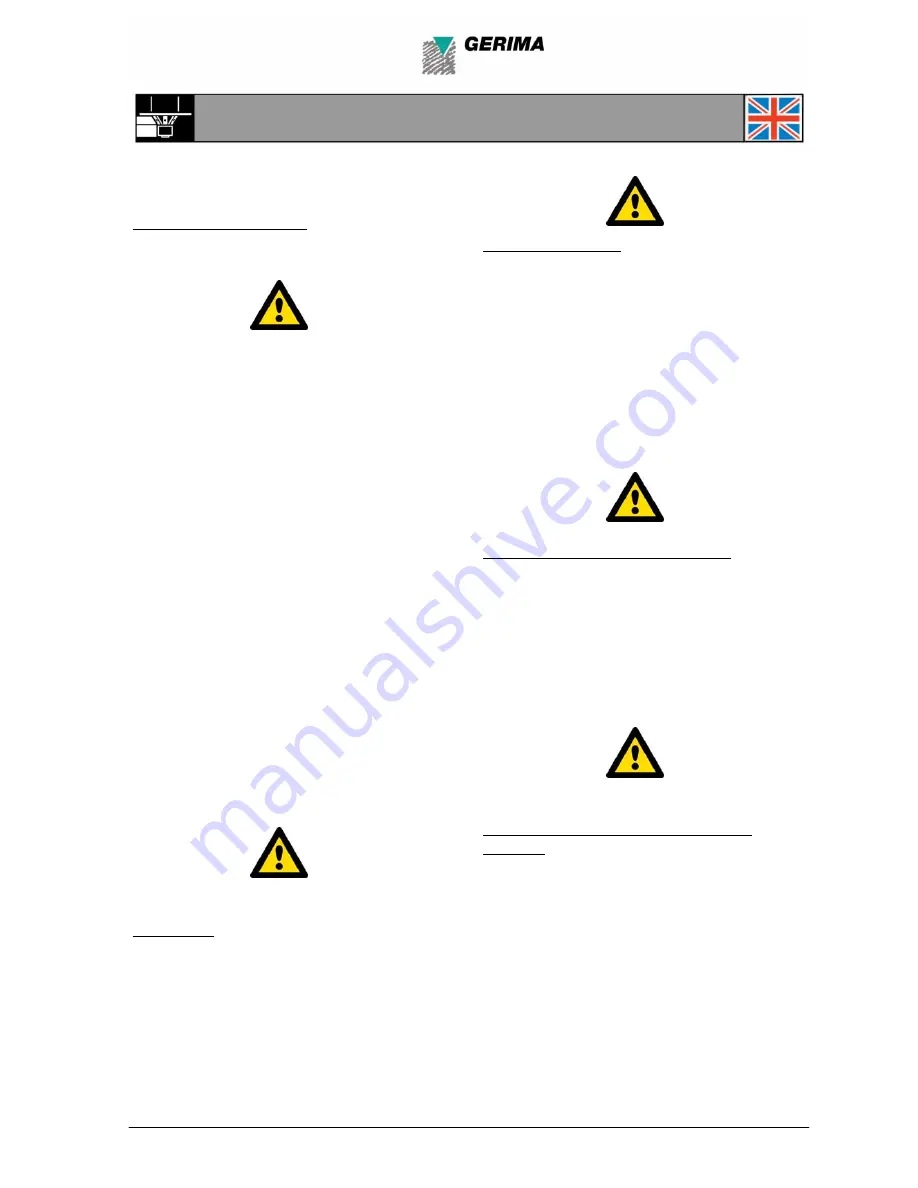
6
V.02
.22.03.10.ENG
2.
Safety
information
General
safety
information:
Before
using
the
machine,
the
operating
manual
and
safety
information
must
have
been
read
and
understood
in
their
entirety.
The
instructions
contained
therein
must
be
followed.
Safety
regulations
such
as
DIN,
VDE,
CEE,
AFNOR
and
others
applicable
in
the
country
of
use
must
be
observed.
These
instructions
cover
the
operation
and
han
‐
dling
of
the
machine,
including
tools,
accessories
and
machine
maintenance.
Failure
to
comply
with
these
established
safety
recommendations
can
cause
serious
hazards.
The
machine
operator
must
have
properly
un
‐
derstood
the
following
safety
advice
and
must
have
access
to
these
instructions
at
all
times.
To
prevent
improper
handling
of
the
machine
and
to
prevent
accidents,
the
operator
must
comply
with
the
safety
precautions
set
out
be
‐
low.
Hand
hat.
Installation:
The
machine
must
only
be
connected
to
an
elec
‐
trical
power
source
with
a
voltage
equal
to
that
specified
for
the
machine.
Electrocution
hazard!
•
Always
disconnect
the
machine
from
the
power
supply
before
servicing.
•
Before
each
use,
always
check
the
plug,
ca
‐
ble
and
machine
for
signs
of
damage.
•
The
machine
must
be
kept
dry.
Do
not
use
in
damp
locations
or
humid
environments.
•
If
used
out
of
doors,
the
machine
must
be
protected
by
a
residual
‐
current
circuit
‐
breaker
with
a
maximum
tripping
current
of
30
mA.
Improper
use
can
cause
serious
injury!
•
Always
wear
safety
goggles,
ear
protectors,
gloves
and
safety
shoes
when
working
with
the
machine.
•
Insert
power
plug
only
when
machine
is
switched
off.
Disconnect
machine
from
the
power
supply
after
use.
Improper
use
can
damage
equipment
and
property!
•
Never
lift
or
carry
the
machine
by
its
power
cable.
•
Make
sure
the
cable
is
directed
behind
and
away
from
the
machine.
Do
not
lay
the
ca
‐
ble
over
sharp
edges.
•
Servicing
and
testing
must
only
be
carried
out
by
appropriately
qualified
technicians.
Safety
information