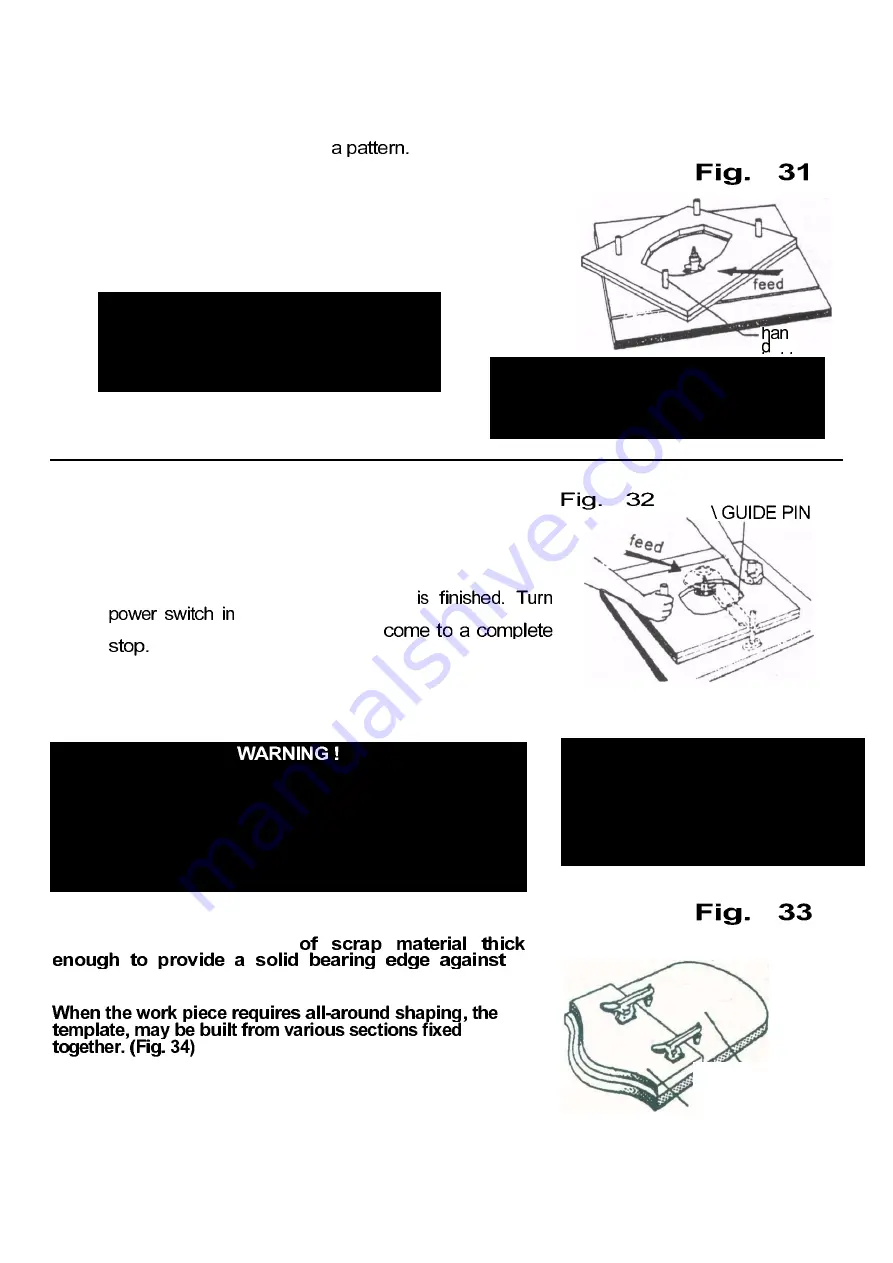
ENCLOSED EDGE SHAPING
Inside edge work piece are shaped the same way as
outside edges (Fig.31). When the whole edge needs to be
shaped, the operator must use
The work piece must be placed on table before starting the
motor. The operator must shape the whole work piece by
feeding into the cutters.
WARNING !
NEVER ATTEMPT TO PERFORM THIS
PROCEDURE WITHOUT A
RING GUARD OR A SIMILAR SAFETY
DEVICE OVER
CUTTERHEAD !
ATTENTION !
OPERATION MUST BE AWARE AT ALL
TIMES OF THE FEED DIRECTION !
OPERATION MUST NOT BE LEFT
UNATTENDED!
1. Use a firm grip to ease the edge into the cutters until
stopped by the collar (Fig. 32).
2. Keep pushing straight while turning and feeding the
work piece, continue until the cut
the off position and remove the work
piece only once the cutters have
NEVER PERFORM ENCLOSED EDGE SHAPING WHEN
THERE IS LESS THAN 12" OF WOOD MATERIAL ALL
AROUND THEOPENING ! THE ONLY TIME THIS CAN BE
DONE IS IF THE WORK PIECE IS ATTACHED TO A
LARGER WOOD BASE!
TEMPLATES
A template serves as guide for the cutter. The
template must be made
a
collar, recommended size 3/4". (Fig. 33)
MULTI-PIECED TEMPLATES
workplace
template
ATTENTION !
NEVER PERFORM ENCLOSED
HAPING WHEN WORK PIECE
OPENING IS MALLER THAN TWICE
THE DIAMETER IN ANY
DIRECTION
Summary of Contents for 40-350
Page 17: ...BASE...