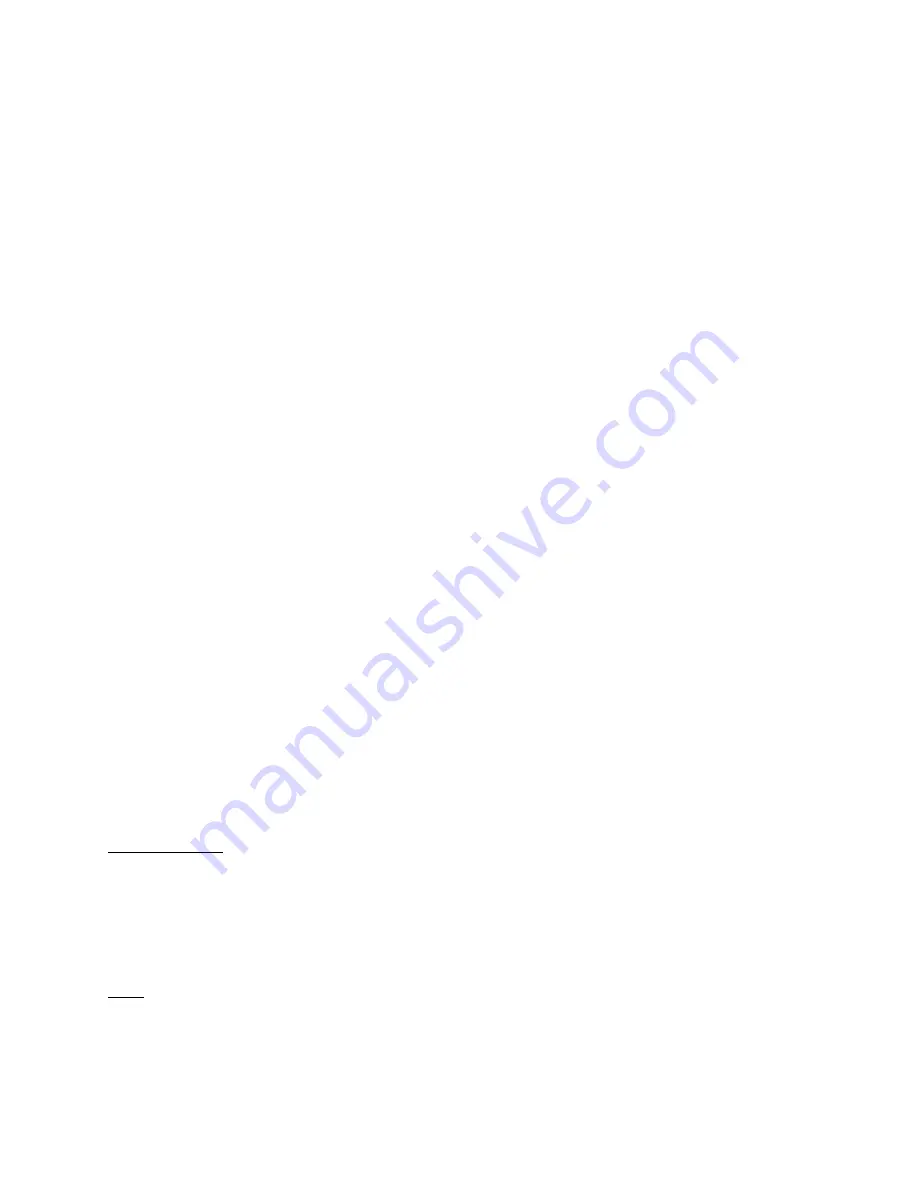
BASIC INSTRUCTIONS
Geo. Knight offers a variety of machine options under the MAXI PRESS AIR line. There
are two standard sizes of 30” x 40” and 40” x 64” heat platens, both of which can be ordered as
twin stations and with top and bottom heat. The general operation and features of the MAXI
PRESS AIRes are basically the same regardless of the options included. These options can not be
added after the machine has been built. Please use the following information as a guide only. If
there are any detailed questions or issues with the press, please call the factory at 800-525-6766.
UNPACKING
Your MAXI PRESS AIR was shipped in a fully enclosed crate. Great care must be used
when uncrating the machine and removing all of the packaging material. The MAXI PRESS AIR
is lagged to the bottom of the crate. Depending on the model, the sidewalls of the wooden crate
may need to be dismantled in order to remove the air maxi from its crate.
It is recommended that a forklift be used to remove the AIR MAXI PRESS from the
crate.
CARE MUST BE USED TO POSITION THE FORKS IN AN AREA THAT WILL
NOT DAMAGE ANY OF THE LOWER AIR COMPONENTS OR AIR TUBING.
NEVER LIFT THE PRESS BY LIFTING UP UNDER THE TOP HEATER BLOCK.
Only
lift up against the lower steel tubing structure.
Locate the MAXI PRESS AIR in an area that will allow for access around the entire
machine. On most machines the Main Power Disconnect is located in the rear of the press. Make
sure there is room to allow the operator to be able to reach the main disconnect on the machine.
IT IS RECOMMENDED THAT A TWIN STATION MAXI PRESS AIR BE
LAGGED/BOTLED TO THE FLOOR AFTER LEVELING THE MACHINE.
ELECTRICAL AND AIR SUPPLY REQUIREMENTS
ELECTRICAL:
30x40 (208-240 VAC) 1 phase 41 amps.
30x40 (208-240 VAC) 1 phase 81 amps (with bottom heat option)
40x64 (208-240 VAC) 1 phase 81 amps.
40x64 (208-240 VAC) 3 phase 95 amps (with bottom heat option)
AIR:
Regardless of the machine size, all of the MAXI PRESS AIR machines require
a 1/2” NPT AIR LINE with a maximum supply pressure of 100psi.