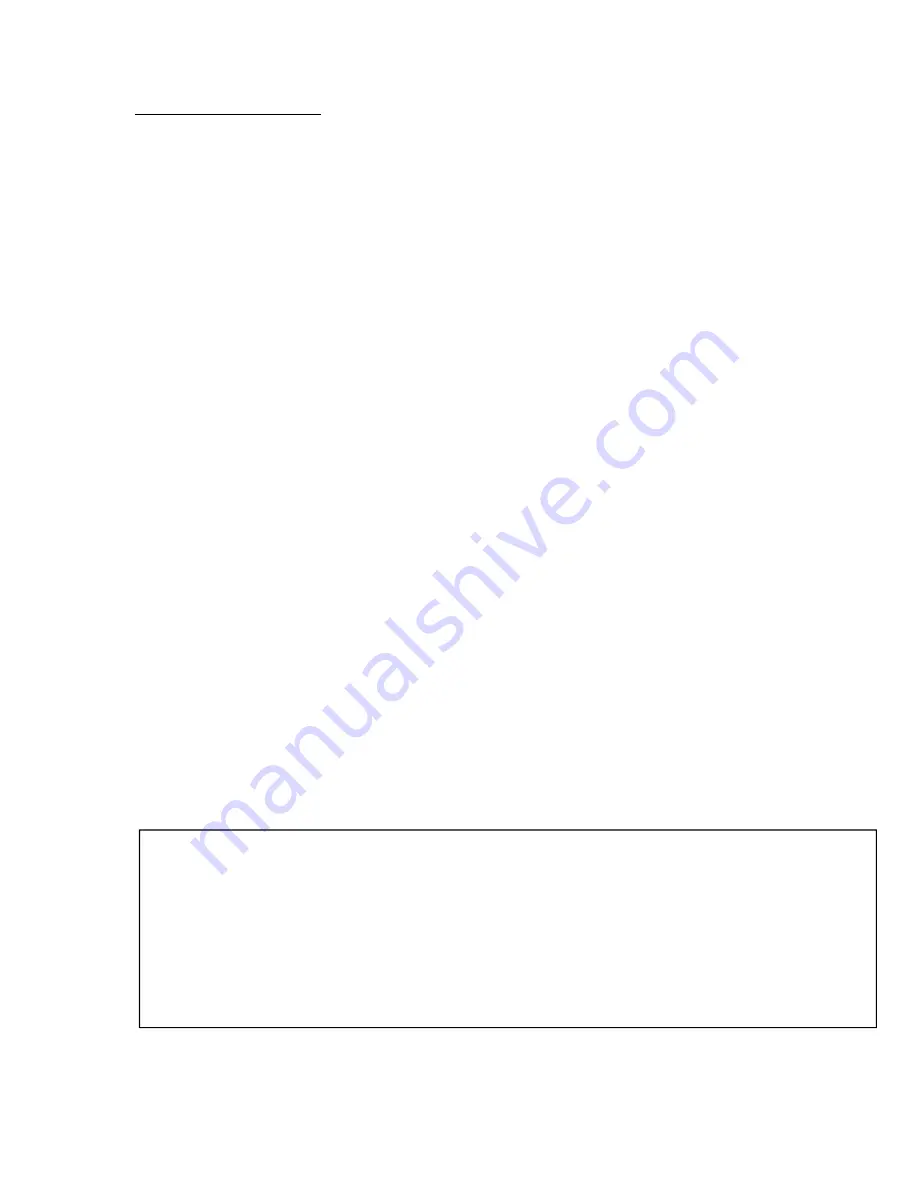
23
Polynomial Conversion:
G
nn/c/tt/saaaaaa/sbbbbbb/scccccc
Where:
nn = Channel # (Valid entries are 1,2,3…16 for the LC-2x16)
c = Conversion Type(L/P) where L=Linear and P=Polynomial
t = Gage Type:
0:
Channel
Disabled
(will
display
“---“)
1:
VW
Gage
Type
1
2:
VW
Gage
Type
2
3:
VW
Gage
Type
3
4:
VW
Gage
Type
4
5:
VW
Gage
Type
5
6:
VW
Gage
Type
6
saaaaaa = polynomial coefficient A with sign
sbbbbbb = polynomial coefficient B with sign
scccccc = polynomial coefficient C with sign
When using polynomial conversion (P), the G command is used to select the gage type and enter
the three polynomial coefficients, A, B and C.
Polynomial Conversion is described further as follows:
saaaa
represents polynomial coefficient A,
sbbbb
represents polynomial coefficient B and
scccc
polynomial coefficient C. The polynomial coefficients can be entered with a sign and decimal
point. The maximum number of digits, including sign and decimal point is 15. The entered value
will display to a maximum of five places to the right of the decimal point.
For the vibrating wire instruments (Gage Types 1-6), the basic formula for calculation of
displayed and stored values is as follows:
Display
(CurrentReading
2
A) + (CurrentReading
B) + C
Equation 2 - Displayed Gage Reading using Polynomial Conversion
NOTE: When using the Polynomial conversion method, the default reading units for a vibrating wire instrument is
the frequency squared multiplied by 10
-6
. For example, an instrument reading 3000Hz will output a value of "9.000"
when A is entered as "0", B is "1" and C is "0". However, typical calibration units for vibrating wire instruments are
frequency squared multiplied by 10
-3
. To adjust for this discrepancy between LC-2 expected units and calibration
units
multiply the A coefficient by 1,000,000 and the B coefficient by 1000. The A and B coefficients can be
found on the supplied calibration certificate.
The
C
coefficient should be calculated based on an actual field
reading.
The above multiplication is
only
necessary if the datalogger is being set up via text commands (see section
2.3)
AND
the gage conversion is set for polynomial. When using LogView to set up the datalogger configuration,
the multiplication is performed by LogView. Refer to the appropriate sensor manual for more information on how to
calculate the
C
coefficient.
Summary of Contents for LC-2x16
Page 2: ......