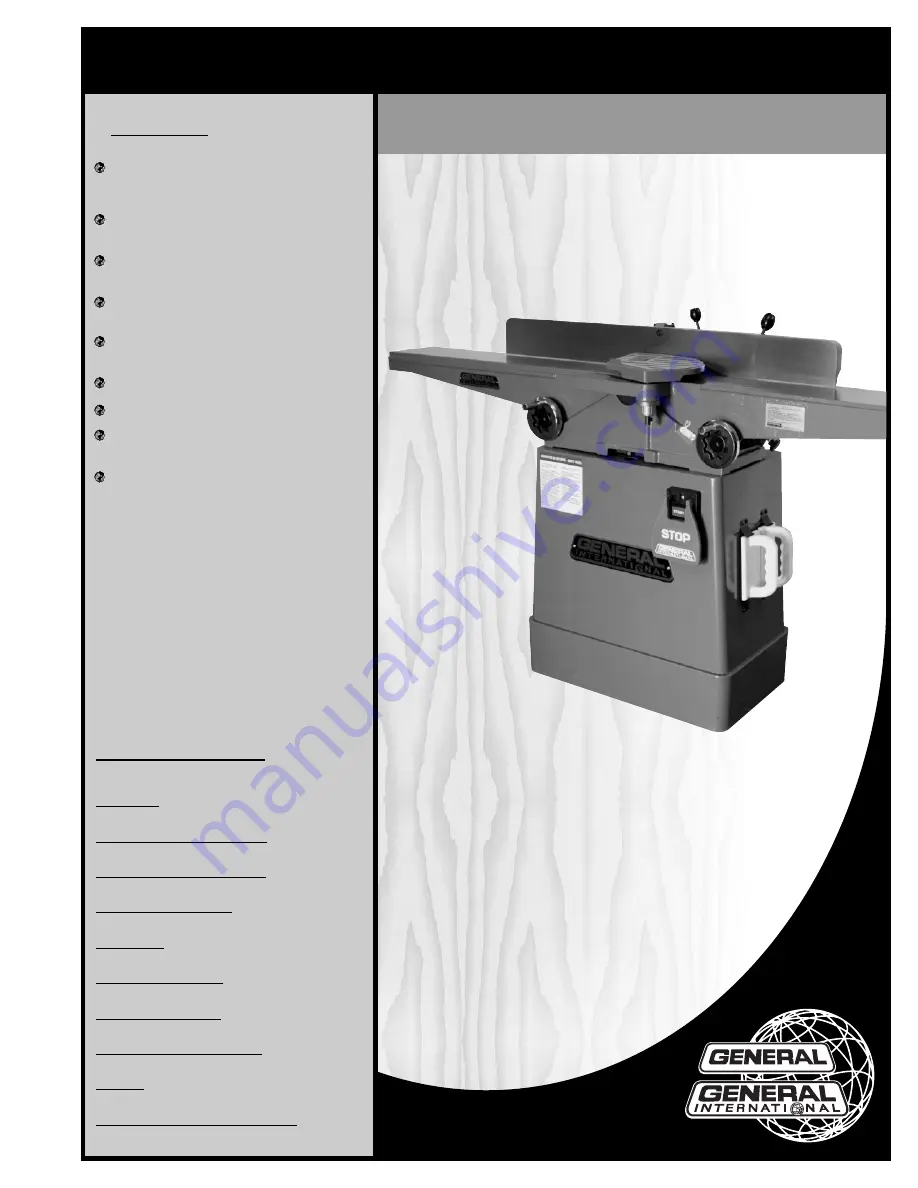
FEATURES
Large surface, ground cast-iron tables for
stability and added support when feeding
longer stock.
Heavy-duty, three-knife cutter head for
clean, fast, superior finish cuts.
Jackscrew system for quick, easy knife
adjustment.
Large, heavy-duty, center-mounted cast-
iron fence with 90° and 45° positive stops.
Independent in-feed and out-feed table
adjustment handwheels.
4” dust collection outlet included.
Built-in rabbeting ledge.
2 hand-paddle style push blocks with
onboard storage mounts included.
Extra long 66 1/4” tables
SPECIFICATIONS
TABLE SIZE
7 1/4" x 66 1/4" (184 x 1683 mm)
MAXIMUM CUTTING WIDTH
6" (152 mm)
MAXIMUM CUTTING DEPTH
1/2" (13 mm)
RABBETING CAPACITY
1/2" (13 mm)
FENCE SIZE
4" x 38" (102 x 965 mm)
CUTTER HEAD SPEED
5000 RPM
NUMBER OF KNIVES
3/HELICAL
BASE DIMENSIONS (L X W)
24" x 13 3/4" (610 x 349 mm)
MOTOR
1 HP, 110/220 V, 13/7 A
SHIPPING WEIGHT / NET WEIGHT
423 LBS (192 kg) / 340 LBS (154 KG)
SETUP & OPERATION MANUAL
VERSION 1 - REVISON 1 (August 16
th
, 2011)
© COPYRIGHT GENERAL INTERNATIONAL 2011
6” DELUXE JOINTER
MODEL
#80-125L/LHC
Summary of Contents for 80-125L
Page 31: ...31 Notes...