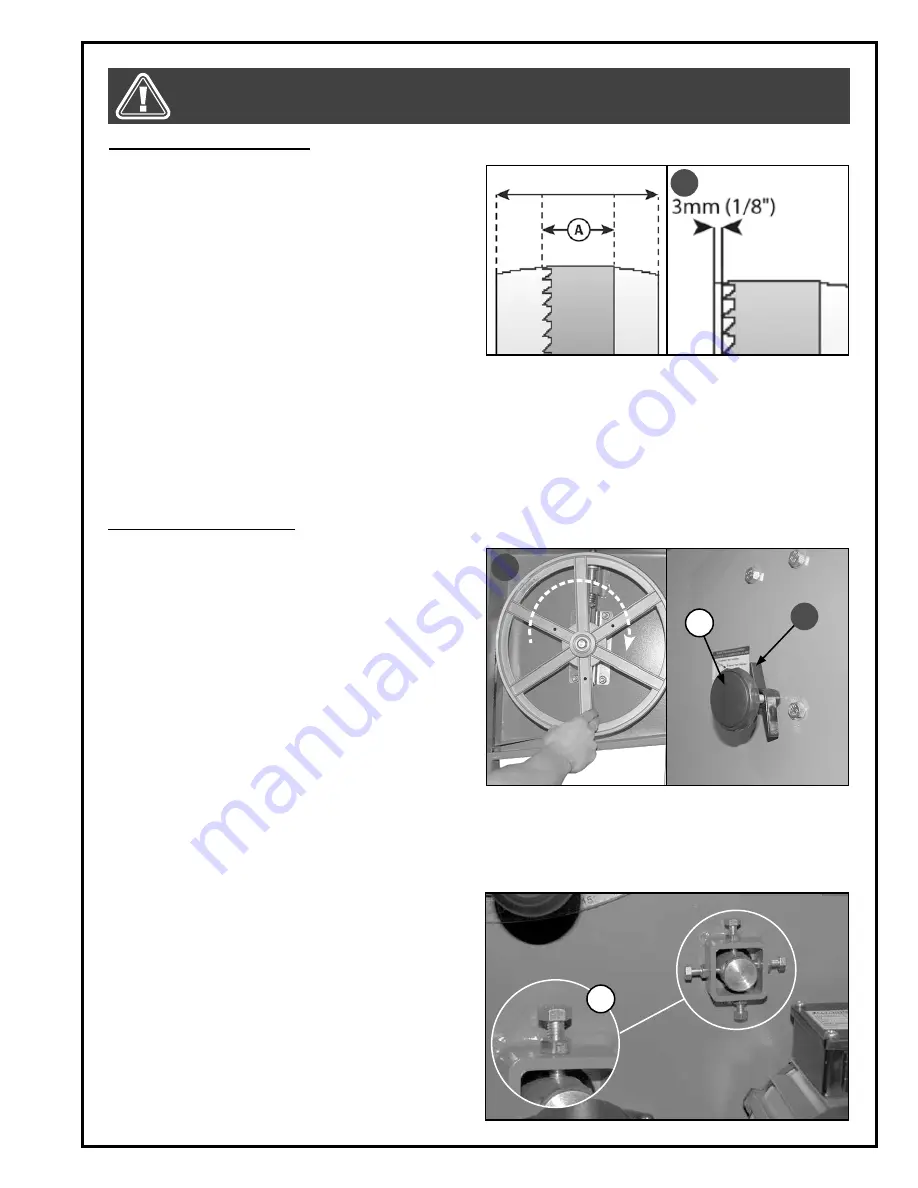
17
MAKE SURE THE MACHINE HAS BEEN TURNED OFF AND UNPLUGGED FROM THE POWER SOURCE BEFORE PERFORM-
ING ANY MAINTENANCE OR ADJUSTMENTS.
ADJUSTING BLADE TRACKING
Blade tracking means centering the blade on the
wheels
A.
Ideally, the blade should stay relatively cen-
tered on both the upper and lower wheels.
Due to natural variations in castings, blade thickness or
density and tire wear, absolute perfect centering align-
ment is rarely attainable. A slight misalignment of the
blade on the wheels is inevitable and as long as it is
kept to a minimum (following the steps listed below)
will not hinder the performance of the saw.
This misalignment is controlled and kept to a minimum
by adjusting the tilt angle of the upper wheel. When
adjusting blade tracking to center the blade on the
wheels and assuming that perfect centering is not attainable, it is preferable to have the blade slightly off-center
towards the front of the wheels rather than towards the rear because the teeth on most bandsaw blades have al-
ternating hook (one inner, one outer) – therefore if the blade is centered too far back on the wheel (or if the blade
tension is too tight), inner hooked teeth will dig into the wheel tire and cause premature wear of the tire.
Nonetheless, to avoid having the blade come off of the wheels on it’s own during operation, the front edge of the
blades teeth should never be any closer than 3 mm (1/8”) from the front edge of the wheel
B
.
To adjust the blade tracking:
B
Note: The upper and lower wheels are factory set to allow
for easy and optimal blade tracking adjustments using the
primary blade tracking adjustment knob, which adjusts the
angle of tilt of the upper wheel.
In extremely rare cases, if acceptable blade tracking can-
not be attained through the primary adjustment it may
eventually become necessary to make minor adjustments
to the angle of tilt of the lower wheel.
The four bolts F may be adjusted in or out to tilt the lower
wheel up/down or left/right as needed. Once the adjust-
ment is finished, retighten the the jam nuts.
F
1.
Open the upper door then rotate the wheel slowly
forward by hand
C
and check the position of the
blade on the wheel. The blade should remain as
centered as possible on the wheel as it turns
A
.
2
. If the blade tracking must be adjusted, loosen the
wing nut
D
on the tracking adjustment knob
E
, then
turn the knob:
Clockwise if the blade moves toward the front of
the wheel. This tilts the top of the wheel to the back
and moves the blade toward the center.
Counterclockwise if the blade moves toward the
back edge. This tilts the top of the wheel to the front
and moves the blade toward the center.
Note: Turn the tracking knobs in 1/2 turn increments, re-
check and adjust again as needed.
3.
With the tracking set, retighten the wing nut
D
.
C
E
D
Summary of Contents for 90-120
Page 25: ...DIAGRAM BANDSAW 25...
Page 29: ...NOTES...