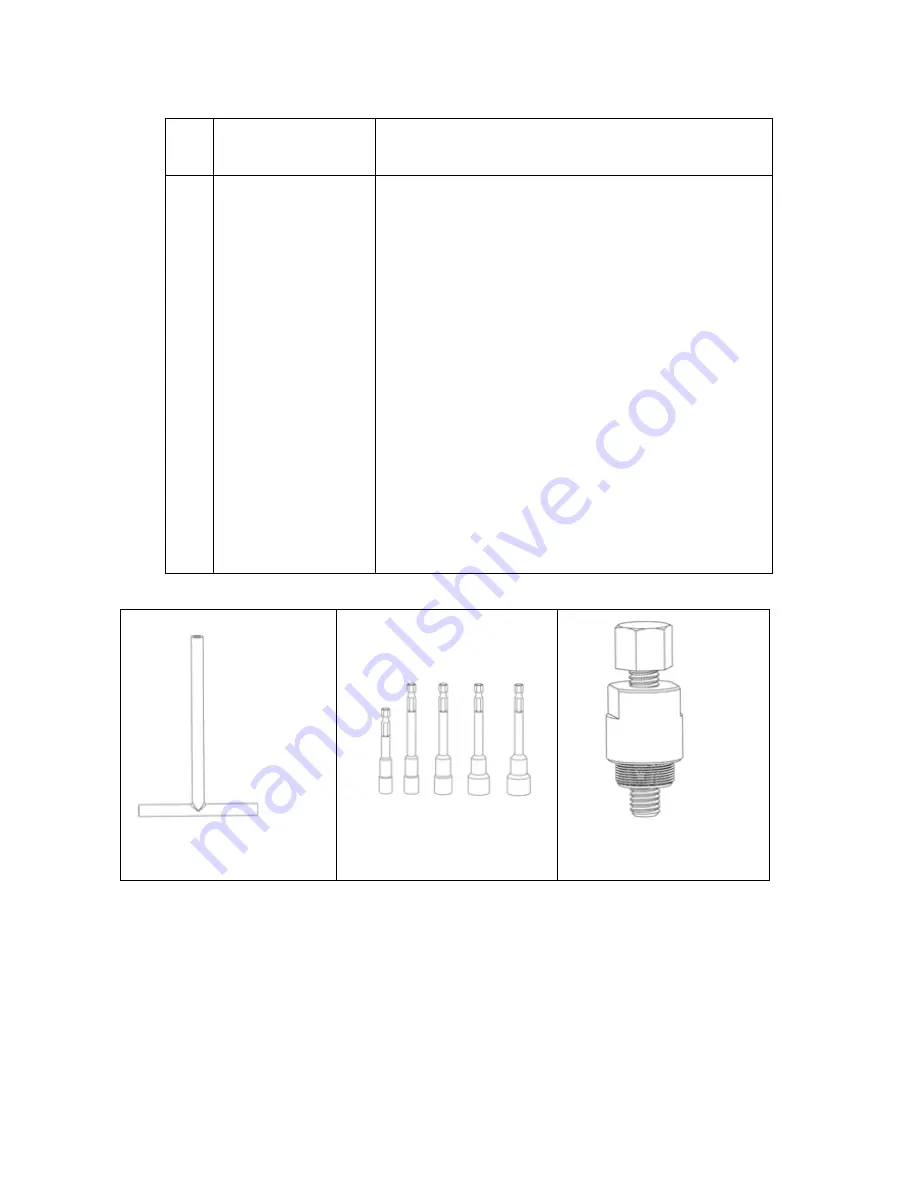
105
SPECIAL TOOLS LISTED BELOW FOR REMOVAL AND REINSTALLATION
NO. TOOL
NUMBER
DESCRIPTION
1
2
3
4
5
6
7
8
9
10
T01
T02
T03
T04
T05
T07
T08
T09
T10
“T”shape of sleeve
sleeve tools
(
7mm,8mm,10mm,12mm,13mm
)
flywheel remover
sleeve (18mm,24mm)
screw remover
cylinder pressure gauge
piston pin remover
spark plug remover
flywheel lockbolt remover
clutch clamp
Summary of Contents for XOR 50 ccm
Page 1: ......
Page 19: ...19 14...
Page 52: ...52 CHAPTER 4 FUEL AND LUBRICATION SYSTEM CONTENTS FUEL SWITCH CARBURETOR OIL PUMP...
Page 73: ...73 3 Disconnect throttle cable and oil pump cable 4 Remove rear brake cable adjusting nut...
Page 86: ...86...
Page 101: ...101 WIRE CABLE AND BRAKE HOSE ROUTING...
Page 102: ...102 carburetor...
Page 103: ...103...
Page 104: ...104 Ignition coil Starting relay CDI HORN POWER SWITCHH...
Page 106: ...106...