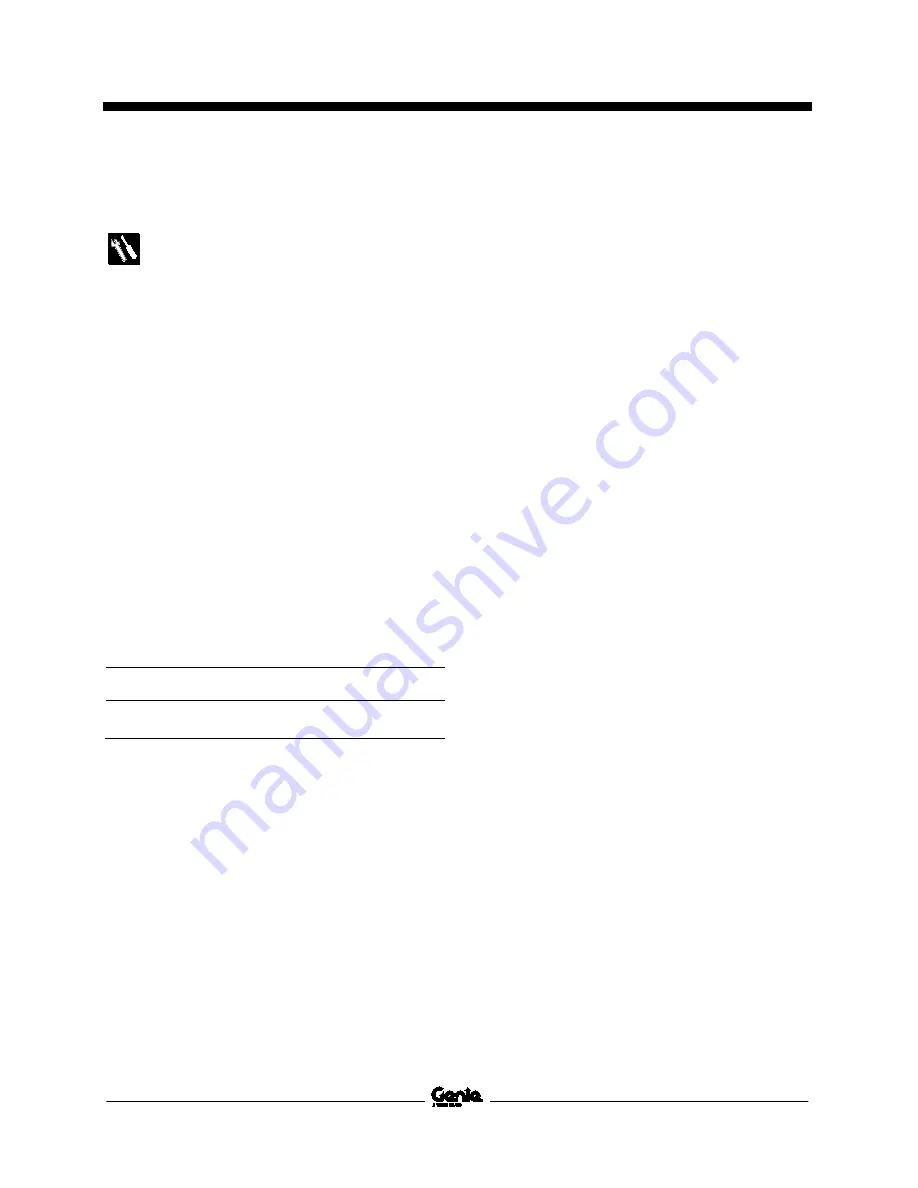
September 2016
Service Manual
Checklist A Procedures
Part No. 115417
Genie Lift
23
A-6 Inspect the C asters and Wheels
A-6
Inspect the Casters and Wheels
Genie specifications require that this procedure be
performed every 8 hours or daily, whichever comes
first.
Maintaining the casters and wheels in good
condition is essential to safe operation and good
performance. Casters or wheel failure could result
in a machine tip-over. Component damage may
also result if problems are not discovered and
repaired in a timely fashion. Extremely dirty
conditions may require that the wheels and casters
be inspected more often.
1 Unlock the brake (if equipped) and move the
machine on a firm smooth surface and check
that the casters and wheels roll smoothly, free
of hesitation and binding.
2
Models with Pneumatic Wheel:
Check the
tire pressure with an air pressure gauge and
add air as needed.
Specification
Pneumatic tires
50 psi
3.4 bar
Summary of Contents for Genie Lift
Page 15: ...September 2016 Service Manual Part No 115417 Genie Lift 15 This page intentionally left blank ...
Page 17: ...September 2016 Service Manual Part No 115417 Genie Lift 17 This page intentionally left blank ...
Page 19: ...September 2016 Service Manual Part No 115417 Genie Lift 19 This page intentionally left blank ...
Page 45: ......