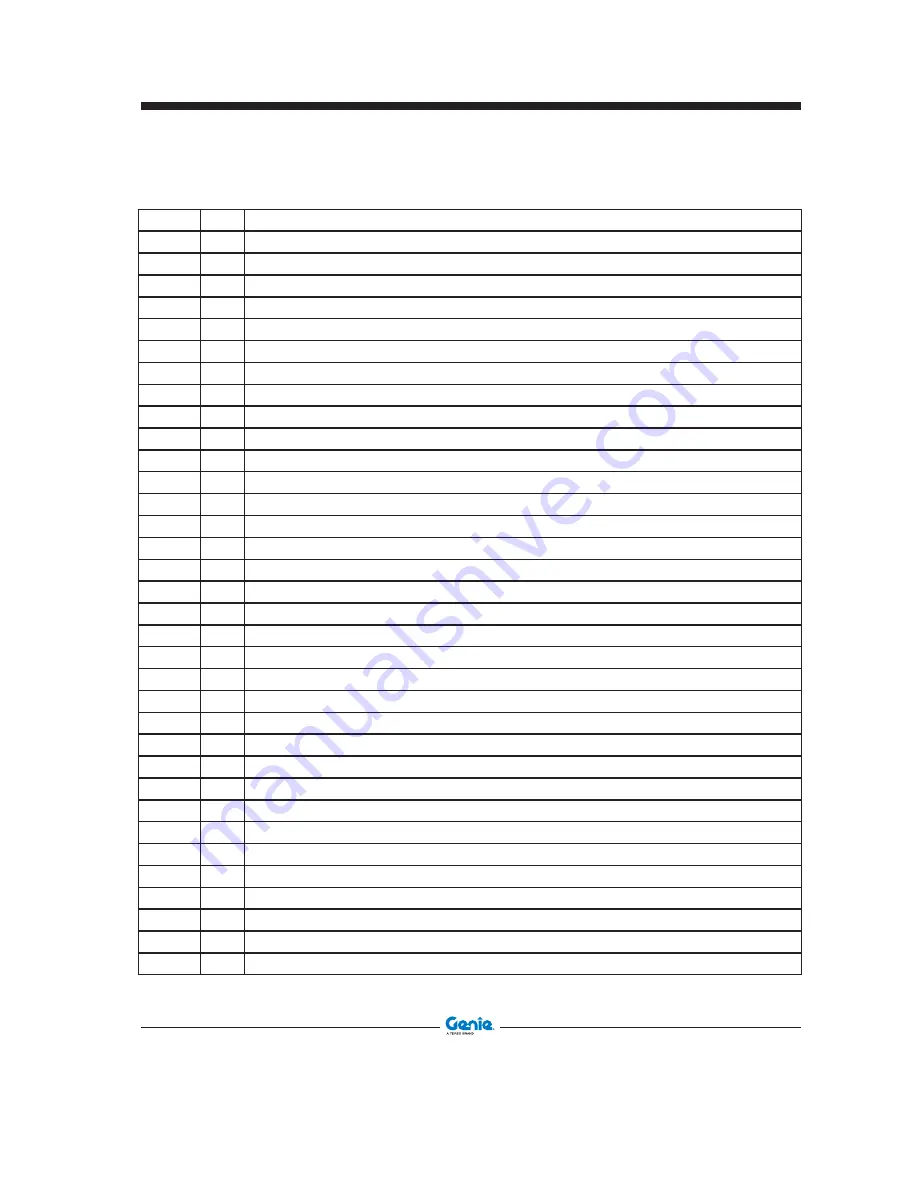
4-28
GTH-5519
Part No. 1272852
September 2016
Section 4 • Fault Codes
SPN
FMI Short Text Detail
1176
4
Sensor error pressure sensor downstream turbine; signal range check high
1180
0
Physical range check high for exhaust gas temperature upstream turbine
1180
0
Turbocharger Wastegate CAN feedback; warning threshold exceeded
1180
0
Exhaust gas temperature upstream turbine; warning threshold exceeded
1180
1
Physical range check low for exhaust gas temperature upstream turbine
1180
1
Turbocharger Wastegate CAN feedback; shut off threshold exceeded
1180
1
Exhaust gas temperature upstream turbine; shut off threshold exceeded
1180
3
Sensor error exhaust gas temperature upstream turbine; signal range check high
1180
4
Sensor error exhaust gas temperature upstream turbine; signal range check low
1180
11
Sensor exhaust gas temperature upstream turbine; plausibility error
1188
2
Wastegate; status message from ECU missing
1188
7
Wastegate actuator; blocked
1188
11
Wastegate actuator; internal error
1188
11
Wastegate actuator; EOL calibration not performed correctly
1188
11
Wastegate actuator; over temperature (> 145°C)
1188
11
Wastegate actuator; over temperature (> 135°C)
1188
11
Wastegate actuator; operating voltage error
1188
13
Wastegate actuator calibration deviation too large, recalibration required
1231
14
CAN-Bus 1 "BusOff-Status"
1235
14
CAN-Bus 2 "BusOff-Status"
1237
2
Override switch; plausibility error
1322
12
Too many recognized misfires in more than one cylinder
1323
12
Too many recognized misfires in cylinder 1 (in firing order)
1324
12
Too many recognized misfires in cylinder 2 (in firing order)
1325
12
Too many recognized misfires in cylinder 3 (in firing order)
1326
12
Too many recognized misfires in cylinder 4 (in firing order)
1327
12
Too many recognized misfires in cylinder 5 (in firing order)
1328
12
Too many recognized misfires in cylinder 6 (in firing order)
1639
0
Sensor error fan speed; signal range check high
1639
1
Sensor error fan speed; signal range check low
1761
14
Urea tank level; warning threshold exceeded
2621
3
Flush valve burner (EPV DPF-System); short circuit to battery
2621
4
Flush valve burner (EPV DPF-System); short circuit to ground
2621
5
Flush valve burner (EPV DPF-System); open load
FAULT CODES