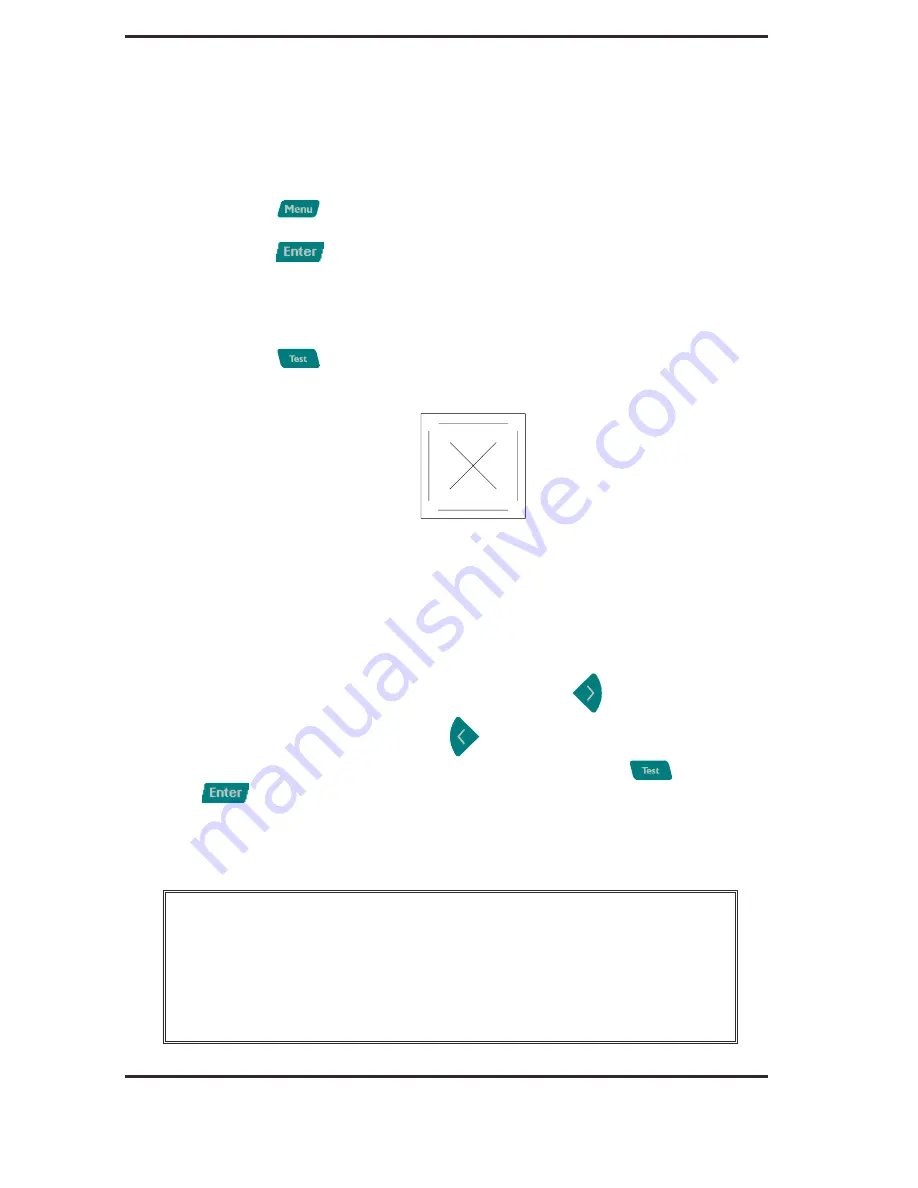
Gerber P2C™ 600
User’s Manual
General Information
1-23
- Tighten the clamp screw.
6.
Set the knife pressure as follows:
•
Power up the cutter and load a piece of media (See 1.7).
•
Press the
key twice.
•
Press the
key.
•
The knife pressure parameter is displayed. The pressure can be set
anywhere from 0 to 400gr.
•
Press the
key to perform a knife depth test as illustrated below.
FIGURE 1-12
KNIFE DEPTH TEST PATTERN
The knife depth is set correctly when the test pattern is visible on the
front side of the media backing but not on the back.
If the cut pattern is not visible on the front side of the media backing,
increase the knife pressure by pressing the
key. Decrease the
knife pressure by pressing the
key when the cut pattern is visible
on the back side of the media backing. Press the
key or the
key to save the changed setting.
In general, the knife depth and pressure should be increased when
using thicker vinyl.
NOTE
As the ideal knife pressure setting depends upon the type and
thickness of the media to be cut, adjusting the pressure will require
some practice. Generally, the pressure should be increased when
thicker types of vinyl are being cut. Thinner types of vinyl usually
require lower knife pressure settings.